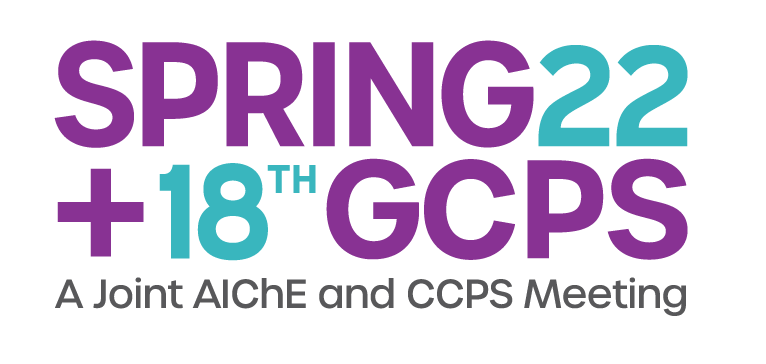
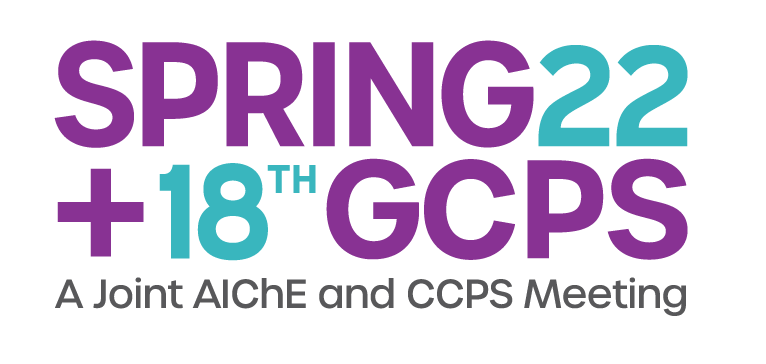
Recently, a step change in refractory ceramic fiber manufacturing technology has been achieved which redefines the insulation design and heat management capabilities imaginable for ethylene cracking furnaces. This technical paper discusses the newly developed refractory ceramic fiber in detail, along with illustrative examples of how its enhanced fiber properties of higher fiber index and lower shot content allow end users to reduce energy consumption, heat loss, heat storage, weight, and the associated insulation investment costs. Several case studies are presented which will contrast the enhanced efficiency and thermal performance benefits of the new refractory ceramic fiber material versus existing strategies for thermally insulating ethylene cracking furnaces.