WCPT8 Keynote Speakers
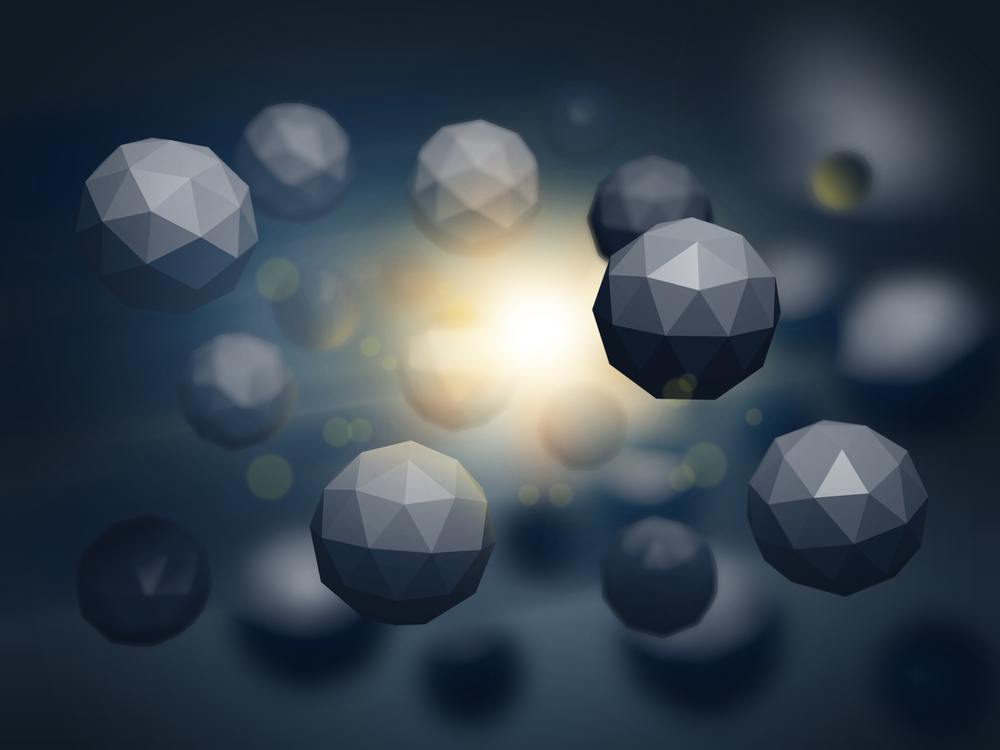
- Particle & Bulk Powder Characterization
- Particle Interactions
- Philip Chi Lip Kwok, The University of Sydney
- Particle Design
- Chika Takai, Nagoya Institute of Technology
- Wolfgang Peukert, Friedrich-Alexander-Universität Erlangen-Nürnberg
- Handling & Processing of Granular Systems
- Particle & Nanoparticle Functionalization
- Jeffrey Elam, Argonne National Laboratory
- Guo-Sheng Gai, Powder R&D
- Particle Classification
- Wu Chen, The Dow Chemical Company
- Michael Kraxner, MCI - The Entrepreneurial School
- Fluidization & Multiphase Flow
- Allan Issangya, Particulate Solid Research, Inc.
- Poupak Mehrani, University of Ottawa
- Ronald W. Breault, National Energy Technology Laboratory
- Mayank Kashyap, SABIC
- Charles A. Petty, Michigan State University
- Takuya Tsuji, Osaka University
- Sreekanth Pannala, SABIC
- Applications for Sustainable Energy & Environment
- Liang-Shih Fan, The Ohio State University
- Hamid Arastoopour, Illinois Institute of Technology
- Rustom Billimoria, ExxonMobil
- Particle-Based Separations
- James Ritter, University of South Carolina
- Christoph Mueller, ETH Zürich
- William Heumann, Heumann Environmental
- Andrew Tong, The Ohio State University
- Applications of Particle Technology for Pharmaceuticals
- Jennifer Sinclair Curtis, University of California, Davis
- Benjamin Glasser, Rutgers University
- Chris Sinko, Bristol-Myers Squibb
- Applications of Solids Processing Unit Operations
- Wolfgang Peukert, Friedrich-Alexander-Universität Erlangen-Nürnberg
- Stefan Heinrich, Hamburg University of Technology
- Special Topics in Particle Technology
- Raffaella Ocone, Heriot-Watt University
- Timothy Bell, DuPont
- Education
- Shankar Subramaniam, Iowa State University
- Combustible Dust Safety
Particle Interactions
Electrostatics of Dry Powder Aerosols for Inhalation
Philip Chi Lip Kwok, Faculty of Pharmacy, The University of Sydney
Electrostatics of pharmaceutical aerosols for inhalation is a relatively new research area. Particle charges have been proposed to potentially influence deposition in the lungs but no conclusive in vivo data have been reported. Investigation of the relationship between the formulation and aerosol charging is required to further explore this area. The modified electrical low pressure impactor (ELPI) and bipolar charge analyser (BOLAR) have been used to measure the size and electrostatic charge of particles generated from dry powder inhalers (DPIs). DPIs are commonly used to deliver drugs to the lungs. The powder is dispersed by the inhalation effort of the patient. Net charges are generated through triboelectrication during aerosolisation. These charges were found to be formulation- and humidity-dependent [1, 2], as well as bipolar [3, 4]. The knowledge gained may be useful in the development of pharmaceutical aerosols and pulmonary drug delivery in the future.
Particle Design
Design of Nano/Micro Structures of Hollow, Skeletal, and Porous Particles
Chika Takai, JSPS Research Fellow, Nagoya Institute of Technology
Hollow silica nanoparticles exhibit unique properties such as thermal insulation, transparency, light diffusion, and so on which are derived from hollow interior surrounded by a silica shell. In order to improve these properties more, control of the silica shell structure in micro- and macro-level is important. The hollow nanoparticles are mainly prepared by template method, in which silica coating is performed on the solid or soft template surface and then the template is removed by chemical etching. Previously, gas adsorption analysis indicated that micro-pores (<2 nm) existed in the silica shell where molecules can pass through. Using the structure, selective deposition of tin oxide nanoparticles inside or outside the silica shell has been achieved. In addition, apparent density of the silica shell can be controlled between 1.45 and 2.20 g/cm^3 by adjustment of sol-gel conditions. The low apparent density of the silica shell significantly improved thermal insulation ability of the hollow nanoparticle /polyurethane film. While, macro-sized pores were also produced on the cubic shaped silica shell, by use of polarity difference in the reaction system. The skeletal silica nanoparticles have mostly hollow which divided by 12 silica nanoframes and are expected to protect organic substance (e.g., phosphor) from external stimuli. How to control micro- to macro-structures of hollow silica nanoparticles and how these functionalities have been achieved are discussed.
Unifying Principles of Product Design
Wolfgang Peukert, Professor, Institute of Particle Technology, Center of Functional Particle Systems, Friedrich-Alexander-Universität Erlangen-Nürnberg
Our mission is to address grand challenges in particle science and technology. These are related to the formation, processing and application of particulate systems along the five dimensions of size, shape, surface, structure and composition. Today, unit operations and product design are the two most important pillars of chemical engineering. Product design is the formation, formulation, handling, manufacturing, and characterization of complex multiphase products with specific properties. The applications define the required product properties which cover both classical fields of process technology in the chemical industry as well as new emerging fields of electronics, energy and environmental technologies, life sciences, materials science and engineering, nanotechnology, and photonic technologies highlighting the broad relevance of mesoscale science. The following five unifying principles of particulate product design are proposed which are widely applicable to many different kinds of products including solid, liquid, and even gaseous particles: i) Particle formation by top-down and bottom-up approaches, ii) interactions between the building blocks, iii) structure formation by self-organization and by transport processes, iv) characterization along the process chain, v) multiscale modelling and simulation. Results from the Erlangen Cluster of Excellence “Engineering of Advanced Materials” show that the joint venture of chemical engineering with materials science in concert with the basic sciences opens new prospects for all involved disciplines. In particular, chemical and biochemical engineering expands through particle technologies also in physics related fields of technology such as electronics, photonics, or 3D printing. Rigorous mathematical optimization methods based on predictive models for structure-property and process-structure functions are the key for the design of products, structures, and processes and will catalyze new possibilities for true design of particulate products.
Particle & Nanoparticle Functionalization
Atomic Layer Deposition for the Synthesis of Nanostructured Catalysts
Jeffrey W. Elam, Senior Chemist, Group Leader, Energy Systems Division, Argonne National Laboratory
Atomic layer deposition (ALD) is a thin film growth technique that uses cycles of alternating, self-limiting chemical reactions between gaseous precursors and a solid surface to deposit material in an atomic layer-by-layer fashion. Saturation of the individual ALD surface reactions and gaseous diffusion of the chemical precursors ensure that all exposed surfaces of a template become uniformly coated. These attributes, coupled with a broad palate of available materials, make ALD a versatile technique for synthesizing catalysts. Conceptually, ALD can be used to build a catalyst as a series of discrete layers which perform specific functions such as tuning the porosity, serving as the catalyst support, providing catalytic activity, and imparting thermal stability. This capability allows the physical structure and porosity of a template to be decoupled from the surface chemistry and catalytic properties. Consequently, the same catalyst can be synthesized simultaneously on a variety of templates such as a planar single crystal to facilitate detailed characterization, or a high surface area powder to boost conversion for catalytic testing.
In addition to depositing continuous layers, ALD also enables the synthesis of nanoparticles. Using ALD, the nanoparticle size can be modulated by adjusting the number of cycles performed, and the number of nanoparticles can be controlled by pretreating the surface to change the concentration of surface functional groups on which the ALD initiates. By alternating between different ALD surface chemistries, mixed-metal nanoparticles (e.g. Pt-Pd) can be formed. Furthermore, the layer-by-layer nature of ALD enables specific nanostructures for these mixed-metal nanoparticles such as core/shell (Pd/Pt or Pt/Pd) and well-mixed alloy. Finally, ultrathin ALD metal oxide layers applied after the metal nanoparticle ALD can stabilize the nanoparticles to inhibit sintering at elevated temperatures. Quite remarkably, these metal oxide “overcoats” grow selectively on specific sites on the noble metals and on the support between the nanoparticles such that the catalytic activity is maintained or even enhanced.
The R & D on Engineered Particles for Functional Materials in China
Guo-Sheng Gai, Tsinghua University, Powder R&D
This is an overview on the R & D activities of functional powder processing from the particle level. China needs this kind of technologies to support its new material industry and improving the qualities of commonly used materials.
It starts from the national policy in this 10-year action plan designed to transform the structure of processing industry and increase the quality of “Made in China”. The Key Developing Sectors are: Aeronautics/Astronautics, New Generation IT, Machine Tools and Robots, Marine Engineering, Advanced Rail Transportation, New Energy Vehicles, New Energy, and New Materials.
Particle coating and hybridization is an important approach to make functional powders. Newly developed equipment is introduced. Copper/alumina, PE/CNT composite particles are prepared. Particle shape modification is another technology to increase the powder flow-ability and higher tap-density. The technology is introduced with the analysis of the process on graphite powder process for Lithium-ion Battery Anode.
Particle Classification
The Advancement of Fluid/Particle Separation for Environmental Protection
Wu Chen, Principal Research Scientist, The Dow Chemical Company
Environmental and health protection efforts continue to be key challenges and opportunities for the scientific community. Whether the challenge is air pollution caused by the particulate matter (e.g. PM2.5), fine particle removal for wastewater discharge/recycling, or sufficient dewatering of a solid for disposal, fluid/particle separation technologies have been playing key roles and evolving over the years. Recent technology developments and the future outlook are reviewed in this presentation. For clean air, filter media development is the major focus. Advanced filtration media allow for less fuel consumption in energy generation and water purification process and, as a result, reduces emissions.
For effluent water, improvements to traditional solid/liquid separation technologies, such as clarifier design and the use of membrane filters, have allowed industries to meet more stringent regulatory requirements. In the area of solid waste reduction, innovative technologies are also being developed. A new chemical amendment for difficult to dewater tailings is highlighted as an example.
An Empirical Comparison of Two Different Cyclone Designs in the Usage of a Third Stage Separator
Michael Kraxner, MCI - The Entrepreneurial School
Background and Motivation
Actually the Third Stage Separator (TSS) in a FCC-process is mainly constructed as a standard reverse flow cyclone which can be designed by approved calculation models, as for example by using the model of Barth/Muschelknautz [1]. The FCC-process efficiency mainly depends on the cyclone performance i.e. on its separation efficiency and its pressure loss. The conical shape of the lower separation body of a reverse flow cyclone leads to high tangential velocities and therefore to high erosion which strongly affects its life time. A second cyclone type, which is not yet well investigated, is the uniflow cyclone. Its essential advantages compared to the reverse flow cyclone are its compact construction and its easy integration into pipes. A further advantage is its low pressure loss and therefore its low energy consumption. Postma et al. investigated the usage of uniflow cyclones (swirl tubes) in the FCC-Process, which requires high process reliability [2]. A study on the applicability of uniflow cyclones as a TSS was carried out in 2010 at PSRI laboratories and showed acceptable performance data for the usage within FCC-process engineering [3].
Standard Reverse Flow Cyclones vs. Uniflow Cyclones
The simplicity of design and the lack of moving parts in cyclone separators are key to their ubiquitous presence in process industry. In some applications, where high gas flow rates must be processed, the physical size of a conventional reverse flow cyclonic unit can become very large. The uniflow cyclone or axial cyclone, is a interesting alternate design, which is able to deliver comparable efficiencies in a very compact geometry. The name is derived from the flow field pattern generated inside the cyclone. Unlike reverse flow cyclone, the gas enters and leaves the cyclone in the same direction.
Compared to a reverse flow cyclone design, the uniflow cyclones can be built approximately two-third smaller in volume at comparable efficiencies. Wide spread adoption of this design has been limited by the absence of a universally accepted and validated design approach. The existing literature mainly focuses on special applications, as shown in the research work of Gauthier et al. or Zhang et al. [4,5]. The highly turbulent particle flow patterns offer a complex parameter system which makes the dimensional analysis rather complicated. For instance, numerous design variations of the inlet swirl generator (Figure 1) are possible, and each approach will result in remarkably different flow field within the cyclone. Therefore, an empirical approach is most apt for studying uniflow cyclones.
To facilitate the understanding of its operation, the design structure of a uniflow cyclone can be divided into four major sections in the direction of the flow, namely Swirl Vane Inlet, Separation Chamber, Vortex Finder and Particle Outlet.
State of the art
Even though the working principle of this cyclone type is well-known, there is hardly any literature which investigates the design, the estimated efficiency or pressure drop. To close this gap the MCI is driving systematic research activities since 2008 to improve the separation efficiency of uniflow cyclones by optimizing the geometric design [6,7,8,9]. As outcome of these activities, there are several applications established in process and automotive industry, as for example in air-pre-cleaning systems for internal combustion engines used in off-road vehicles (e.g. building and agricultural engines).
Experimental
To compare the two cyclone systems on a fair basis, the executed test series show data for efficiency and pressure drop and the erosion potential at comparable operating conditions. The experimental testing is performed on a standard reverse flow cyclone and a uniflow cyclone with various operation configurations differing from each other regarding the vortex finder diameter, the volume flow rate and pressure recovering systems. A test stand which allows comparing effectiveness and optical accessibility for phenomenological observations is set up at MCI laboratories, by using selected FCC-Powder which typically reaches the Third Stage Separator.
References:
[1] VDI Heat Atlas, 11th Edition. VDI-Book. Berlin [u.a.]: Springer Vieweg, 2013.
[2] Postma, R.S., Hofmann, A.C., Dries, H.W.A., Williams, C.P., The Use of Swirl Tubes for Dedusting, World Congress on Particle Technology 3, Brighton, UK, 1998.
[3] Kraxner, M., Muschelknautz, U., Karri, S.B.R., Cocco, R., Knowlton, T.M., Applicability of a Uniflow Cyclone as a Third Stage Separator in the FCC-Process, AIChE - American Institute of Chemical Engineers - Annual Meeting, Minneapolis / MN, USA, 2011.
[4] Gauthier, T.A., Briens, C.I., Bergougnou, .A., Galtier, P., Uniflow cyclone efficiency study, Powder Technology, Nr.62: 217-225, 1990.
[5] Zhang, Y., Wang, X., Riskowski, G.L., Christianson, L.L., Ford, S.E. Particle separation efficiency of a uniflow deduster with different types of dust, Transactions of ASHRAE, 1999.
[6] Muschelknautz, U., Pattis, P., Reinalter, M., Kraxner, M., Design Criteria of Uniflow Cyclones for the Separation of Solid Particles from Gases, CFB10 – 10th International Conference on Circulating Fluidized Beds and Fluidized Bed Technology, Sunriver / OR, USA, 2011.
[7] Kraxner, M., U. Muschelknautz, S. Wechner, S. Ackermann, V. Greif, J. Bolda, Influence of the Inlet Vane Geometry on the Uniflow Cyclones Performance, AIChE-Annual Meeting, Pittsburgh / PA, USA, 2012.
[8] Kraxner, M., Skarke, B., Kofler, T., Pillei, M., Pressure Drop in Uniflow Cyclones: Investigation on an Empirical Calculation Model, CFB-11, Beijing, China, 2014.
[9] Kraxner, M., Empirical Evaluation of Design Criteria’s for Uniflow Cyclones in Multicycloneboxes, Doctor Thesis, TU München, Germany, 2013.
Fluidization & Multiphase Flow
A Hydrodynamic Study of Subway Grating and Disk and Donut Trays in a 0.6-m Diameter Fluidized Bed Stripper
Allan Issangya, Particulate Solid Research, Inc.
The counter-current contacting between the down-flowing emulsion phase stream and the up-flowing bubbles stream in fluidized bed strippers is enhanced by the use of an assembly of horizontal or inclined baffles. The baffles are important because in un-baffled fluidized beds, the movement of the bubbles is unrestricted. So, as they rise, interact, coalesce and grow in size they tend to move laterally toward the center or, in some instances, the bubbles can consolidate in a jet stream that bypasses significant portions of the bed in what has been termed gas bypassing. Therefore, open beds would give too low of a mass transfer to be effective strippers. Installing baffles enhances gas-solids interaction by controlling the bubble size and improving bubble distribution over the stripper cross section. As is typical for two-phase countercurrent flow unit operations, fluidized bed strippers can also suffer from flooding at relatively high solids mass fluxes.
Literature shows that disk and donut trays give excellent stripping efficiencies. They are among the most widely-used fluidized bed stripper internals in the fluid catalytic cracking (FCC) process. Disk and donut internals are, however, expensive and prone to flooding. This study compares the hydrodynamics of simple and cheaper subway grating trays with disk and donut trays in a 0.6-m-diameter fluidized-bed stripper. The stripper column was 7.6 m tall and the test solids were FCC catalyst particles containing 8% fines, less than 44 microns. Solids flowing out of the stripper were transferred by a 0.25-m-diameter, 3.4-m long vertical standpipe to a 15-m tall, 0.3-m-diameter riser that conveyed the solids back to the stripper via primary and secondary cyclones. The measurements performed in the study included differential pressure and local bubble properties.
Results showed that the subway grating stripper built a higher-pressure head, operated more smoothly without flooding over a wider range of operating gas velocities and solids fluxes compared to the disk and donut stripper. Literature studies showed, however, that the stripping efficiency of subway grating tray strippers is significantly lower than that of disk and donut strippers. Therefore, while hydrodynamics suggests a superior subway grating stripper, the future challenge will be to find ways of raising its stripping efficiency. Installing more subway grating trays in the same vertical height will most likely improve stripping.
Particles Wall Coating Due to Electrostatic Charge Generation in Gas-Solid Fluidized Beds in Turbulent Versus Pre-Turbulent Flow Regimes
Poupak Mehrani, University of Ottawa
Ronald W. Breault, National Energy Technology Laboratory
Risers in gas-solids circulating systems are used extensively in the petrochemical and energy industries as well as being proposed for advanced technologies from chemical looping combustion/gasification. The performance of these units has been linked to the meso-scale and the dynamic behavior of the flow field. New experimental data has been obtained in a 0.1 m diameter riser with a 5.3 m height. The particle is an 850 µm high density polyethylene with a density of 860 kg/m2. Experiments were conducted primarily in the core-annular regime. In addition to standard differential pressure measurements along the riser, three-dimensional measurements of the solids volume fraction were obtained using a Tech4Image Electrical Capacitance Volume Tomography (ECVT) system. The dynamic structure of the riser solids fraction is obtained by analyzing the time series data for each voxel in the flow field. Specifically, the data were analyzed using higher level statistics (skewness and kurtosis) as well as chaotic correlation dimension and the entropy. These values are compared with published ECVT data using the same material from a 0.3 m diameter riser with a 16 m height. The effect of system scale is analyzed and discussed.
Improving Circulating Dehydrogenation Technology through Optimization of Fluidization
Mayank Kashyap, SABIC
Charles A. Petty, Michigan State University
An Idea of DEM-CFD Coupling Model Decoupling Spatial Averaging Scale from Computational Cell Size
Takuya Tsuji, Osaka University
DEM-CFD coupling model is widely used for the numerical simulation of dense gas-solid flows. Because it is a mesoscopic approach, fluid motion is obtained by solving spatially-averaged continuity and momentum equations. It is usual that computational cell size used for CFD calculation is same with the spatial-averaging scale of governing equations and the results obtained by the model can change depending on the computational cell size. Fine computational cell is desired for accurate CFD calculation, on the contrary, sufficiently large averaging scale is required to fulfil the requirement of spatial averaging. These are contradictory and it is important to adopt a proper cell size carefully to obtain reasonable results. It could be a big problem in the case particles with different size exist and particle size changes over time and position.
In the present study, an idea of DEM-CFD coupling model that decouples spatial averaging scale from calculation cell size used for CFD calculation is discussed. We present the concept of proposed model first and develop discussions on its feasibility and validity.
The Divide between Academia and Industry in Modeling Gas-Solids Reacting Flows
Sreekanth Pannala, SABIC
I will present such an approach using a gas-phase fluidized bed polymerization reactor as an example. First, I will provide an overview of the various models currently used at the different scales in gas-solids reacting flows. The coupling across the scales will be introduced through few different approaches:
- Discrete-Continuum Coupling using Discrete Element Method for particles
- Upscaling data from Discrete Element Modeling results to continuum based Computational Fluid Dynamics (CFD)
- Upscaling information from CFD to simplified reactor network models
In conclusion, the presentation will elucidate the approaches and opportunities in bridging the gap between academic advances and industry needs to model and advance our understanding of gas-solids reacting flow reactors.
Applications for Sustainable Energy & Environment
Chemical Looping Combustion, Gasification and Reforming – Particle Technology Perspectives
Liang-Shih Fan, Distinguished University Professor and C J Easton Professor, The Ohio State University
The concept of chemical looping reactions has been widely applied in chemical industries. Fundamental research on chemical looping reactions has also been applied to energy systems. Fossil fuel chemical looping applications were used with the steam-iron process for coal from the late 1800s to early1900s and were demonstrated at a pilot scale for synthetic natural gas production with the IGT HYGAS Process and the CO2 Acceptor Process in the 1960s and 1970s. There are presently no chemical looping processes using carbonaceous fuels in commercial operation. Key technical factors that determine commercial viability of the technology lie in the sustainability of the reactivity and recyclability of the metal oxide oxygen carriers and the ability of configuring the reactor assembly for optimal operation and control of the solids flow system. The chemical looping system is developed on the circulating fluidized bed platform. The successful deployment of this technology requires thorough knowledge of two interconnected fields, i.e., metal oxide reaction engineering and particle science and technology. With now CO2 emission control of great concern and process conversion efficiency enhancement of great interest, activities on research and development of chemical looping technology have resurfaced.
Specifically, chemical looping technology is a manifestation of the interplay among such key elements of metal oxide reaction engineering and particle science and technology as particle synthesis, reactivity and mechanical properties, flow stability and contact mechanics, gas-solid reaction engineering and particulates system engineering. This presentation will describe the fundamental and applied features of modern chemical looping technology in the context of the circulating fluidized bed platform that utilizes fossil and other carbonaceous feedstock. It will discuss particle reaction engineering represented by reaction chemistry, ionic diffusion mechanisms, metal oxide synthesis and thermodynamics, reactor design, and system engineering along with energy conversion efficiency and economics of the chemical looping processes for full and partial or selective oxidation for electricity, fuel and chemicals production. The Ohio States University has developed a number of advanced chemical looping combustion, gasification and reforming processes which will be highlighted in this presentation. Potential for solar based chemical looping technology will also be discussed.
Creating a Pathway to Sustainability: The Critical Contribution of Particle Technology Research
Hamid Arastoopour, Henry R. Linden Professor of Engineering, Illinois Institute of Technology
Maintaining adequate future supplies of energy and water requires the creation of a pathway to sustainable energy and water that is both multi-faceted and complex. An effective pathway aims to improve the reliability, security, and affordability of energy and water by: utilizing a least-cost strategy to reduce the negative impact of energy consumption on climate change and water availability; emphasizing the gradual decarbonization of the global energy system; increasing energy efficiency and conservation; and preserving natural resources and the environment.
A successful pathway to sustainability must include short-term, transitional, and long-term plans that must be launched simultaneously. This presentation will discuss the critical contribution of particle technology research to the successful implementation of these plans.
The role of circulating fluidized bed (CFB) research in carbon capture processes and particle pulverization as a recycling tool for polymeric and elastomeric materials as examples of the short-term plan will be presented.
As an example of the transitional plan, the impact of fluid-particle flow and computational fluid dynamics (CFD) research in the production of natural gas from unconsolidated hydrate reservoirs will be discussed.
The contribution of particle technology to the long-term plan, including the effect of rain droplets on wind turbine performance and the role of the fluid-particle mixture as a very effective heat transfer medium for concentrated solar power (CSP) systems will be presented.
Energy Outlook, A View to 2040
Rustom Billimoria, Dean and Professor, ExxonMobil
Particle-Based Separations
On the Use of Structured Adsorbents in Pressure and Temperature Swing Adsorption Processes
James Ritter, Carolina Distinguished Professor, University of South Carolina
The use of strucutred adsorbents in PSA and TSA processes has been suggested for many decades. However, there has been limited commercialization. This is rather surprising since much has been patented and published on this topic. In this presentation an overview on the use of strucutred adsorbents in PSA and TSA processes will be given. Examples will be taken from commercial processes, the patent literature, journal articles and the authors' own experiences with strucutred adsorbents in their adsorption process laboratory.
Chemical Looping for Reactive Separation
Christoph Mueller, Associate Professor, ETH Zürich
In this talk we will report on challenges and recent advances in calcium oxide based CO2 sorbents (calcium looping). Alkaline earth metal oxides, such as CaO and MgO are an interesting class of CO2 sorbents as their theoretical CO2 uptake is very high. However, to obtain materials that show a high CO2 uptake over many capture and regeneration cycles the structure and surface properties of the materials have to fulfill a number of criteria. As alkaline earth metal oxides capture CO2 at elevated temperatures, these CO2 sorbents can be integrated into catalytic processes. The so-called sorbent enhanced steam methane reforming will be presented as an example.
A New Theoretical-Empirical Model for Cyclone Design
William Heumann, Senior Scientific Advisor, Heumann Environmental Company
One of the theoretical bases for many cyclone design methods is the work of E. Feifel. One of those who continued and improved upon Feifel’s work was G. Miczek. Although some of Miczek’s work was published (two in Czechoslovakia and one in Chem. Eng. in conjunction with C. Doerschlag), most was not, and has been held as proprietary by my current (and past) businesses for commercial benefit. After 40 years of work within this field, benefitting from Miczek’s work, I wish to give credit to Miczek for his work by sharing it with the scientific and industrial communities.
The method is initially based upon the Vortex Theory described by Feifel and others. This describes a vortex of maximum tangential velocity at some radius that is a function of the over-all geometry of the cyclone. While the diameter of the cyclone itself is a variable that affects the location and magnitude of this “Core Vortex” velocity, it is, contrary to popular belief, by no means the most significant variable. The Core Vortex velocity magnitude and position is more strongly a function of the inlet size, arrangement and location, as well as the gas outlet diameter. The magnitude of the Core Vortex tangential velocity is not only the primary measure of the inertial forces available for particle separation but also the primary contributor to cyclone pressure drop.
At the highest level, there are two primary methods for increasing cyclone separation efficiency:
- Increase the centrifugal force (defined as the opposite of centripetal force): i.e. increase the tangential velocity at a given radius or decrease the radius at a given tangential velocity of the flow stream that is transporting the particle.
- Provide for a greater amount of time for the particle to be transported to the collection point before the flow stream exits the cyclone.
Miczek’s contributions can be summarized as a method that determines what he calls a “Specific Flowrate” for any given cyclone. This Specific Flowrate should be more properly defined as Specific Velocity which is defined as the average one directional gas flow velocity of a cyclone at some defined standard conditions. These standard conditions include the pressure drop across the cyclone. This approach of comparing Specific Velocity of various cyclones at standardized conditions and pressure drop allows for a description of “cyclone quality” that considers the cyclone pressure drop, capacity, Core Vortex Velocity and radiuses well as a measure of the cyclone residence time.
While cyclones are relatively simple to construct, the accurate prediction of their performance remains quite challenging and difficult for most engineers. By combining Miczek’s theoretical model with the empirical corrections he developed, an accurate predictive model for cyclone pressure drop and fraction efficiencies was achieved. We have been able to refine and improve the coefficients of Miczek’s empirical corrections as we have successfully designed hundreds of cyclones used in commercial and research applications with negligible (minimal?) error in predicted pressure drop and fraction efficiencies. The intent of this paper is to describe in detail the theory, research it is based upon, and provide guidance for the continued refinement of the empirical coefficients by others who wish to utilize this method.
Demonstration of High Temperature and Pressure Gas-Solid Circulating Chemical Looping Reactor Systems for Syngas and Heat Generation – Particle Reaction Analysis and Pilot Scale Test Results
Andrew Tong, The Ohio State University
Applications of Particle Technology for Pharmaceuticals
Toward Simulation-Based Design of Pharmaceutical Processes
Jennifer Sinclair Curtis, Dean and Professor, University of California, Davis
Particle and fluid-particle simulations have been widely used to model a range of processes across many industries. This presentation will review application of simulations to common pharmaceutical processes including material transport and storage, blending, granulation, comminution, compaction, coating, and die filling. In many cases, simulations enable detailed analysis and flow visualization which provide insights into the effect of material properties and operating conditions promoting new designs and innovations and reducing inefficiencies and cutting costs associated with additional experimentation and scale-up studies.
Additionally, this presentation will review some computational models and techniques common to simulations involving particles. Recent advances in fluid-particle and particle models have significantly expanded the range of pharmaceutical systems and processes that can be described. Some of these advances include the modeling of particle mixes with wide variation in size, particle roughness, particle friction and particle cohesivity due to van der Waals or liquid bridging forces. Other model extensions include descriptions for particle aspericity that can also allow for particle breakage and flexibility. All of these complexities considerably affect the processing behavior of the particles. For example, surface moisture results in particle agglomeration, as is well known, but the particle aspect ratio determines the size and packing (solids volume fraction) of the agglomerates that are formed and the force required to convey or blend the particle mixture. And, when the solid volume fraction approaches the maximum packing density, the particle friction coefficient can be a more dominant factor than the liquid bridge force in determining the solid-phase shear stress.
Novel Technologies to Improve the Bioavailability, Content Uniformity and Manufacturing of Pharmaceuticals
Benjamin Glasser, Professor, Director, Pharmaceutical Engineering Program, Director, Catalyst Manufacturing Center, Rutgers University
Approximately 65% of all prescription drugs are manufactured as solid dosage forms, which includes tablets and capsules. For very potent drugs, the amount of Active Pharmaceutical Ingredient (API) in the solid dosage form can be as low as 0.1% by weight. This very low API loading poses one of the biggest challenges in pharmaceutical product development: the control of dose uniformity. Low API content variability in the blend are highly desired and strictly enforced by the U.S. Food and Drug Administration. Another challenge in product development is that about 40% of newly discovered drug compounds have poor solubility which subsequently affects their bioavailability. An important aspect of pharmaceutical process development is the final product cost. As pharmaceutical companies strive to develop more affordable drugs, any possible elimination of lengthy and expensive unit operations becomes commercially advantageous. One group of such unit operations is associated with the control of API attributes (size, size distribution, shape, bulk density, etc.). These unit operations can include crystallization and various milling steps. The need for control of API attributes is solely dictated by the drug product development and usually is associated with desired improvements in blend uniformity or release profile. Having a formulation process that can make these and other steps unnecessary can provide a large advantage to pharmaceutical companies. In this talk, we will discuss a manufacturing method for solid dosage forms using fluidized bed impregnation of APIs onto porous excipients (inactive filler powders) that can potentially address all of the above challenges in drug substance and product development.
Fluidized bed impregnation can be summarized as the combination of three distinct processes taking place simultaneously. These include fluidization of the porous carrier, spraying API solution within the bed, which penetrates the excipient due to capillary forces, and drying of the porous particles causing the API to be deposited within. In this talk, we will present results showing that this process can deliver powder with high blend uniformity and tablets/capsules with high content uniformity. In addition, we show that the final API loading is not limited by its solubility in the organic solvent. Our results also show that fluidized bed impregnation does not depend on the nature of the API but rather on the nature of the excipient used. The product is an excipient impregnated with API that has flow properties that depend on the excipient and not on the physical properties of the API. In addition, we show that the product that is produced can significantly increase the dissolution kinetics of poorly soluble APIs. Implementing fluidized bed impregnation in drug manufacturing could allow for significant cost savings due to elimination of several unit operations.
Particle Technology Impact on Pharmaceutical Product Performance and Process Design: Past, Present and Future
Chris Sinko, Senior Vice President & Head of Product Development, Bristol-Myers Squibb
At the center of pharmaceutical product development lies the needs of patients. Each time a patient takes a drug, the patient expects consistent product quality and performance. These attributes are, in large part, determined at the product and process design stage. In recent years, particle technology has played a key role in advancing science-based approaches to product and process design shifting away from traditional empirical approaches. These science-based approaches drive efficiency and innovation in product development improving the pharmaceutical industry’s ability to meet the patient’s needs. Today particle technology applications span the drug development life cycle, from early stage materials characterization, to mid-stage product design and late stage process development and scale-up. This talk will present an industry perspective on how particle technology has transformed the product development paradigm. Real-world industrial examples will be presented. Current gaps and opportunities for future innovations will also be presented.
Applications of Solids Processing Unit Operations
Particles in Contact: The Key Challenge in Solids Processing
Wolfgang Peukert, Professor, Institute of Particle Technology, Center of Functional Particle Systems, Friedrich-Alexander-Universität Erlangen-Nürnberg
One of the grand challenges in Particle Technology is how to characterize the contact mechanisms and contact forces between particles. Mechanical particle properties are the key parameters in discrete element models (DEM) which have been developed during the last decades and gradually reach “predictive power”. Here and in many other aspects of Particle Technology, it is helpful to distinguish between process and materials functions. The process functions describe the effects of external parameters such as energy input, rotor revolution, machine geometry on the motion and stresses acting on particles in the process. As a result, the particles in the process or in the machine (such as mills, mixers or granulators) are stressed by these external forces and react accordingly depending on their material properties. In order to make DEM truly predictive, intrinsic material properties such as Young’s modulus, hardness, plastic deformation or fracture toughness of the particles must be known quantitatively. For instance, we have shown how to model packing densities of glass beads as a function of particle size in dependency of intrinsic material properties. However, measured particle properties (and their distributions) are only known in a few rare cases.
The (nano-)mechanics of particles across all length scales down to the nanoscale are highly relevant for many applications including adhesion, friction, powder flow, comminution and tribology. Particular interesting new fields are additive manufacturing and 3D printing which “promise” a revolution in industrial manufacturing based on powder technologies. Nanomechanical elastic and inelastic particle properties have been measured systematically in a novel nanoindentation device installed within a scanning electron microscope to obtain simultaneously force-displacement information and optical images of deformed and broken particles. Quantitative data of intrinsic particle properties (and their respective distributions) are derived with high statistical relevance from force-displacement curves of single oxide, metal and polymer particles. The force-displacement of well-defined model particles can be used to obtain so far unknown distributions of stress energy and stress number distributions in mills and other solids processing devices. Finally, we show how novel 2D materials such as graphene, MoS2 or BN can be produced by scalable mechanical delamination. Here, the challenge is also to characterize the delaminated nanosheets which is accomplished by advanced ultracentrifugation techniques. All these results are discussed in the context of unifying principles of product design and solids processing.
Dynamic Simulation of Interconnected Solids Processes
Stefan Heinrich, Professor, Institute of Solids Process Engineering and Particle Technology, Hamburg University of Technology
1. Introduction
A novel flowsheet simulation system, aimed at the dynamic modelling of complex production processes mainly in the area of solids processing, is being developed within the Priority Program SPP 1679 “Dynamic simulation of interconnected solids processes (DYNSIM-FP)” of the German Research Foundation (DFG) since July 2013 [1]. The Priority Program consists of 29 separate projects from different German universities and is thematically divided into four main groups:
- A: Development and implementation of new dynamic models of individual apparatuses and process substeps;
- B: Calculation of material parameters and development of models to describe properties of solids materials;
- C: Development of advanced algorithms and methods for dynamic simulation of complex process structures;
- Z: Development of a novel framework for the flowsheet simulation of dynamic processes.
This flowsheet simulation framework, named Dyssol (acronym for the DYnamic Simulation of SOLids processes), is presented in this contribution. The main objective of the system is to combine models, methods and algorithms, developed within the whole SPP 1679 program, into a single modelling framework that allows performing dynamic modelling of complex process structures involving solid, liquid and gaseous phases as well as their mixtures.
2. Calculation algorithm and applied methods
The Dyssol simulation system implements a sequential-modular approach [2] (SMA), where each unit is relatively independent from others and can be computed separately by its own numerical method or calculation algorithm using an individual simulation time step. Obtained results after computation of each unit are transferred between units according to the flowsheet structure. This approach leads to a relative independence between models and provides high flexibility of the simulation system itself.
The SMA implies sequential computation of models in a certain order, so it is necessary to know all inlets of a model to start calculation. Flowsheets, which consist solely of serially connected modules, satisfy this condition by default. On the other hand, applying of SMA is complicated if there are recycle streams in a process structure. In this case a flowsheet must be additionally converted into sequential form by tearing recycle streams [3]. Tearing here means search for recycle streams and setting some initial values into them.
For the dynamic simulation a modified waveform relaxation method (WRM) [4] is used. The whole simulation time is divided into smaller non-constant time intervals, on which convergence can be reached faster. Units are solved separately on each time window using some initial guess for the solution. Calculations are repeated on the current time interval until the convergence is reached. Then, the system proceeds to the calculations on the next time window. To initialize each next time window extrapolated values from the previous time intervals are used. The number of WRM iterations, needed to reach convergence, depends on the difference between the extrapolated and actual results. A set of extrapolation algorithms has been implemented in Dyssol to initialize the first iteration on each time interval.
3. Parallelization methods
Dynamic flowsheet simulation is a computationally demanding process. Sequential-modular algorithm of the Dyssol makes it relatively easy to implement different parallelization mechanisms [4] that can significantly reduce calculation time. Several strategies are implemented in the simulation system Dyssol:
- Parallelization of basic functions of the simulation system, such as matrix transformation and mixing of material streams.
- Parallel calculation of the model itself. Feasibility of this approach depends on the particular model, and the specific implementation is the task of a model’s developer.
- Simultaneous calculation of individual time points for steady-state models. If the outlet parameters of model are independent of its internal state, and are determined only by the input parameters, model state at different time points can be computed in parallel.
- Parallel calculation of models, which are located on independent branches of a flowsheet and thereby are not directly dependent from each other.
4. Handling of multidimensional distributed parameters
One of the main challenges during the simulation of solids processes is related to the dispersity of granular materials: the solid phase can be distributed along several interdependent properties, such as size, shape, moisture content, density, etc. forming a multidimensional set of distributed parameters. On the other hand, each operation on the material flow, such as separation, mixing, agglomeration, etc. may require a change in one or more distributed parameters. In this case it may be necessary to calculate all dimensions from a multidimensional set even if the value of a single parameter had been changed. Therefore, it should be considered that during the simulation interdependency between all parameters should not be lost. This means that applying the same methods for calculation of solids as for liquid-gaseous systems is impossible or can lead to their incorrect handling.
All parameters of the granular materials are represented in the simulation system Dyssol in the discretized form. The entire interval, on which the parameter is determined, is represented as a set of shorter intervals. To describe the distribution each such interval is associated with the number or mass of particles whose parameters fall within this interval. The discretization scheme must be fine enough that the numerical errors were small compared to the accuracy of the used models.
To represent interdependency between several distributed parameters multidimensional matrixes [4, 5] are used, where the number of dimensions is equal to the number of parameters. Each cell of such matrix contains the mass fraction of the solid material with certain combination of parameters, whereas the total sum of all entities of the matrix is equal to one.
For storing of such discretized multidimensional distributed parameters a sparse data format is used. The multidimensional matrix is represented by a flat tree data structure, where each level of this tree is one of the dimensions. If there are some classes, which are empty (contain zeroes), there is no need to store data on lower levels. This approach provides an opportunity to reduce memory consumption and calculation time. For more efficient usage of this structure dimensions are arranged in such a way, that the more zeroes a dimension contains, the higher it is placed in the structure.
For correct handling of solids an approach with transformation matrices is used [4, 5]. Each cell of a transformation matrix describes the mass fraction of material that passes from one class with a particular combination of parameters to some other class with another combination of parameters. This concept allows preserving information about all parameters, even those which are not considered or not changed in the current model. Thus, instead of an explicit calculation of the model's parameters transformation matrix can be generated and applied to obtain output stream in each unit.
When using this approach, the model of each particular unit is slightly complicated because not the final distribution of parameters is being calculated, but the laws of their transformation. However, this concept ensures that all information about the distributed parameters of granular materials will be retained during the computation and properly considered.
Special Topics in Particle Technology
The Vagaries of Granular and Particle Laden Flow
Raffaella Ocone, Heriot-Watt University
In the 80s, the development of the kinetic-collisional theory for granular flow (KTGF) represented a major breakthrough in the modelling of the hydrodynamics of particulate flow: based on the analogy between solid particles and gas molecules, a kinetic theory was proposed which produced constitutive equations for rapid granular flow when binary, instantaneous and inelastic particle collisions occur. In practical situations, however, the flow of particles presents complexities that escape successful description based on the KTGF alone. Many complicated phenomena happen at the meso-scale, the scale between “small” and “large”: as an example, clusters and agglomerates are formed at a length scale between particle size and equipment size. In addition, particle-particle interactions, other than inelastic and instantaneous collisions, might occur, and more complex theories are needed to capture the observed behaviour.
The talk will describe the journey from the first rigorous effort to model granular and particle laden flow to recent theories and models to explain the vagaries observed in practical situations. Open problems, in need of a solution, will be presented and the search for a “unifying” theory will be discussed.
Scaling Up Particulate Process – Lessons from Industry
Timothy Bell, DuPont
In the 1980’s, the Rand Corporation identified challenges in the commercialization of processes involving particles. Particulate process plants took longer to start up and achieved lower production rates than expected. Not enough has changed in more than 30 years. Processes involving particles are inherently more difficult than those for liquids and gases. A consistent lack of fundamental understanding dooms industry to empirical approaches, and the sensitivity of experiments to scale and equipment configuration leads to high costs and long development periods. Modeling by the discrete element method (DEM) has not yet fulfilled its promise, especially for small particles. This presentation will provide examples of the challenges involved in some of the unit operations of particle technology, and discuss strategies for scale-up, including the use of equipment suppliers, toll processors, modeling and pilot plants to bridge the knowledge gaps. Even with such strategies, education of both the engineer and the business leader is necessary to manage expectations and appropriately allocate resources.
Education
Discovering the Fascinating World of Particle Technology
Shankar Subramaniam, Mechanical Engineering, Iowa State University
This talk will begin with a broad overview of the application areas of particle technology in the chemical process industry, and the role particle technologists play in addressing engineering problems. Specific examples of particle technology applications in sustainable energy generation and pharmaceuticals that involve nanoparticle manufacture, granular flow as well as fluidization and multiphase flow will be presented to highlight interesting and exciting aspects of this field. The intent is to assist the aspiring particle technologist in deciding “Is particle technology the right field for me?” The talk will then touch on opportunities in this education session for those interested in learning more about particle technology at all levels. The talk will then focus on the necessary techniques and skillsets a particle technologist uses in their practice, including theoretical, experimental and computational methods, and how best to deploy them in the field. It will conclude with a vision for the future of particle technology.