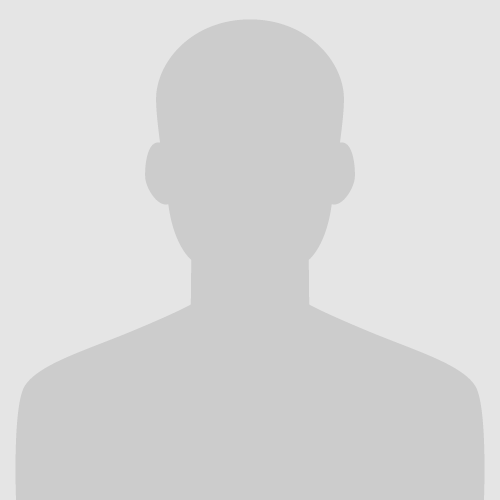
Session Chair:
- Mary Lynch, ConEdison
Session Description:
Learn more about selecting and installing process equipment such as: valves, valve actuators, safety valves, rupture discs, pumps, heaters, piping, insulation, expansion joints, anchors, supports, alarms and controls. Learn what to look for when inspecting process equipment and what is available for making repairs and upgrades.
Schedule:
PRESENTATION | SPEAKER |
---|---|
Production Plants | Nzinga Turner and Ananta Islam, GEA Process Engineering Inc. |
Specifying the Optimum Chemical Pump | Nancy Westcott, GoatThroat Pumps |
Thermoplastic Piping Systems - Material Selection | Patrick Fedor, IPEX USA |
Production Plants
Nzinga Turner, GEA Process Engineering Inc.
Fluid Bed Drying has been the chosen technology for removing water or solvents from moist powders, wet cakes and some pastes for many years. The key is to select to correct type of fluid bed for your material. There are two fluid bed technologies that will be explained in technical detail. The first is the traditional static fluid bed that can be supplied in a variety of configurations based on the feed powder properties as well as the finished product goals. Continuous fluid bed granulation, which is a take-off from static fluid bed drying, will also be discussed. The second is a vibratory fluid bed that utilizes vibration of the bed to dry and move the moist powder through the drying system. Furthermore, we will also discuss options for air-powder separation equipment downstream of fluid bed dryers.
In this presentation we will discuss GEA’s ability to examine your material to propose an effective and efficient drying system to achieve your desired final powder properties. Topics covered include selection criteria, design philosophy, typical applications, and a comparison of benefits and drawbacks of stationary versus vibratory fluid beds.
Specifying the Optimum Chemical Pump
Nancy Westcott, GoatThroat Pumps
Pumps and pumping systems are the largest consumer of electricity and are the second most frequently purchased items in the manufacturing world, but the selection process for the right pump at the right price is frequently left to others who may, or may not, have thought the job all the way through. Pump selection and ordering not only demands a thorough understanding of what the system needs to do, but it is also important to consider what impact a system will have on the overall cost to produce your product. This presentation will examine the pump selection process from a number of perspectives so as to achieve the best long-term cost-benefit and efficiency based on: the effect that different pump technologies have on the liquid and the concomitant effect that the liquid has on the pump materials; the liquid’s physical characteristics and chemical composition as it affects the materials of construction of the pump; the location of the pump whether it be an in-line or a stand-alone unit. There will also be an overview of on-line resources for understanding and selecting the materials of construction as well as active discussion groups which can help with solving on-going pump problems.