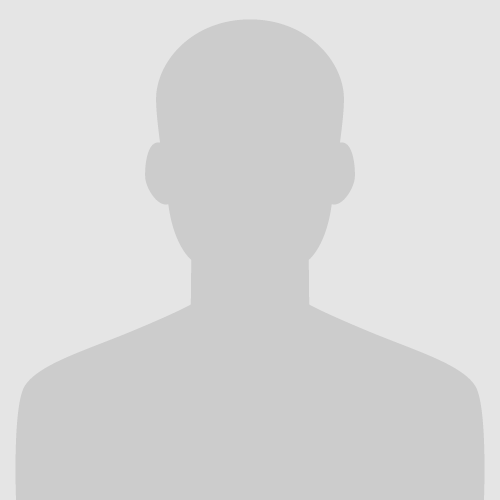
3D printing or additive manufacturing how it is called in B2B industries is evolving to a complementary manufacturing technology with continuous innovations in new materials and printing processes. In this session we will cover the first pressure safe 3D printed equipment, talk about progress in cold metal fusion and present the latest innovation in high speed volumetric processing based on photoswitchable photoinitiators.
Session Chair:
- Thomas Mörsdorf, 3Dpartzz
Schedule:
TIME (EDT) | PRESENTATION | SPEAKER |
---|---|---|
7:00 AM | Additive Manufacturing of Pressure Equipment | Daniel Urbanczyk, BASF; Matthias Wagner, BASF |
7:30 AM | Metal AM Serial Production by Cold Metal Fusion | Christian Staudigel, Headmade Materials |
8:00 AM | Xolography: A linear, volumetric technology for rapid, multiscale 3D printing | Martin Regehly, Xolo GmbH |
Abstracts:
3D-Printed Pressure Equipment
Daniel Urbanczyk, BASF; Matthias Wagner, BASF
Additive manufacturing is a new manufacturing technology to produce parts which are used in both, research and production plants at BASF. The focus is to use the new freedom of design to facilitate a more effective and efficient way of producing chemicals. The BASF division Global Engineering Services built an Additive Manufacturing Center and set up a team who has in the past 6 years been fabricating components with a main focus on metal alloys. Currently the material focus is on stainless steel and corrosive-resistant nickel-based alloys.
In process industry, pressure equipment poses particularly high technical requirements in terms of component integrity, safety and certification.
Therefore, certification is crucial for additive manufacturing to become an accepted manufacturing technology for pressure equipment.
The Technical Inspection at BASF SE in their role as Notified Body (user inspectorate) has certified an additively manufactured autoclave (PS: 225 bar, TS: 300°C) as a pressure equipment for the first time. This equipment conforms to the European Pressure Equipment Directive (2014/68/EU).
In this talk, the presenter will give an overview about the established Additive Manufacturing Center and the first operational experiences with pressure equipment. In addition, the range of available material and their qualification approaches will be introduced.
Metal AM Serial Production by Cold Metal Fusion
Christian Staudigel, Headmade Materials
Headmade Materials' new Cold Metal Fusion technology ('Metal SLS') enables Additive Manufacturing (AM) of metal components by combining the benefits of Powder Metallurgy (PM) with the opportunities of 3D printing.
In the 3D printing process, metal powders are combined with a thermoplastic binder to form a powdered feedstock that is processed into a green part on standard plastic laser sintering (LS) machines. In the subsequent step, the green part is debinded and sintered in the sintering furnace into a dense metal component.
Metal 3D printing thus makes the leap to series production of up to 100,000 components/year, running on standard machines (AM & PM) available from various manufacturers. This allows customers to scale variably from a very capital-efficient entry into the technology to high production capacities.
Other advantages include high material diversity, high green part strength, isotropic properties in the metal component, no support structures in the building process and high cost-effectiveness.
Xolography: A linear, volumetric technology for rapid, multiscale 3D printing
Martin Regehly, Xolo GmbH
Xolography is a novel technology for volumetric processing that uses photoswitchable photoinitiators activated by crossing light beams of different wavelengths. Here we demonstrate the application of the method for fast, precise 3D printing based on highly viscous polymer resins and hydrogels. Using a new light-section-based projection method, we generate complex, multi-part objects in one step. The continuous printing process produces smooth surfaces, which makes the method interesting for the production of optics and optical systems. Challenges are the optimisation of the dual-colour photoinitiators and post-processing of the objects. We finally show that the extension of the technology to the microscopic and nanoscopic size scale is possible.