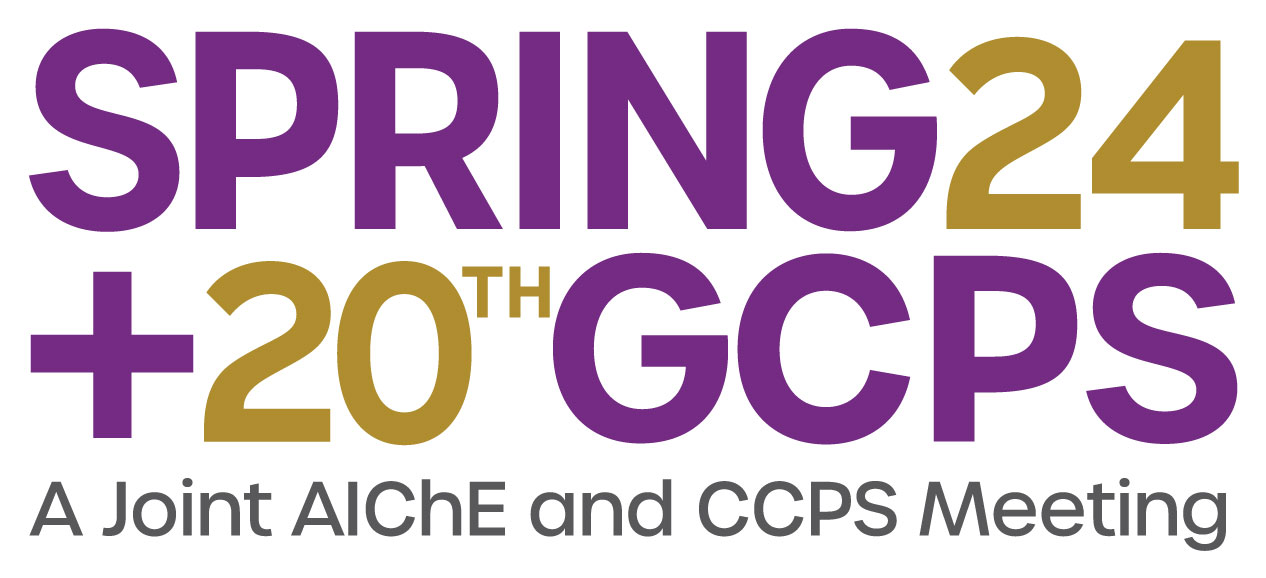
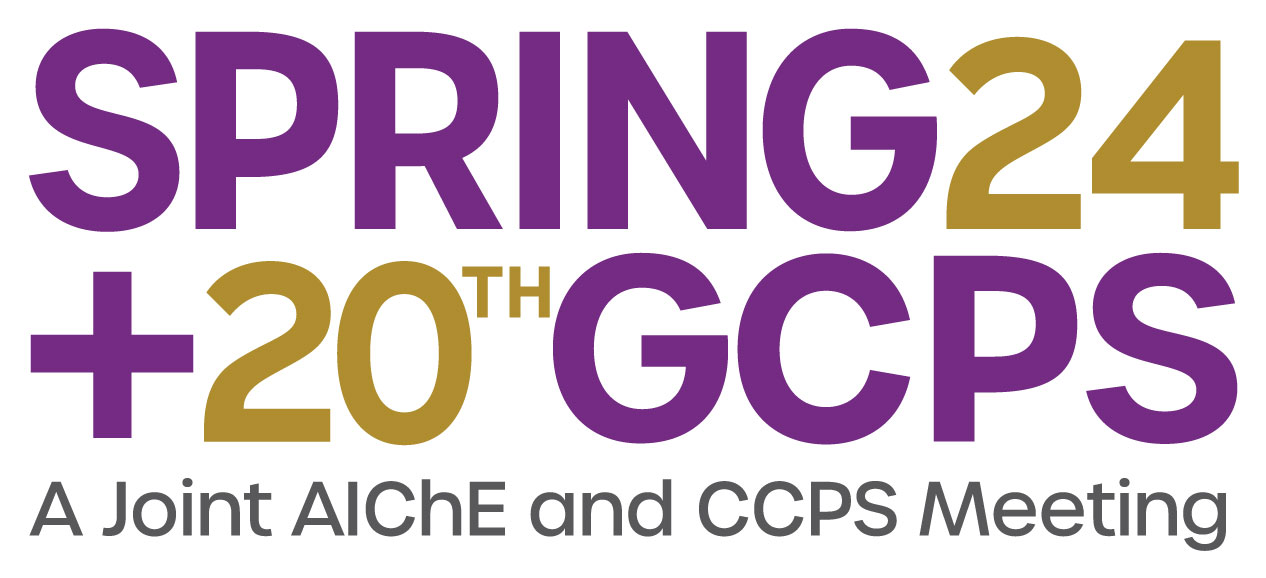
Super-dry reforming of methane (1) has been developed at the Laboratory for Chemical Technology (LCT) at Ghent University as a sustainable chemical process complimentary to the well-established steam reforming (equations 1 and 2) and dry reforming (equation 3) process. Indeed, whereas steam reforming focuses on the production of pure H2 or syngas with high H2:CO ratio (3:1), and dry reforming on the production of syngas with low H2:CO ratio (1:1), super-dry reforming (equation 4) maximizes the CO yield at the cost of H2. The development of an effective CO2-to-CO conversion techniques provides a path towards the creation of new chemical value chains based on CO as a platform molecule, such as the value chain towards ethanol and ethylene through gas fermentation and dehydration (2). To achieve its selectivity towards CO, the super-dry reforming process makes use of a two-step process to avoid the water-gas shift reaction by performing the CO production step in absence of H2O by using a CO2 sorbent such as CaO and a redox active material such as Fe3O4. Although the former is more endothermic than dry reforming, the amount of reaction heat required per mole of CO2 utilized is significantly lower (110 vs. 247 kJ per mole CO2).
CH4 + 2H2O = 4H2 + CO2 | ÎH°(298K) = 165 kJ mol-1 CH4 |
(1) |
CH4 + H2O = 3H2 + CO | ÎH°(298K) = 206 kJ mol-1 CH4 |
(2) |
CH4 + CO2 = 2H2 + 2CO | ÎH°(298K) = 247 kJ mol-1 CH4 |
(3) |
CH4 + 3CO2 = 4CO + 2H2O | ÎH°(298K) = 330 kJ mol-1 CH4 |
(4) |
The super-dry reforming process has been shown to possess economic potential for the valorization of biogas and biomethane (3), but also for steel mill gases such as the blast furnace gas (4, 5), demonstrating the flexibility of the chemical looping approach towards resource valorization (6). By using a third metal oxide such as Mn3O4 or NiO, Singh et al. showed that the super-dry reforming process could be run in an autothermal way by introducing a chemical looping combustion functionality within the two-step process (5). Applying the chemical looping combustion cycle in situ of the super-dry reforming process to provide the heat of reaction, particularly for the CO2 release during decarbonation of CaCO3, requires a relatively pure source of oxygen to avoid dilution of the product stream. An interesting way around this has been proposed in which chemical looping combustion, calcium looping and chemical looping air separation are combined in an energy-neutral chemical looping process for the capture and release of CO2 from steel mill gases (7).
The transient nature of chemical looping processes and the use of functional materials pose specific requirements towards the infrastructure required for technology upscaling. Through funding by the Flemish Moonshot Program, the LCT had the opportunity to design and build a chemical looping pilot plant with a nominal capacity to convert 1 kg CO2 per hour into CO through super-dry reforming. The pilot plant, which consists of two parallel fixed bed reactors, has been commissioned under non-reactive conditions, with the first experimental campaigns underway. In the meantime, CaO/Al2O3 and Fe2O3/MgAl2O4 materials have been upscaled from gram to kilogram scale.
<Figure 1. Chemical looping pilot plant for super-dry reforming installed at the LCT.>
In conclusion, the development of the super-dry reforming process has come a significant way since its conception and is on the verge of being experimentally tested at TRL 5. Non-reactive pilot plant tests indicate that the plant has the right functionality to deal with the transient behavior of chemical looping processes when operated in multiple fixed bed reactors and to provide high quality experimental data. Given the endothermicity of super-dry reforming and CO2 utilization in general, the development of strategies for heat management and autothermal operation is a crucial piece of the technological puzzle. To this end, experimental pilot plant campaigns will provide answers and directions for further upscaling.
References:
- Buelens LC, Galvita VV, Poelman H, Detavernier C, Marin GB. Super-dry reforming of methane intensifies CO2 utilization via Le Chatelier's principle. Science. 2016;354(6311):449-52.
- Van Cauwelaert M, Delikonstantis E, Buelens L, Poelman H, Van Geem KM, Galvita V. From steel to ethylene : super-dry reforming of CH4. 34th Ethylene Producersâ Conference; San Antonio, USA 2022.
- Verbeeck K, Buelens LC, Galvita VV, Marin GB, Van Geem KM, Rabaey K. Upgrading the value of anaerobic digestion via chemical production from grid injected biomethane. Energy & Environmental Science. 2018;11(7):1788-802.
- Singh V, Buelens LC, Poelman H, Saeys M, Marin GB, Galvita VV. Carbon monoxide production using a steel mill gas in a combined chemical looping process. Journal of Energy Chemistry. 2022;68:811-25.
- Singh V, Buelens LC, Poelman H, Saeys M, Marin GB, Galvita VV. Upcycling the carbon emissions from the steel industry into chemicals using three metal oxide loops. Energy Advances. 2022;1(6):367-84.
- Singh V, Buelens LC, Poelman H, Marin GB, Galvita VV. Chemical looping: a technology platform for upcycling low-grade industrial resources. Discover Chemical Engineering. 2023;3(1):12.
- Singh V, Buelens LC, Poelman H, Saeys M, Marin GB, Galvita VV. Decarbonisation of steel mill gases in an energy-neutral chemical looping process. Energy Conversion and Management. 2022;254:115248.
Presenter(s)
Language
Pricing
Individuals
AIChE Member Credits | 0.5 |
AIChE Pro Members | $19.00 |
Fuels and Petrochemicals Division Members | Free |
AIChE Graduate Student Members | Free |
AIChE Undergraduate Student Members | Free |
AIChE Explorer Members | $29.00 |
Non-Members | $29.00 |