What Is It?
Workers, at all levels and in all positions in an organization, should have roles and responsibilities for enhancing and ensuring the safety of the organization’s operations. However, some workers may not be aware of all of their opportunities to contribute. Some organizations may not effectively tap into the full expertise of their workers or, worse, may even discourage workers who seek to contribute through what the organization views as a nontraditional role. Workforce involvement provides a system for enabling the active participation of company and contractor workers in the design, development, implementation, and continuous improvement of the RBPS management system.
Effective workforce involvement involves developing a written plan of action regarding worker participation, consulting with workers on the development of each element of the RBPS management system, and providing workers and their representatives access to all information developed under the RBPS management system.
Workforce involvement provides for a consultative relationship between management and workers at all levels of the organization. This element is not intended to create a system whereby any worker or group can dictate the content of the RBPS management system; however, for workforce involvement to succeed, management must provide due and fair consideration of the input provided by workers.
Unless a reason exists for distinguishing between company employees and contract workers, the term worker, as subsequently used in this chapter, should be interpreted as referring to both groups.
Why Is It Important?
Those workers directly involved in operating and maintaining the process are most exposed to the hazards of the process. The workforce involvement element provides an equitable mechanism for workers to be directly involved in protecting their own welfare. Furthermore, these workers are potentially the most knowledgeable people with respect to the day-to-day details of operating the process and maintaining the equipment and facilities, and may be the sole source for some types of knowledge gained through their unique experiences. Workforce involvement provides management a formalized mechanism for tapping into this valuable expertise. Workforce involvement also ensures that mechanisms exist for workers to access the information they need to perform their jobs, including fulfilling their roles in support of the implementation of the RBPS management system Workforce involvement either directly implements or helps reinforce a number of the essential features of a sound process safety culture, as outlined in Chapter 3. For example:
- Individual empowerment. Workforce involvement provides explicit roles, responsibilities, and authorities for workers in the planning, implementation, and improvement of the RBPS management system.
- Deference to expertise. Workforce involvement provides a mechanism for workers to share their expertise in the operation and maintenance of the process. By having a role in helping define their training needs, workers can also help direct the enhancement of their expertise.
- Open and effective communications. Workforce involvement provides various mechanisms for workers and managers to communicate.
- Mutual trust. By enhancing dialogue and interaction between workers and management on process safety issues, workforce involvement provides opportunities for fostering mutual trust within the organization.
- Responsiveness. The manner and timeliness of management response to worker suggestions will be a primary determinant of the degree of success that can be achieved by the workforce involvement program. Slow, no, or superficial response can both cause the loss of time-critical opportunities to respond to problems and serve as a disincentive to future worker participation.
Where/When Is It Done?
By its nature, workforce involvement is associated with virtually every process safety activity, whenever and wherever it occurs. Thus workforce involvement should begin during the design of the RBPS management system and continue on through its implementation and continuous improvement. Certain workforce involvement activities may be scheduled periodically; for example, a periodic operator
opinion survey regarding the adequacy of the refresher training program. In addition, a mechanism permitting continuous input or feedback from workers should be provided as part of the workforce involvement program. Management’s responsibility for providing access to information developed under the RBPS management system provides a continuing role for management as such information is developed and modified (see Chapter 8, Process Knowledge Management).
Who Does It?
Management, with worker involvement, establishes the procedures and systems that constitute the workforce involvement element, which, in turn, describe the process for identifying opportunities for the workforce to be engaged in the development and implementation of each RBPS element. The workforce involvement procedures also establish a responsibility for workers to make suggestions for the development, implementation, and improvement of the RBPS management system and, for management to respond to such suggestions.
Management ensures that required information is available to workers under the workforce involvement program.
Finally, workers must support the workforce involvement element through their active participation (involvement) in process safety management system activities.
This chapter addresses workforce involvement as it pertains to only two groups – the company and the workers. More complex dynamics may exist at a unionized facility at which the union organization and its contract work rules will likely affect workforce involvement activities.
What Is the Anticipated Work Product?
The output of the workforce involvement element is a RBPS management system that:
- Defines the roles and responsibilities of all involved.
- Meets the current needs of all constituencies.
- Is maintained in an evergreen condition through both management attention and ongoing worker input.
- Provides workers the information necessary to understand the hazards to which they may be exposed, and to support their roles in RBPS management system implementation.
The workforce involvement element yields suggestions for the implementation and improvement of any RBPS element. Such suggestions are directed to the respective element custodians for consideration, response, and potential implementation.
Another product of this element should be the active engagement of workers at all levels of the organization, and a correspondingly greater sense of worker ownership of, and commitment to, the successful
implementation of the RBPS management system.
How Is It Done?
Implementation of the workforce involvement element normally involves (1) identification of the more common roles that workers can and should play in the implementation of the RBPS management system and (2) the establishment of mechanisms to facilitate this participation. Additional opportunities for worker involvement may be identified and formalized as the workforce involvement program evolves. The resulting working environment should be flexible enough to allow capitalizing on unexpected workforce involvement opportunities as they arise.
Table 6.1 lists general areas of activity in which workforce involvement could beencouraged, as identified by the United Kingdom (UK) Health and Safety Executive (HSE).
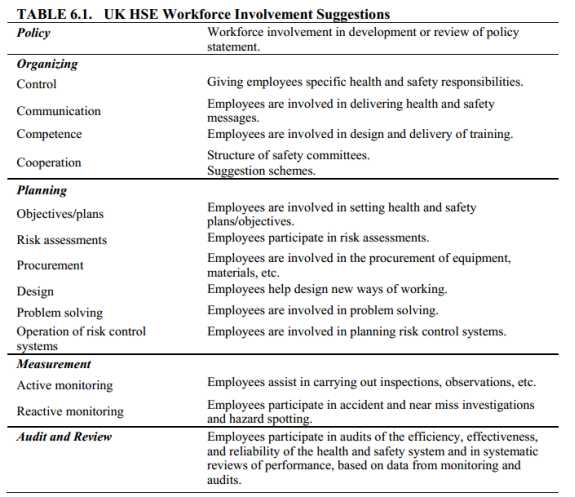
In addition, information required to be shared with workers must be identified and mechanisms established for providing this information. Employers have the right to require that workers seeking access to trade secret information sign confidentiality agreements before being given access to such information. Written policies, protocols, or procedures may be appropriate for documenting and controlling some of the activities mentioned above.
Read more
Section 6.2 of the Guidelines for Risk Based Process Safety book describes the key principles and essential features of a management system for this element. Section 6.3 lists work activities that support these essential features, and presents a range of approaches that might be appropriate for each work activity, depending on perceived risk, resources, and organizational culture. Sections 6.4 through 6.6 include (1) ideas for improving the effectiveness of management systems and specific programs that support this element, (2) metrics that could be used to monitor this element, and (3) issues that may be appropriate for management review.