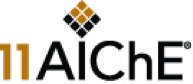
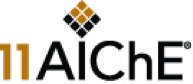
Analysis of the activity of the operator in the task of the industry requires the establishment of definitions regarding the Human Reliability, Influence Environments and, affective, cognitive and intuitive functions a connection with the job. These explanations depend on the operational and tactical point of view and can be embedded in complex systems which hamper research into the nature of human error. There nuclear types of human errors which, although identified, preventive measures may indicate the operator's task manager and acting through programs of Human Reliability and Task Analysis. The discussion on human errors is old by production management but not effective. The main efforts so far have been undertaken in the search for solutions based on equipment, process technology and management. These issues bring solutions not effective with regard to human error and can result in inappropriate projects that fail to achieve the status of &'human error-proof.&' Human factors in the current level of technology (control and automation), have been blamed for stoppages of production systems with time losses, accidents or loss of property. Statistics indicate human involvement in 85% of industry losses related to downtime of production systems. The human contribution may be even greater when taking into account that many latent failures contribute to the loss of capacity of equipment and people at work and cause loss of competitiveness in the industry The analysis of the causes of human errors in the work is highly complex due to the fluctuation of the behavior resulting of environments influence. The operator who performs the tasks of the job has variable behavior due to several factors, among them: non-availability of suitable tools and environments to accomplish the task; changes in the balance between personal and organizational goals, between individual and organizational values (commitment); and due to inherent issues in human formation for the job, emerging with motivational aspects, often, of unconscious dimension. The complexity of this analysis involves (PADOP, Figure 2): environmental aspects; types of cognitive processing that lead to specific decision models; forms of planning, executing and controlling the task; levels of knowledge and ability to implement and task analysis including verifying the demand for training for skills training; commitment to task; verification of the statement of causality techniques for failure; and verification of mentoring in the implementation of projects by providing task interface between man, the equipment and process. Chemical Industry has had Accidents with 80% of human cause and try to implement management systems (ready packages) to reduce this share. This kind of attempt is unsuccessful leading to the belief that without deep study of environments and regional mental models, it can't ensure reduction of accidents. Studies conducted and published in the Nuclear Industry (UK and USA), the Transport Services in Railway System (Virginia, USA) in Aerospace (USA), and in maritime transport projects with Nautical (Scotland) presents the following conclusion: &' The models for predicting human error in performing the task can't be trusted to consider the fluctuation of human behavior based on changing environment.&' A specialist in process losses (Paul Sharratt / UMIST) confirm that organizational and safety culture are difficulty to relate with occurrence of accidents, one sees the need to study the human factors in complex systems embedded in organizational and social environments. The business environment also reports that despite having acquired and deployed basics of HSE management technology (Dupont), it appears that in the routine actions, accidents continue to follow trends beyond the expected. Interdisciplinary groups should be formed to start work that seeks to increase Human Reliability in Technical Systems. The Analysis involves technical aspects of failure analysis: as social environments where the failure occurs on the task and human aspects (Figure 1) analysis of the structural characteristic of the individual and their relationship to specific behaviors (affective or cognitive or intuitive) for the task. The search to avoid human error in the activity of the operation lies over the non-execution of the task in a planned manner as indicated by Embrey (Technical Carman) and Lees. There are several reasons that can lead to failure in task perform, among them: the operator relies on his experience, he believes that the best manner of operation is yours. This operator performs the task according to his vision of procedure. Another possibility is the overconfidence of knowledge about the steps of the procedure then, apparently, does not need to read or to do check-list. The operator that will perform the task, and may not have participated in the planning and writing, disagreeing with the stages and times, just doing the task differently. Lees tells about the need to plan the task based on knowledge and accomplish the task-based planning relying on skill, correcting parameters and steps to measure and control the resulting state of the task. Thus, making possible the correction of procedure based on the difference between the status and the ideal state plant. The PADOP methodology (Standards and Procedures in Operation) is proposed to analyze the task including: the environments influence; the type of cognitive processing with decision models; and verification about the efficacy and effectiveness in achieving the ideal state. Some important aspects of the give importance to PADOP utilization: ? clear identification of human and technical default state to be reached; ? Inventory Analysis of knowledge based on: actual demands (causation problem) and commitment in the implementation, as written; ? Level of cooperation in Teams (written and verbal communication); ? Characteristic type of profile on the creativity and standardization in performing the task; ? Type of mental map constructed for the procedure by the operator: time, clarity, sequence, team work; ? Logic roles in performing the task and availability of tools and information; ? Interpret procedures taking into account cultural differences; and measure results to determine the efficacy and effectiveness. Some occurrence or routine cases are considered by the viewpoint of the operator and manager using concepts entered by Embrey (CARMAN), by Lees (Task Planning) and Ávila (PADOP) resulting in recommendations for action of man on the production line (environment analysis, leadership, skill, human error, and the decision task): Director, ex-operator and ex-engineer always participate in the startup of industrial plants, inhibiting the shift; improper behavior on waste disposal and cooperation in the solution; financial vision (bank) of director about reaction oscillation and practical solution, the initiative of the collective using alchemy at operation; mapping perception abilities to identify loss of vacuum in an industrial plant; purpose of disseminating research report about the fluctuations in the vacuum leading to the resolution &'does not communicated&' of root-cause; lack of cooperation and selfishness at shift turnover generating fault signals in the early stages of this work (passing the ball square to the partner); quick perception of loss of effluent through tests with solid plate polymer attacked by the solvent, becoming possible adjusts in the process and investigate the root-cause; interpreted signals allows the routine reordered hypotheses and test patterns to change; while respecting regional codes of behavior you can change patterns with reduced effort of persuasion (negotiating changes in temperature with operator panel before writing the definite statement); inspection of the feet of employees in the dressing room as contamination by direct contact with chemicals - inadequate standards; natural behavior in the appropriation by the operators of industrial specific areas to maintaining organization and cleanliness; the blame provoked by contamination can dirty worker register by HSE investigation, the necessary omission; inadequate conditions assumed in production since the departure of the plant due to unknowing about root cause of problems, the case of o-ring in alternative pumps; changing of manager leading to changing in the rituals of social inclusion causing occupational and labor instabilities; sampling deviation indicating false pattern during visit of a supervisory body (production department pressure); large solvent loss to effluent by consecutive errors and omission group conscious, social vices; director authorizes the solvent vaporization in the effluent channel to prevent high levels of contaminants (measuring by the environmental agency); probable operator with overlapping functions deflects attention from the transfer operation of wastewater and loses control sending oil into the sea; hole in the reactor generating acid gas leakage needing inspection instrument (unavailable) ? leads to &'palliative&' inadequate solution creating ethics conflict; tank liberated (instruments authorizes) to maintenance work with ?positive? signs allowing permission to work (trust the obvious) leads to explosion and death of worker; corrective action to remedy failure causes fire truck in the courtyard of death and to help drive due to rain and transshipment of dike with toluene. Key-words: task analyzes; human factors; human elements; human reliability
Presenter(s)
Once the content has been viewed and you have attested to it, you will be able to download and print a certificate for PDH credits.
If you have already viewed this content,
please click here
to login.