(494j) Cross-Linked “Cure Blown” Nonwoven Fibers By Simultaneous Fiber Spinning and in Situ Photopolymerization
AIChE Annual Meeting
2020
2020 Virtual AIChE Annual Meeting
Materials Engineering and Sciences Division
Polymer Networks and Gels II
Wednesday, November 18, 2020 - 10:15am to 10:30am
Micron-sized nonwoven fibers find diverse range of applications such as medical textiles, tissue engineering scaffolds, geotextiles, and filtration media. Current methods for producing synthetic nonwovens rely on transforming pre-formed thermoplastic polymers by adding heat or organic solvents to facilitate drawing, which respectively results in their high energy demands and concerns about volatile solvent emissions. Furthermore, conventional synthetic fiber manufacturing processes only use thermoplastics since cross-linked thermosets cannot flow like liquids. However, cross-linked (thermoset) fibers are an attractive target due to their superior thermal and chemical resistance. Herein, we describe a âcure blowingâ process that addresses these issues by producing cross-linked fibers at room temperature with little or no volatile solvent. In this process, a photocurable liquid mixture of reactive thiol and acrylate monomers was extruded through a spinning die resembling those used for commercial melt blowing, drawn into liquid filaments by high-velocity, ambient temperature air jets. The liquid filaments were cross-linked in flight into solidified fibers by in-situ photopolymerization (see accompanying schematic representation). Use of a liquid mixture eliminates the need for both organic solvents and heat for fiber production. The effect of process parameters on the fiber diameter and morphology was investigated to understand the limits of cure blowing. In tailoring the process to produce smaller fibers (⤠2-3 μm), two intrinsic process limits were inevitably encountered: (1) a kinetic limit dictated by the rate of photopolymerization relative to the fiber flight time and (2) a stability limit dictated by the surface tension and viscoelasticity of the monomer mixture. These limits manifest as fibers that are fused at their points of contact with other fibers or fibers that possess surface undulations and non-uniform diameters, respectively. Several strategies to suppress or extend these limits were identified and demonstrated experimentally to expand the cure blowing process window. These studies suggest the industrial relevance of this new cure blowing technique for producing cross-linked polymeric nonwovens for a wide range of applications.
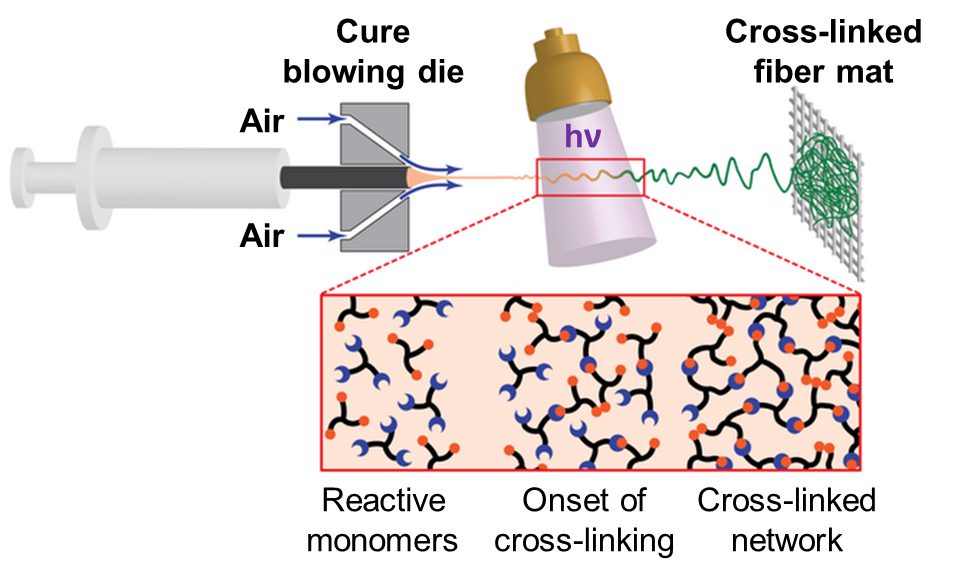
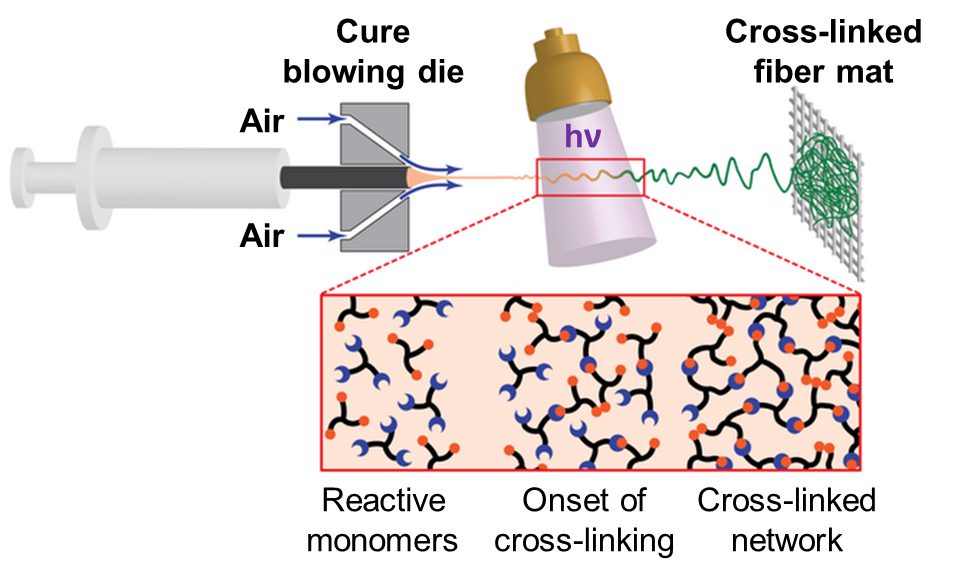
Topics
Checkout
This paper has an Extended Abstract file available; you must purchase the conference proceedings to access it.
Do you already own this?
Log In for instructions on accessing this content.
Pricing
Individuals
AIChE Pro Members | $150.00 |
AIChE Emeritus Members | $105.00 |
AIChE Graduate Student Members | Free |
AIChE Undergraduate Student Members | Free |
AIChE Explorer Members | $225.00 |
Non-Members | $225.00 |