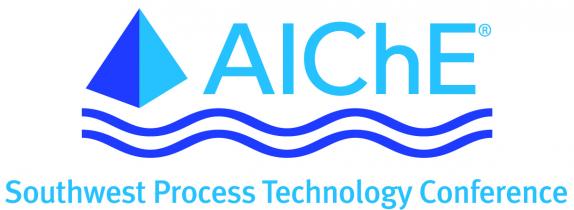
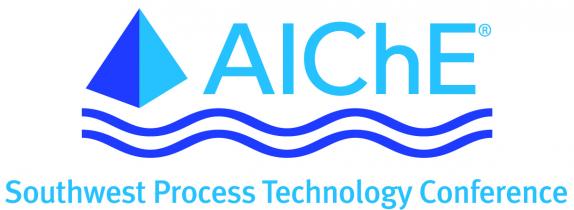
Automated unheading valves are becoming the norm for both new and modernized delayed cokers, as these unheading devices have a proven track record of improving safety, operability, and reliability of the delayed coker.
But the installation of automated valves has created new challenges in the design of coke drum piping and the coke drum itself. Historically, with manual coke drum unheading, the coke drum feed was inject directly into the bottom head of the coke drum and the feed naturally flowed upwards with a relatively even distribution.
The use of bottoms, automated unheading devices requires the flow be injected into the side of the coke drum cone, an operation which has caused coke drum distortion in cases and maldistribution of the feed in some instances.
This paper presents engineering analysis and proven operating designs, showing that improved technology will assure even upward distribution of coker feed; the improved design must aims the feed upward and toward the center of the coke drum.
Successful coker feed injection can result in reliability and stream factors improvements which flow to the refiners bottom line. Technologies considered must include flow analysis, dual side entry nozzles, nozzle orientation, retractable center feed injection devices, and pipe design.