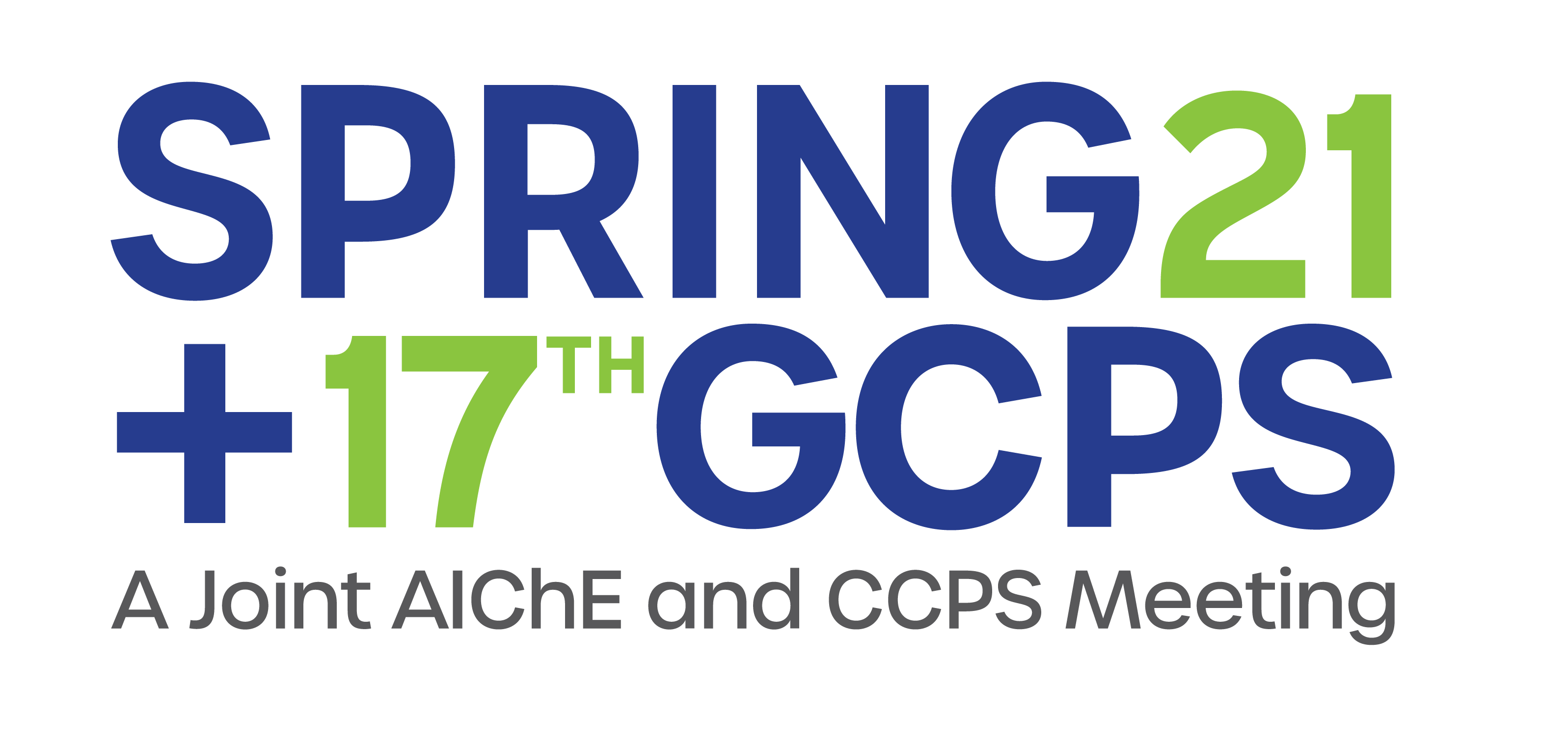
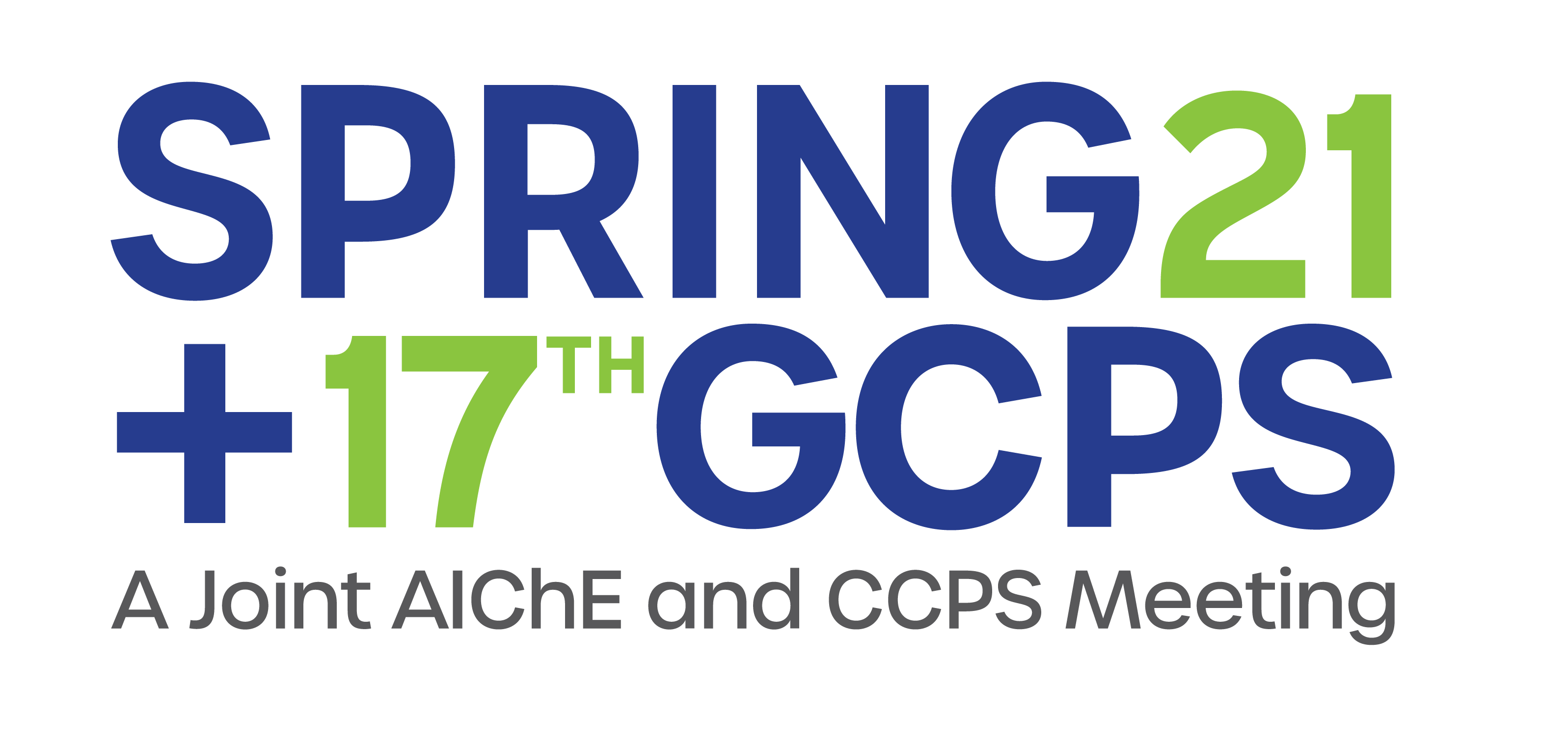
âSingle size shoe does not fit all,â sounds so much in synchrony when we want to assess risk related to powder handling. Powders, unlike liquids have varied challenges right from itâs transportation, receipt storage and handling.
Dust handling can have primarily 2 major hazards:
- Dust explosion
- Dust thermal decomposition
Few of the important parameters to understand for dust explosion are:
- Fuel characteristics of the powder:
- MIE: Minimum energy that can ignite dust cloud in the air.
- MIT: lowest temp of a hot surface that will cause dust cloud (not dust layer) to ignite.
- Particle size: Smaller size poses higher risk
- Kst: Max Rate of pressure increase. lower the kst number means the lesser severity 0 bar m/s means no risk while >300 bar m/s means high risk and bigger explosion severity.
- Ignition source:
- Hot Surfaces
- Mechanical sparks/friction
- Electrical motors/contacts
- Static electricity
Few important parameters to understand and control thermal decomposition in powders is:
- Onset temperature of decomposition
- Ageing of powders in vessels that the in process powders are handled such as Dryer, pipelines etc
- Bulk storage stability of powders
Powders have challenge in terms of dissipation of heat, sampling of representative samples and uniform temperature indication and thus control.
The case studies will focus more on common errors during defining of controls for powder handling and will focus on how preventive controls can be built in to avoid major incidents.
Sr.No |
Case Study Title |
Controls in brief |
1 |
Drying of Powders with detonation property |
Selection of right type of Dryer to ensure metal tramp is not an issue Inert atmosphere
|
2 |
Aging of powders and thus lowering of thermal decomposition onset
|
Thermal studies post commissioning to ascertain periodic cleaning of process vessels such as dryers to avoid decomposition at lower temperatures |
3 |
Handling of shock sensitive powders
|
Handling the powders in situ in inert atmosphere Ensuring that all process lines such as filter to dryer are flushed every batch Higher authority control for permit to work on such systems Avoid use of agitators for such processes. |
4 |
Handling low MIE powder formulations including drumming out |
Static charge generation is a concern. Some preventive controls to be considered are: Ensuring that drop height of powder is less than 3 mtr. Use of earthing continuity stem such as earthrite system. Ensure personnel use antistatic body protection and shoes. Use of conductive FIBC or drums Good housekeeping
|
All the above studies are based on Authorâs 10 years of experience in process hazard analysis for bulk chemical manufacturing and is expected to benefit the audience at large.