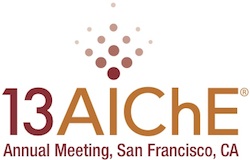
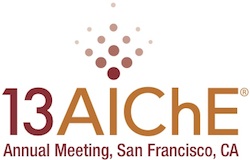
Mixture preparation prior to a reforming catalyst is one of the important challenges in developing reliable hydrocarbon reformers. Reactants should be mixed properly before supplying it to the downstream catalyst, and unwanted gas-phase reactions in the mixing region should be suppressed at the same time. Ethylene, a well-known deposit precursor, is one of the major products from gas-phase reactions, which can cause deleterious catalyst failure even with a small amount as ~ 1,000 ppm1. Therefore, it is essential to characterize ethylene generation from gas-phase reactions before designing the mixing chamber of a hydrocarbon reformer. Previous works2-5 showed that gas-phase reactions are closely related to mass and heat transfer; thus, the coupled transport-kinetics was developed to describe the gas-phase reactions in the mixing region of a hydrocarbon reformer6.
The mixing chamber design described previously6 was used for the CFD calculations. A mixture of fuel/steam vapor and air are supplied separately and mixed before entering a downstream reforming catalyst. The initial autothermal reforming (ATR) conditions had an O/C ratio of 1.6 and a S/C ratio of 1.5. The flow rates of reactants were calculated with the assumption that the reformer is designed for a 5kWe-class system.
N-heptane was selected as a surrogate liquid fuel. was reduced in size because As illustrated in Figure 1, a reduced mechanism consisting of 50 species and 98 reactions was found to be reasonably consistent with the predictions of the original mechanism. This figure shows the decrease in reactivity as the temperature increases from 450 to 550 oC. This region of decreasing reactivity with increasing temperature is known as the Negative Temperature Coefficient (NTC) region. The reasons for this unusual behavior are discussed in previous work10. Applying the reduced reaction kinetics, tC or above 625 o
Figure 1 Product distribution of n-heptane oxidation modeling results under the nominal ATR condition (O/C=1.6, S/C=1.5): solid line (LLNL mechanism) and dashed line (a reduced mechanism)
Figure 2 Predicted distributions of ethylene concentration on the cross section shown in (a) at inlet temperature of (b) 450 oC and (c) 625 oC
At lower temperature (450 oC), the local O/C ratio (~1.9) is higher than the overall O/C ratio (1.6) at the location of maximum ethylene production. Therefore, the more oxidizing environment promotes ethylene production. Figure 3 describes the results of the perfectly mixed kinetic study using the reduced mechanism. The rate of ethylene production increases as O/C increases. In this temperature range, most of the ethylene is produced by the reaction C2H5+O2 = C2H4+HO2.
Figure 3 Perfectly-mixed predictions of the reaction rate profiles for ethylene production at the inlet temperature of 450 o<span °íµñ;="°íµñ;" color:black;font-weight:normal;mso-bidi-font-weight:bold'="color:black;font-weight:normal;mso-bidi-font-weight:bold'">C (S/C=1.5)
At higher temperature (625 oC), the rate of ethylene generation and the temperature change are much lower compared to the lower inlet temperature case. The rate of ethylene generation peaks at two points (before and after the nozzle). The results showed that the heat release rate is moderate but coincident with the ethylene generation rate. Figure 4 describes the results of perfectly mixed kinetic calculations also using the reduced mechanism. The effect of O/C is opposite to that predicted at the lower temperature. At the higher temperature, pyrolysis chemistry is dominant, so that the rate of ethylene production decreases as O/C increases. In this temperature range, high-temperature chemistry is activated and alkyl radical decompositions begin to contribute to ethylene production by the following reactions: n-C3H7 = CH3+C2H4 and n-C4H9 = C2H5+C2H4. Ethylene production peaks in two locations in the coupled transport-kinetics analysis. At the peak upstream of the nozzle, the local reactant composition is O/C = 0.7. The more pyrolytic environment stimulates the ethylene production; thus the finitely mixed case (266 ppm) showed more ethylene production than the perfectly mixed case (114 ppm).
Figure 4 Perfectly-mixed predictions of the reaction rate profiles for ethylene production at the inlet temperature of 625 o<span °íµñ;color:black;font-weight:normal;mso-bidi-font-weight:bold'="°íµñ;color:black;font-weight:normal;mso-bidi-font-weight:bold'">C (S/C=1.5)
The coupled transport-kinetics analysis was performed to investigate the characteristics of ethylene production in the mixing region of a hydrocarbon reformer. At lower temperature, most of ethylene is produced by oxygen addition; thus, ethylene production is stimulated with efficient mixing of fuel/steam vapor stream with the air stream. On the other hand, pyrolysis chemistry dominates ethylene production near 625 oC, and ethylene generation can be suppressed by better mixing. The results suggest that the complexities of the gas-phase kinetics demand that careful attention be paid to design of the mixing region upstream of an ATR reformer to avoid undesirable gas-phase reactions that have the potential to interfere with proper catalytic operation.
References
1. Kang IY, Carstensen HH, Dean AM. Impact of gas-phase reactions in the mixing region upstream of a diesel fuel autothermal reformer. Journal of Power Sources. Feb 2011;196(4):2020-2026.
2. Yoon S, Kang I, Bae J. Suppression of ethylene-induced carbon deposition in diesel autothermal reforming. Int. J. Hydrog. Energy. Feb 2009;34(4):1844-1851.
3. Lindstrom B, Karlsson JAJ, Ekdunge P, et al. Diesel fuel reformer for automotive fuel cell applications. Int. J. Hydrog. Energy. May 2009;34(8):3367-3381.
4. Porš Z, Pasel J, Tschauder A, Dahl R, Peters R, Stolten D. Optimised Mixture Formation for Diesel Fuel Processing. Fuel Cells. 2008;8(2):129-137.
5. An SM, Kim WS, Lee SY. Spraying of liquid fuel for improvement of reforming performance for hydrogen generation. Int. J. Hydrog. Energy. 2011;36(9):5342-5349.
6. Kim S, Zhu H, Carstensen HH, Kee R, Dean AM, Bae J. Coupled kinetics and transport in the mixing region of a hydrocarbon reformer. AIChE. Salt Lake City, UT2010:280.
7. Mehl M, Pitz WJ, Sjöberg M, Dec JE. Detailed kinetic modeling of low-temperature heat release for PRF fuels in an HCCI engine. SAE 2009 International Powertrains, Fuels and Lubricants Meeting. Florence, Italy2009.
8. Mehl M, Pitz WJ, Westbrook CK, Curran HJ. Kinetic modeling of gasoline surrogate components and mixtures under engine conditions. Proceedings of the Combustion Institute. 2011;33(1):193-200.
9. Curran HJ, Gaffuri P, Pitz WJ, Westbrook CK. A comprehensive modeling study of n-heptane oxidation. Combustion and Flame. Jul 1998;114(1-2):149-177.
10. Kim S, Carstensen H-H, Dean AM, Bae J. Investigation of gas-phase reactions in the mixing region for hydrocarbon autothermal reforming applications. Int. J. Hydrog. Energy. 2012;37(9):7545-7553.