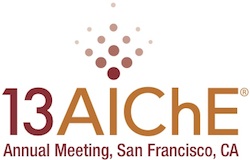
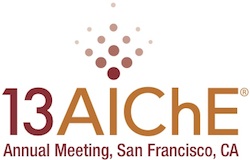
In order to dramatically reduce CO2 emissions from coal-fired power plants , and mitigate their impact on global climate change , DOE has called for technologies that can capture at least 90% of CO2 emissions from an existing coal-fired power plant with no more than a 35% increase in the cost of electricity (COE). One process design approach with the potential to achieve these goals is through the use of advanced gas-liquid contacting devices which enable more efficient capture of CO2with reduced process footprints. However , more cost-effective construction methods and rapid prototyping are needed to deploy these technologies and meet DOE goals. 3-D printing is an “additive” fabrication technique which can offer unprecedented advantages in accelerating the design cycles of gas-liquid contacting devices , minimize manufacturing costs , and expedite deployment timeline for CO2 capture in the field. Functional prototypes can be designed , fabricated and tested within a frame of 24 hours. Because the design process is entirely software-based , devices can be parametrically varied so that effects of surface area , pressure drop , porosity , etc. can be easily understood and used to develop improved devices. The rapid and flexible feedback loop between design , fabrication and testing that can only be provided through 3-D printing will more quickly advance the peformances and lower the costs of novel gas-liquid contacting devices for CO2 capture. This presentation will detail our progress in developing and applying gas-liquid contactors fabricated from 3-D printing techniques. Specifically , we will discuss the advantages , challenges and possibilities relating to solvent-based CO2 capture processes.