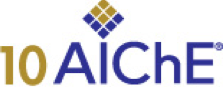
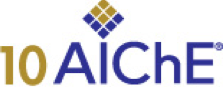
A method for adjusting spring operated pressure relief valve (SORV) inspection intervals is presented based on hazard identification, financial risk assessment, fluid service, and comparison of the life-cycle testing costs. Intuitively, longer intervals between maintenance and proof testing should tend to increase the likelihood of the catastrophic event (valve stuck shut on demand). A case study for one production facility is presented where risk quantification is broken into probability of an actual demand on the pressure relief device, probability of the valve being in a stuck shut condition, and consequences of the event. Estimates for the probability of the stuck shut condition were obtained through extensive statistical studies and modeling of Department of Energy's Savannah River Site (SRS) data and use of the Center for Chemical Process Safety (CCPS) Process Equipment Reliability Database (PERD). The probability of failure on demand for mild, moderate, and severe fluid services are derived from existing risk-based inspection technology and experience at SRS. The paper will give a graphical illustration of the lowest lifetime inspection costs versus the associated risks by using Monte Carlo Simulation and a statistical model for lift pressure growth. Analyses of anticipated financial risks are then compared to adjusted life cycle costs.