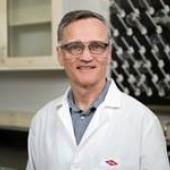
Session Chair
- Yujun Liu, The Dow Chemical Company
Session Description
Process intensification (PI) has attracted increasing attention from both industry and academia. PI refers to any chemical engineering development that leads to a substantially smaller, cleaner, safer, and more energy efficient technology. PI may involve multiple process integration, mass and heat transfer enhancement, and process simplification. It can be realized on different scales of a chemical process via, for example, new reaction routes, use of innovative solvents, novel reactors, integrated or hybrid processes, and new operating modes. This session will feature talks on practical implementations and the key aspects of process intensification.
*All session and speaker information is subject to change pending finalization
Schedule:
TIME | PRESENTATION | SPEAKER |
10:10am | Small Volume Continuous Processing for the Manufacture of Active Pharmaceutical Ingredients | Martin Johnson, Eli Lilly and Company |
10:40am | Opportunities and Challenges for Process Intensification: An Industrial Perspective | Ted Calverley, The Dow Chemical Company |
11:10am | Application of Aerospace Liquid Propulsion Technology for Process Intensification | Anthony Eastland, Gas Technology Institute |
Abstracts:
Small Volume Continuous Processing for the Manufacture of Active Pharmaceutical Ingredients
Martin Johnson, Eli Lilly and Company
Eli Lilly has recently run a 3-step fully continuous process for the cGMP production of 200 kg API. The continuous reactions, separations, and purifications were inside laboratory fume hoods adjacent to the plant feed and intermediate vessels, providing safety and containment advantages. A silylation was run in a gas/liquid PFR designed to allow off-gassing without changing the liquid hold-up volume in the reactor, while maintaining low axial dispersion. Negishi coupling and acid deprotection reactions were accomplished in PFRs designed to handle solids because of insolubilities at end-of-reaction conditions. The reactors used inexpensive, consumable tubing to eliminate cross-contamination potential. A Grignard formation was run in a CSTR because of the solid Mg reagent. The Grignard reagent was an unstable intermediate, therefore it was continuously generated and immediately consumed in the downstream coupling reaction, which was an enabling aspect of continuous versus batch for the synthetic route. A zincate formation reaction was run in a CSTR to dampen out the stoichiometry fluctuations due to deliberate cyclic flow patters from the Grignard. A quench reaction was accomplished in a CSTR because of 2-phase liquid/liquid, the potential solids entering, and surging from the gas/liquid PFR. On-line HPLC was utilized downstream from the silylation, Grignard formation, and Negishi coupling reactions. Based on the on-line LC, flow rates were adjusted to maintain high conversion, and return from divert decisions were made. Continuous extraction and back-extraction were achieved in mixer-setters in series designed to handle small amounts of solids precipitates, and to facilitate ease of stop-restart and buffering capacity for stoichiometric flow fluctuations. The final API crystallization was done continuously because a key impurity was rejected kinetically. Continuous is superior to batch for kinetic rejection because the vessels are maintained in the kinetic regime with constant steady state supersaturation, consistent mean residence time with scale up, and immediate semi-continuous filter cake washing. Slurry milling, filtration and drying of the purified API were done batch. Surge vessels were an important aspect of the control strategy. They were used at 3 locations for decoupling, simplifying startups and automation, and forward processing decisions. Numerical modeling was used for residence time distribution, surge strategy, lot genealogy, and determining allowable disturbances and pump stops. Production rate was 8 kg/day, which is a sufficient production rate for future manufacturing of this specialized medicine because of the high potency and low annual demand.
Opportunities and Challenges for Process Intensification: An Industrial Perspective
Ted Calverley, The Dow Chemical Company
Despite more than a century of developments in chemical processing, large opportunities for energy and atom efficiency remain. Increasing population means that demand for products of the industry will continue to grow, posing a challenge to shrink the environmental footprint per unit of production.
This talk will examine some of the process improvement opportunities of interest to Dow and how we have attempted to address them. In addition to highlighting some success stories, the talk will present some of the barriers we encounter when attempting to innovate and intensify process technologies.
Application of Aerospace Liquid Propulsion Technology for Process Intensification
Anthony Eastland, Gas Technology Institute
Very often technology challenges in one industry can be addressed by looking outside the industry to capabilities developed elsewhere. Process intensification can be achieved by increasing operating pressures and temperatures to increase reaction rates and/or reduce equipment sizes. Liquid propulsion for space applications has a 50 year history of developing high energy density hardware for applications where weight is at a premium. In particular, the industry developed capability for efficient high pressure combustion processes using effective injector mixing and high heat flux cooling to keep metal temperatures at acceptable levels. In addition, the industry developed low weight turbomachinery components with energy densities up to 100HP/lb. This paper will discuss how these capabilities are being applied for process intensification in the chemical, oil and gas, and power generation industries to improve efficiency and reduce cost. In particular applications in coal gasification, partial oxidation of Natural Gas, steam generation for secondary oil recovery and supercritical CO2 closed Brayton cycles for power generation will be highlighted.