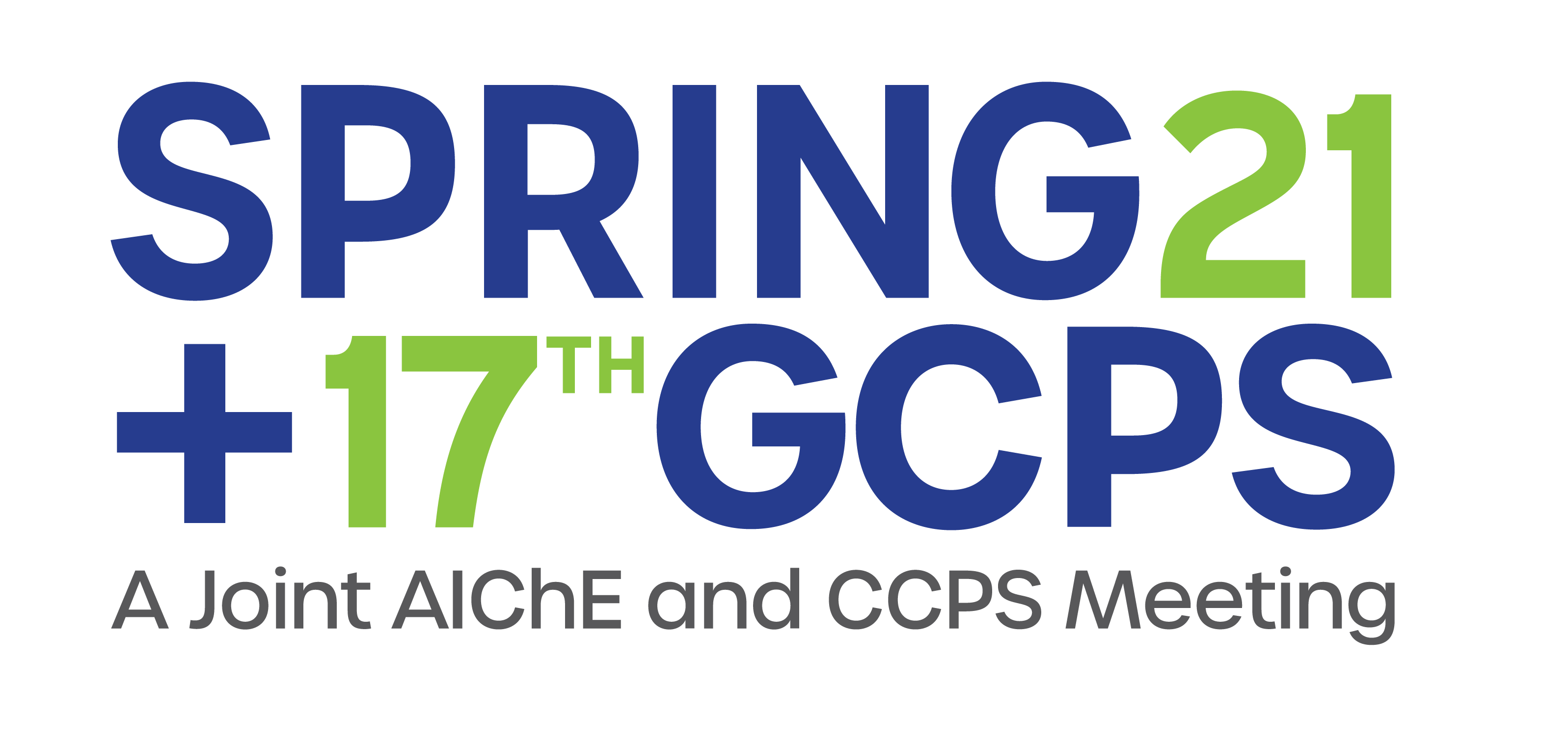
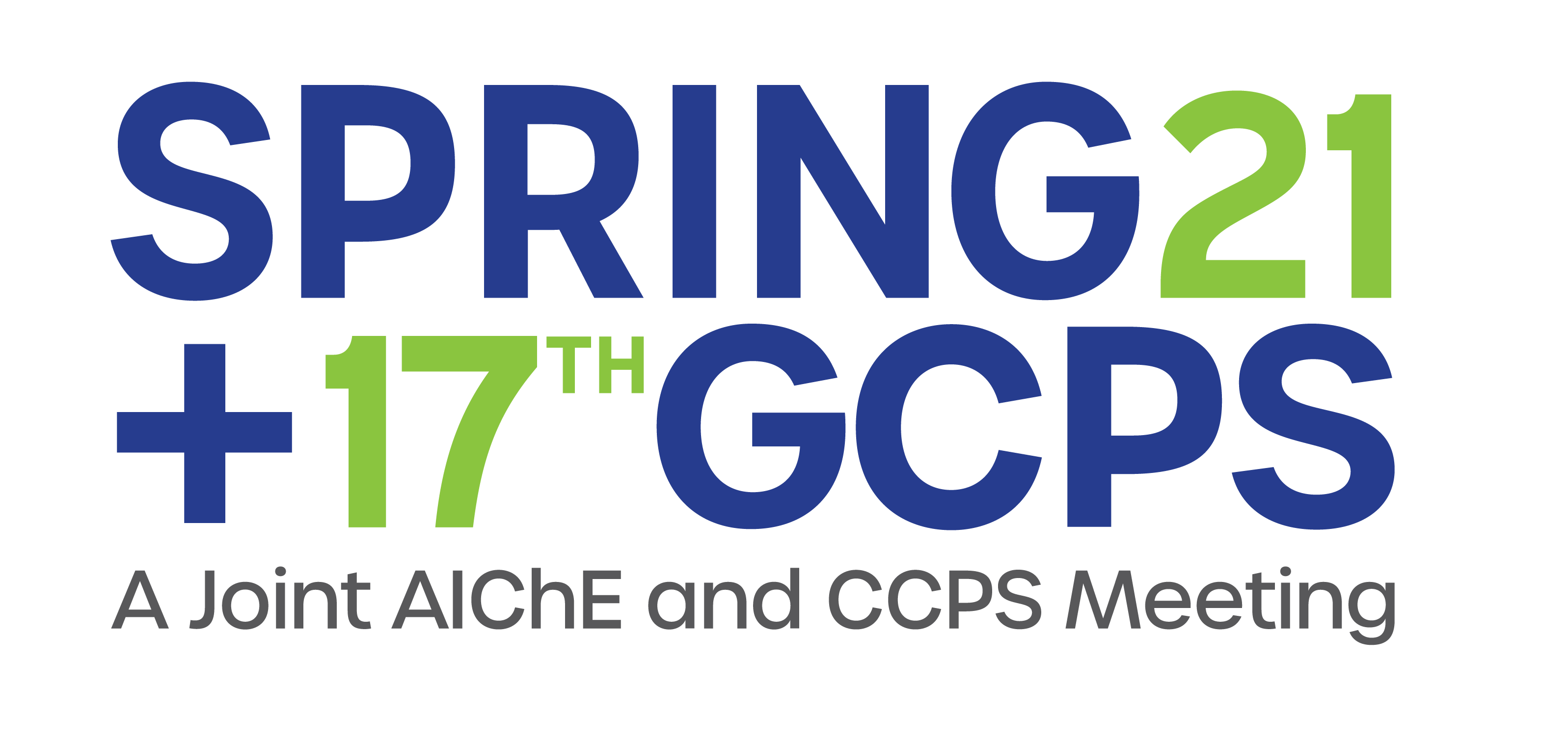
During the manufacture of a new product, a batch distillation step required considerably longer time than original anticipated, and it became a bottleneck for production. The distillation step was used to remove organic solvents from the target product in a column equipped with structured packing and a reflux condenser. A dynamic simulation model was used to represent a typical batch at the original operation conditions. The simulation results were then used to perform capacity rating calculations for the column and the condenser at different times during the patch. These calculations indicated that flooding in the tubes of the condenser was the key limiting factor. To overcome this limitation, the condenser configuration was changed, moving away from the reflux mode, that is, with vapor and condensate flowing in the same direction inside the tubes. After this change in configuration, the throughput limitation in the unit was removed, and a distillation time lower than 1/3 of the original time was consistently demonstrated in the plant. In addition, a higher distillate purity was achieved.
Presenter(s)
Once the content has been viewed and you have attested to it, you will be able to download and print a certificate for PDH credits.
If you have already viewed this content,
please click here
to login.