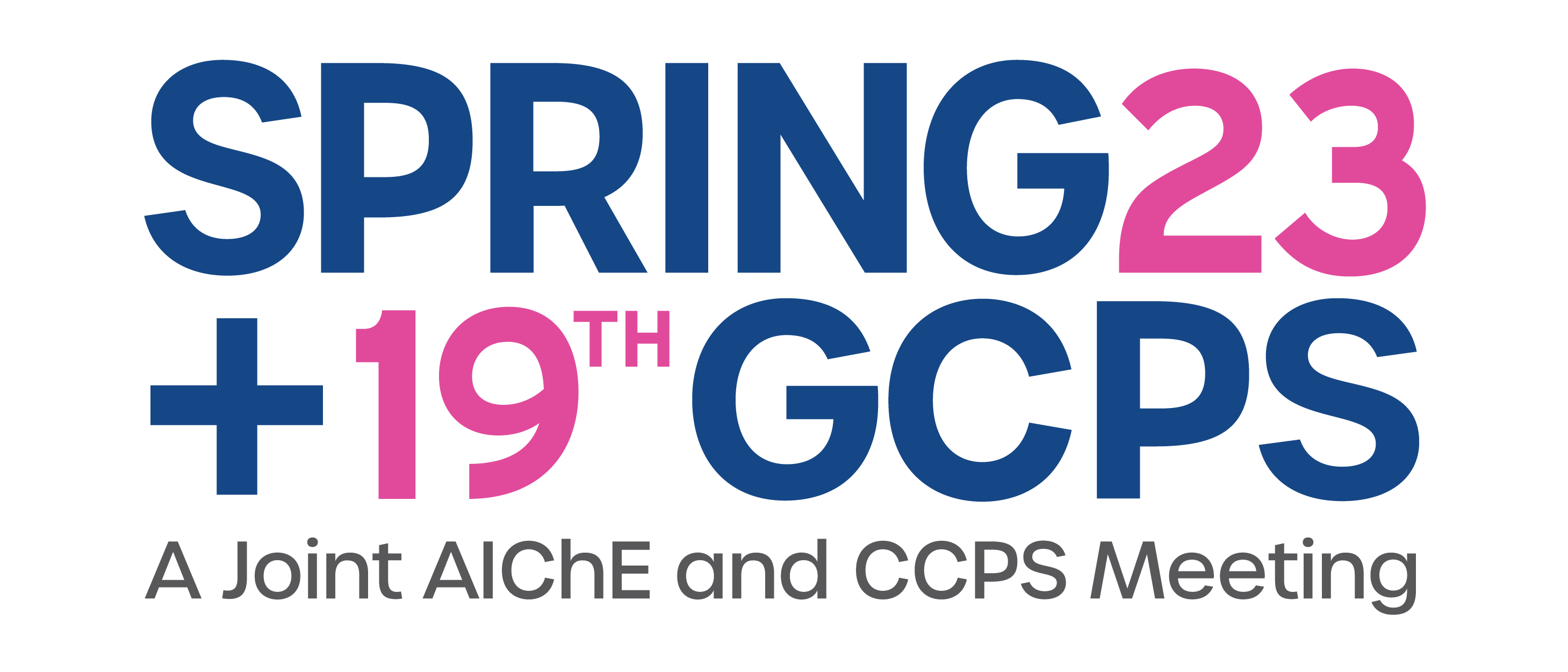
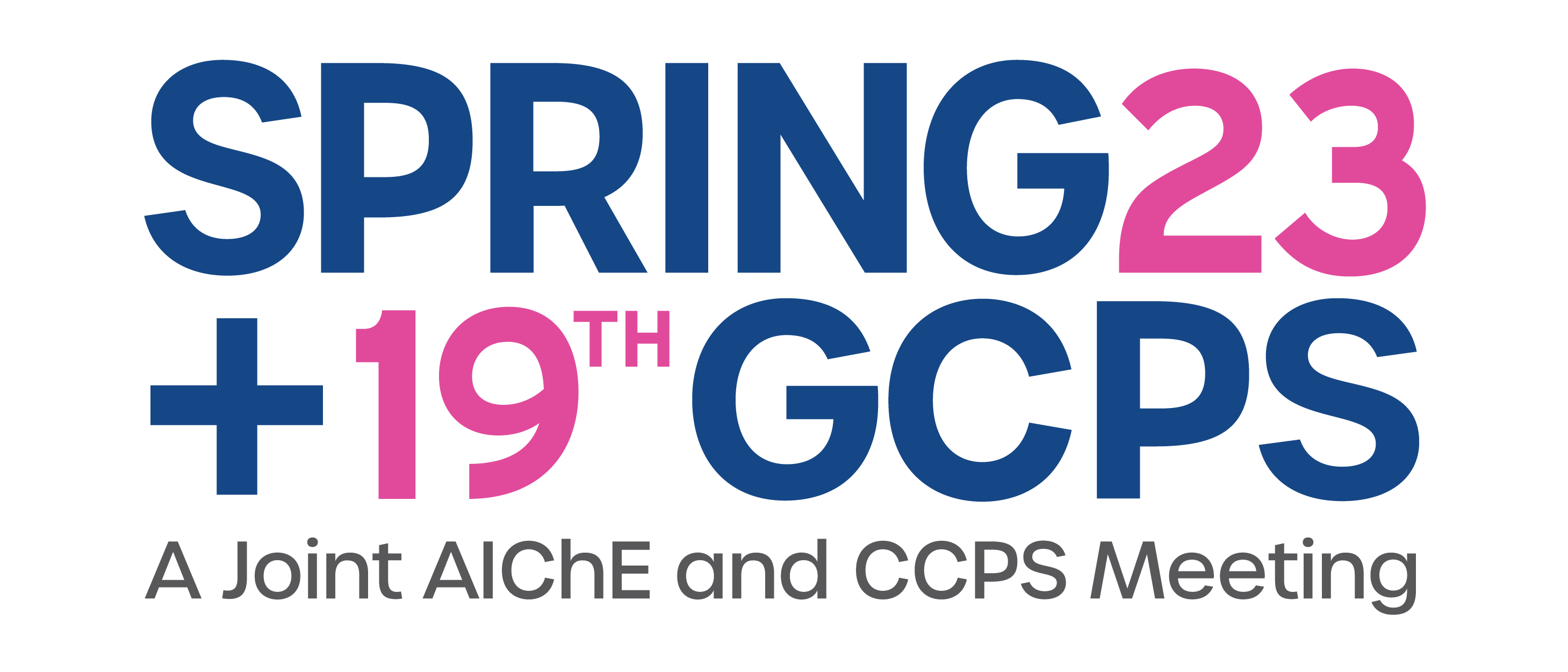
One of the largest ethylene and polyethylene production complexes in the world located in Alberta Canada was dealing with marginal reliability of the mechanical seals on their ethylene product pumps. The ethylene product pumps are classified as API 610 BB5 types and the duty conditions for the mechanical seals are arduous, experiencing seal chamber pressures continuously above 1000 PSIG at sub-zero temperatures. The pumps operate at shaft speeds above 5,000 RPM providing additional challenges for the mechanical seal to overcome. The heritage mechanical seals utilized in this application were a dual unpressurized configuration supported by an API Piping Plan 11 and 52. Through close collaboration with the end user, the supplied seal provided by the manufacturer was able to achieve an 18 â 24 Mean Time Between Repair (MTBR). Known failure modes of the existing mechanical seal identified during failure analysis activities were addressed through modification of the seal to the existing iteration. The most recent limiting factor in seal performance was attributed to breakdown of the dynamic secondary sealing element in both the process and containment seals. The dynamic secondary seal, or o-ring, experienced a high degree of abrasion and breakdown due to suspected axial movement of the pump rotor. Additional analysis of the pump further supported these findings. It was the seal manufacturerâs recommendation to address the root cause of seal failures by proposing an alternative configuration. The alternative seal configuration utilized active seal face features for optimized sealing of the ethylene while incorporating a non-pusher secondary seal (NPSS) to both the process and containment seals to address the dynamic o-ring concerns. Additionally, improvements to the circulation and cooling of the Plan 52 loop were identified and optimized through CFD modeling of the internal circulation device and support system piping. All modifications were incorporated into a redesigned seal cartridge that was installed during a unit outage in September 2021. Performance of the new design to date has been extremely satisfactory despite several documented upsets in the process stream.
Presenter(s)
Once the content has been viewed and you have attested to it, you will be able to download and print a certificate for PDH credits.
If you have already viewed this content,
please click here
to login.
Language
Pricing
Individuals
AIChE Member Credits | 0.5 |
AIChE Pro Members | $19.00 |
Fuels and Petrochemicals Division Members | Free |
AIChE Graduate Student Members | Free |
AIChE Undergraduate Student Members | Free |
AIChE Explorer Members | $29.00 |
Non-Members | $29.00 |