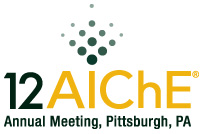
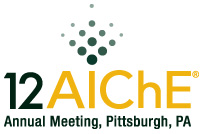
Component Development for decentralized sustainable hydrogen production
Stephan Nestl, Manfred Wegleiter, Viktor Hacker
Institute of Chemical Engineering and Environmental Technologies, Graz University of Technology
8010 Graz, Steyrergasse 21/2, Austria
stephan.nest@tugraz.at, manfred.wegleiter@tugraz.at, viktor.hacker@tugraz.at
Fuel cells have the potential to realise high efficient and emission-free power generation. Fuel cells have been extensively investigated and various manufacturers start mass production in the next few years. The resulting cost reduction will make the fuel cell to a competitive product in various fields of applications, such as electro-mobility, APUs or residential heat and power generation.
Due to the fact that hydrogen transport and storage capacities are still inadequate, on site hydrogen production offers an alternative to the centralised production that is common today. Besides electrolysis, the reformation of liquid and gaseous energy sources, as for example methane, or ethanol, in small units located near the end user, can play an important role as an enabling technology for fuel cells. Thereby hydrogen production from renewable energy sources also decreases the carbon dioxide emissions. To achieve these goals small scale reformers have to overcome the economic hurdle to market entry.
The selection of an economically advantageous catalyst system with high durability and satisfying conversion efficiency can be seen as one of the most important steps for that. Various catalytic active materials can be found in literature. On the one hand noble metals such as Ruthenium or Platinum show higher stability against some degradation effects, on the other hand their prices are several orders of magnitude higher compared to other usable metals like Nickel or Cobalt.
In addition to the catalytic active materials also the selection of the support structure is an important aspect. Commonly used catalyst pellets are simple to handle and inexpensive in production. The pellets can also be exchanged easily which increases operation time and lowers maintenance costs. But the catalytic active surface of pellets is limited and a homogeneous gas flow is difficult to achieve. More complex structures such as ceramic monoliths and metallic foams have the potential for improved performance. With regard to temperature control and waste heat utilization also the use of catalytic heat exchanging materials is investigated.
Catalyst lifetime has a significant impact on economic efficiency and depends strongly on the reaction conditions. Temperature, steam or oxygen to carbon ratio and space velocity needs to be optimised for each potential fuel. The operating conditions and the catalyst material determine the amount of by-products and carbon monoxide in the product gas, which in turn determines the necessary further purification steps. Advantages and disadvantages of different system configurations for decentralized hydrogen production units will be discussed in the presentation.
Acknowledgment: This work is funded by the Research Studios Austria program of the Austrian Federal Ministry of Economy, Family and Youth.