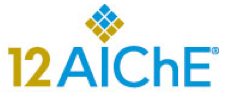
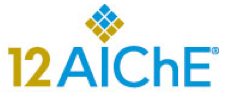
The chilling train system is an important part of ethylene plant which is usually combined with demethanizer and a series of flash drums to separate hydrogen and methane from cracked gas, and recover the hydrogen and methane as different products through multi-stream heat transfer with refrigerants. The system of demethanizer and chilling train is the intermediate part of an ethylene plant whose performance can significantly affect the amount of flaring during start-up and thus energy consumption. However, most research efforts are focused on design and steady-state optimization aspects, the dynamic behavior of chilling train is rarely explored. In this study, several control strategies of demethanizer and chilling train system will be simulated and corresponding dynamic responses will be investigated in order to reduce time and flaring during start-up.
General methodology includes the following steps: 1) In the first place, a steady-state model will be built using the sequential modular approach and plant design data; 2) the model will be further validated with normal steady state operating conditions obtained from the DCS (distributed control system) historian; 3) If the steady-state model is satisfied, it will be exported to the dynamic simulation environment. Three types of data will be needed in this transferring, including equipment dimensions, control strategies and P&ID (piping and instrument diagram) parameters, and the heat transfer option; 4) after the dynamic modeling is completed, it will be further validated to match some process upsets in DCS historian; 5) the control strategies will be tested in dynamic simulation to decrease start-up time and energy consumption. A case study is used for the demonstration.
Presenter(s)
Language
Pricing
Individuals
AIChE Member Credits | 0.5 |
AIChE Pro Members | $15.00 |
Fuels and Petrochemicals Division Members | Free |
AIChE Graduate Student Members | Free |
AIChE Undergraduate Student Members | Free |
AIChE Explorer Members | $25.00 |
Non-Members | $25.00 |