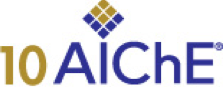
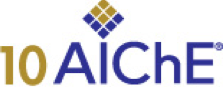
Since radiant coils operate under severe conditions of carburization, oxidation and erosion tube material selection plays an important role. Schmidt + Clemens and the R&D-institute HDZ have developed a new bench-scale unit to simulate high temperature corrosion of alloys in petrochemical plants. The unit provides the possibility to examine samples at steam cracking conditions: i. e. high metal temperatures/lower gas temperatures, low residence times in order to provide catalytic and pyrolytic coke formation (according to the coke formed in the radiant coils) and a gas mixture which is corresponding to the composition within the outlet tube of a radiant coil.
This new and unique high temperature corrosion test rig offers S+C the possibility to improve and develop centrifugal cast materials for radiant coils in a very fast and well aimed way. Therefore, the tube materials can be “tailor- shaped” in dependence of the customers needs, the specific coil design, operating conditions and feed contaminants.
Exemplary test results of conventional and experimental alloys will be presented, also a new class of the alumina forming materials– the “HT-Alloys” family: Combined with a high carburisation & oxidation resistance and excellent creep strength the alloy Centralloy® HT E was further refined for steam cracker applications by optimizing the oxide layer stability and reducing the catalytic coke formation.