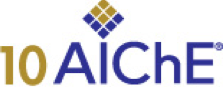
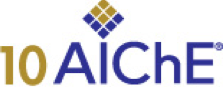
Of prime importance in the ethylene plant process is the Cracked Gas (CG) Dehydration System. CG Dryer operation is a key factor to the achievement of not only on-specification ethylene production, but the prevention of incapacitating hydrates formation in the downstream recovery equipment operating at low-temperatures. In an existing steam cracker, there is usually the requirement to handle progressive creep in the olefins plant's CG capacity. Therefore, there will be a time when the increase in CG capacity requirements will deem a debottlenecking of the appropriate operating systems. However, for the economic success of any Debottlenecking Project it will be important to achieve the increase in capacity with the lowest capital expenditure, while maintaining a reliable operation.
In the debottlenecking of any ethylene plant the process performance of the CG Dryer Systems will be crucial to a successful project. Given the basic economic goals – achieve the desired incremental capacity increase with the lowest capital cost and minimal plant downtime and construction effort – the objective of this paper is to present basic concepts that can be applied in economic debottlenecking of a CG Dryer System, eliminating the bottleneck to capacity and, in many cases, improving operating efficiency and reliability as well.
This paper provides an introduction to modification concepts that, depending upon the existing configuration of the CG Dryer equipment, might be successfully utilized to debottleneck a CG Dryer System. In addition, this paper will highlight those ancillary elements and other considerations that are essential to the successful operation of the revamped CG Dryers and must not be overlooked.