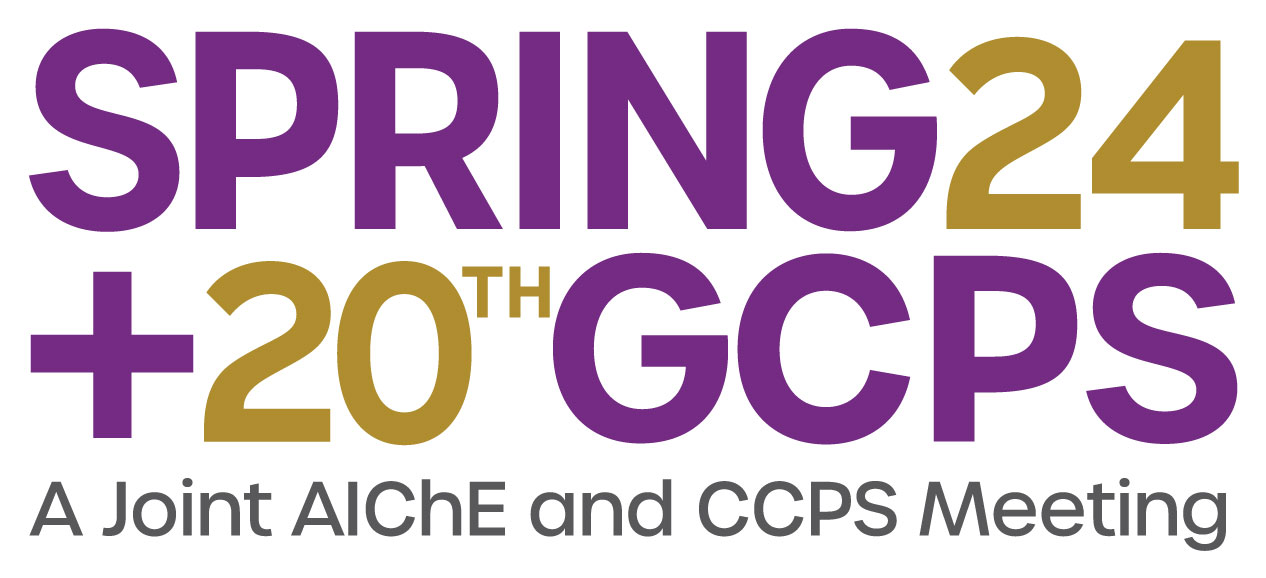
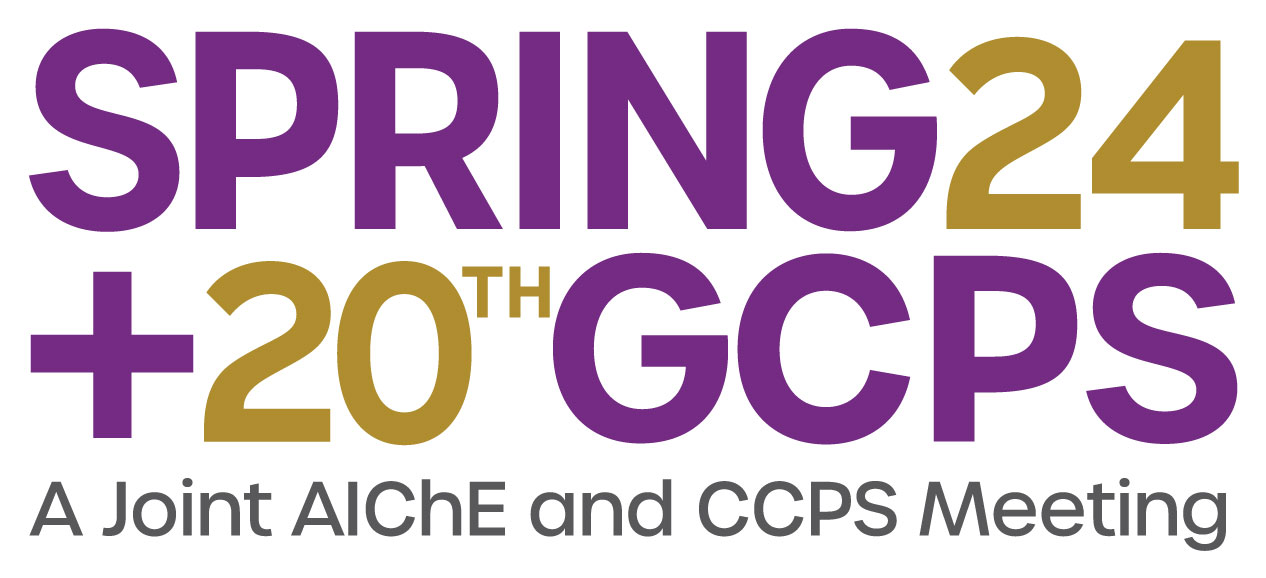
Objectives/Scope: The global petrochemical market demand for ethylene is growing steadily. While operators are striving to maintain maximum throughput, expand margins, and decarbonize their operations, equipment fouling and unplanned maintenance is constantly pushing plants in the opposite direction. With plants extending the time between turnarounds, these avoidable situations are hurting the ethylene industry's bottom-line more than in the past.
Methods, Procedures, Process: Most ethylene plants have limited capabilities in predicting charge gas compressor failures resulting from either fouling or mechanical issues. This jeopardizes the reliability of the compressor operation. The purpose of this paper is to provide a case study demonstrating that fouling and unplanned outages involving the cracked gas compressor can be significantly reduced. Baker Hughes developed its next level real time monitoring program by combining its digital assets for remote diagnostics (iCenter) with effective chemical treatment programs to improve compressor performance and minimize the total costs over the 5-10 year run cycle. By using proprietary Baker Hughes monitoring technology, current plant instrumentation, real time plant data, machine efficiency, and key mechanical parameters, the cracked gas compressor can be constantly monitored by experts. This new approach can more accurately predict the real time demand for antifoulant chemistries and provide predictive mechanical failure information. The ability to predict mechanical failures provides the plant with the lead time needed to properly prepare for an unscheduled outage.
Results, Observations, Conclusions: The result is plant availability and efficiency improvement leading to economic gains and carbon footprint reductions. The presented case study demonstrates that on a 1.2 MTA ethylene plant, the fouling associated cost over typical mean time between maintenance (6 years) can be halved (from approx. 60M$ to 30M$) with potential CO2 emission reduction of 50,000 tons. The amount of savings generated by avoiding an unplanned outage due to a mechanical failure would vary depending on specific outage situation and duration.
Presenter(s)
Language
Pricing
Individuals
AIChE Member Credits | 0.5 |
AIChE Pro Members | $19.00 |
Fuels and Petrochemicals Division Members | Free |
AIChE Graduate Student Members | Free |
AIChE Undergraduate Student Members | Free |
AIChE Explorer Members | $29.00 |
Non-Members | $29.00 |