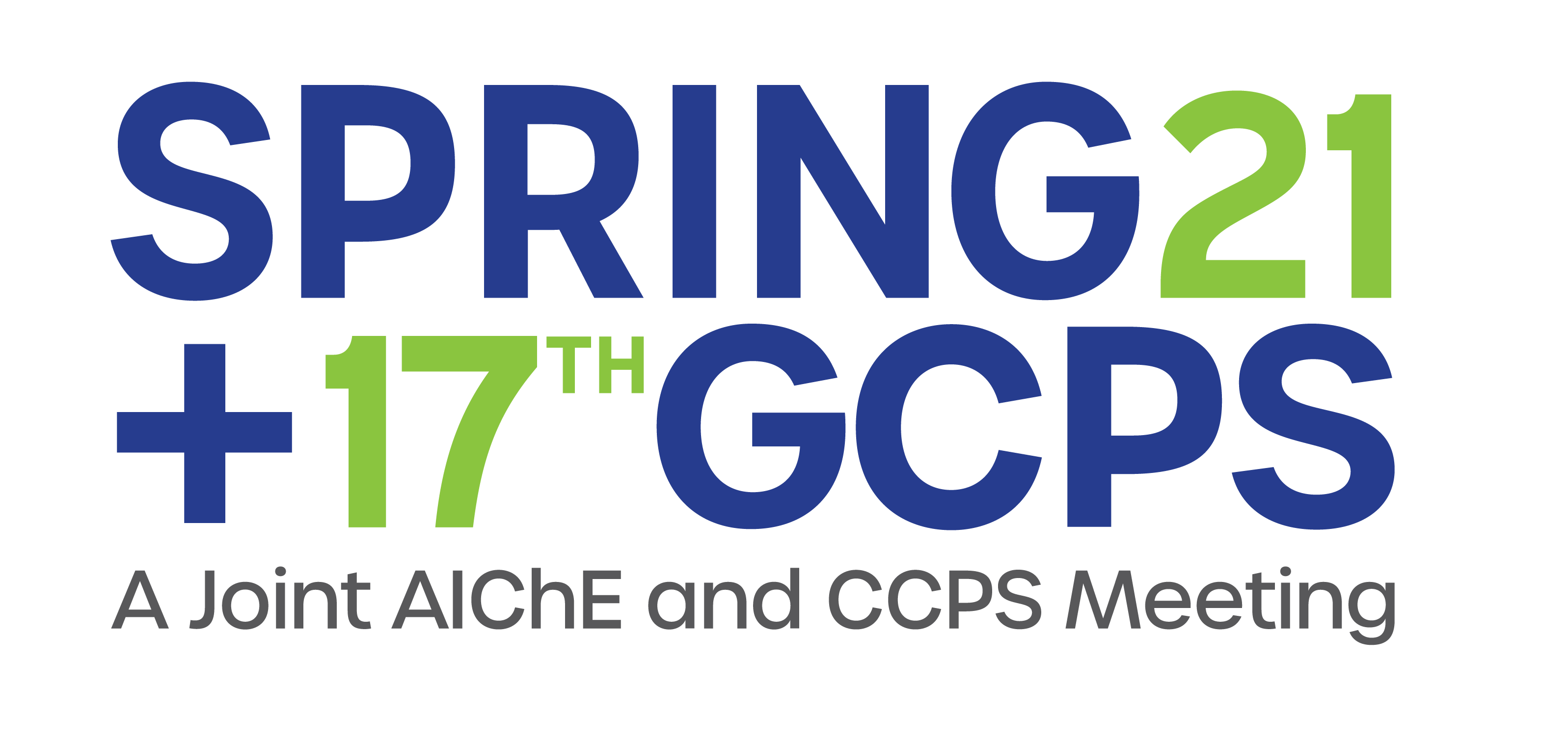
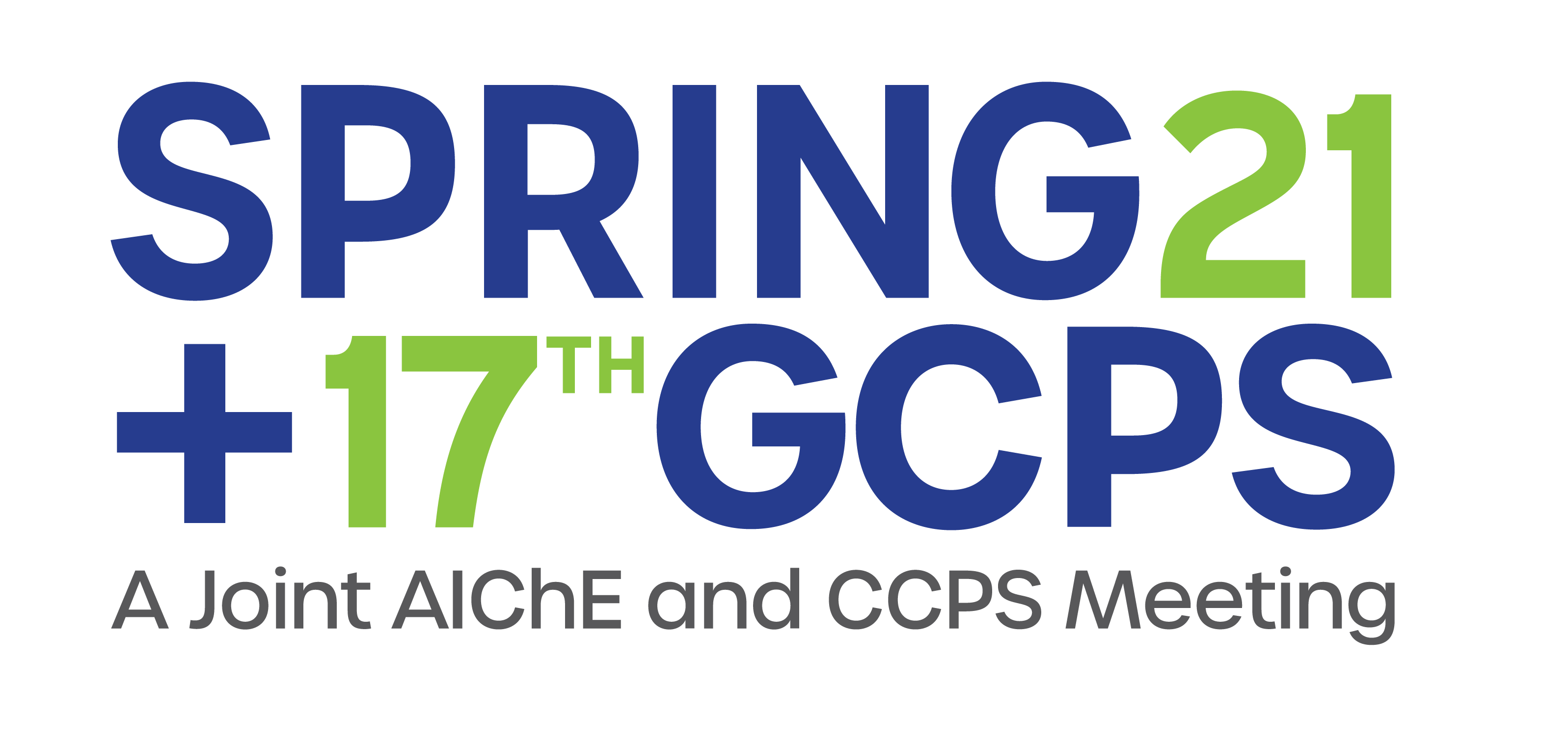
Blind risk is most often due to incomplete, inconsistent, or out-of-date asset and process safety information. Most often, these information quality issues are not obvious or visible, and as such they are a blind risk. They lie dormant, like a beartrap in the undergrowth of a forest until someone inadvertently steps on it. They become gaps in our "layers for protection" -the systems and processes we trust to stop incidents before they happen. But blind risk is also a choice, and it is a measure of a companyâs tolerance for risk.
Safety, engineering, capital, and operating decisions are only as good as the information they are based on. Most companies may not objectively know how good (read reliable and trustworthy) the quality of their underlying asset and process safety information is. It does not have to be this way.
There are two things you can do today that will have a significant impact now and into the future:
- Use standardized information quality metrics and tools to measure, monitor and report the true state of asset and process safety information across multiple repositories, applications, and formats. Let all stakeholders including executive management know the good, the bad and the ugly. Use this as a baseline to measure your improvement against.
- Monitor and quantify the cost of poor asset and process safety information. Use this information to justify funding for information quality improvement initiatives.