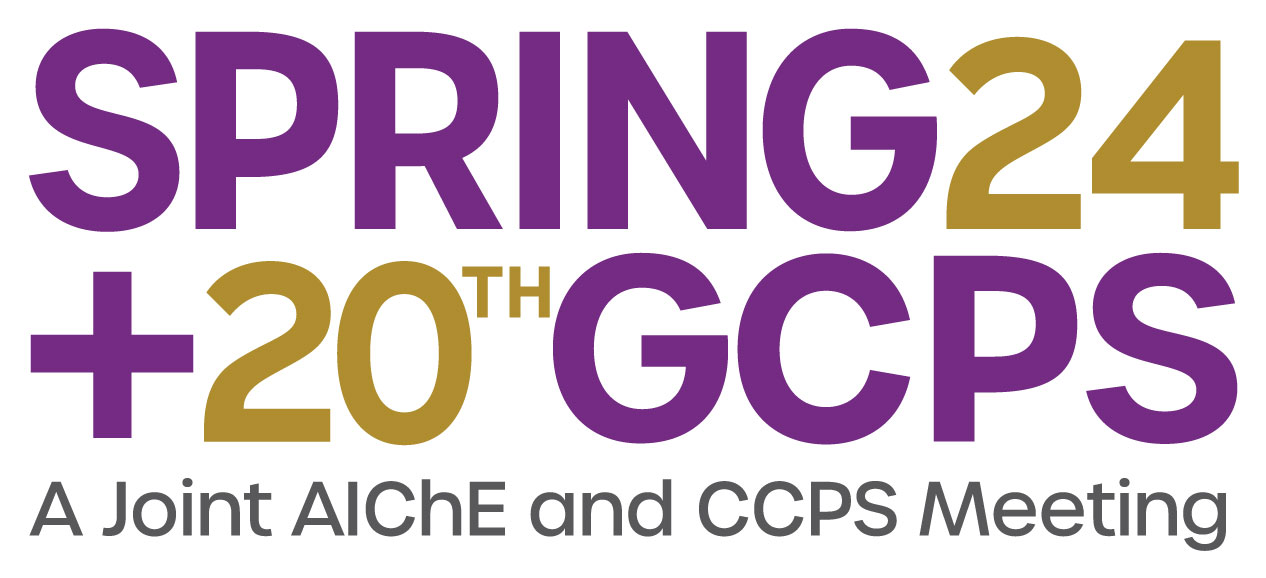
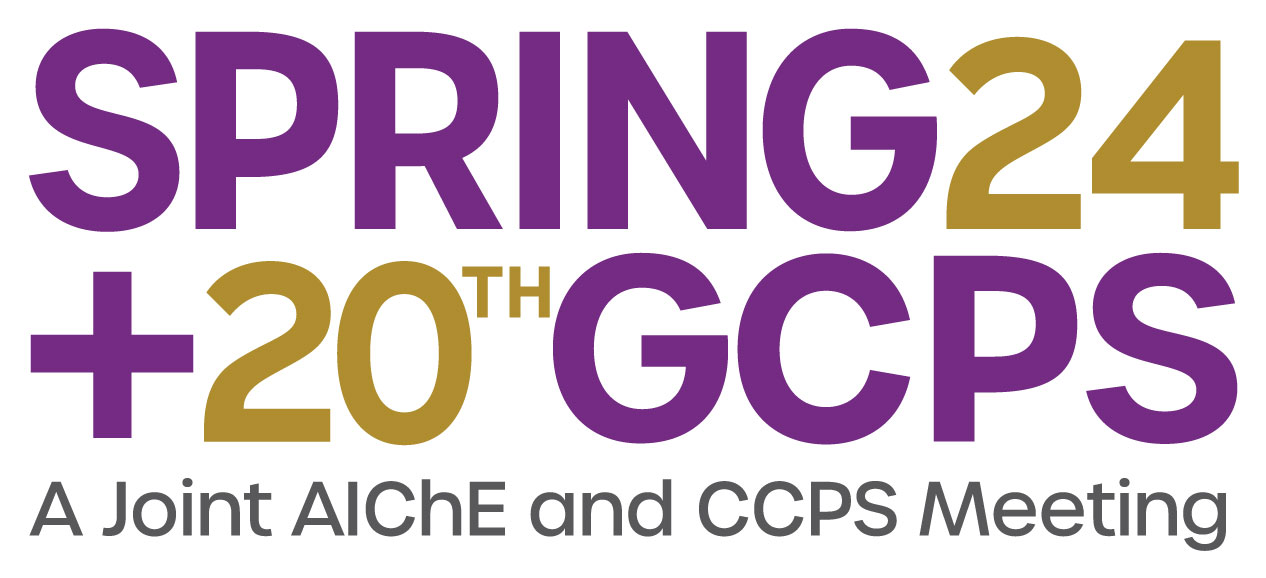
- Abstract
LNG is becoming increasingly viable and popular as a marine fuel because it is clean-burning, produces fewer NOX emissions, and has the lowest emissions level per joule of energy released of all fossil fuels.
The use of LNG on board is attractive because it complies with strict emission rules set out by the International Maritime Organization (IMO). Fuel gas supply system (FGSS) for LNG fueled ships is a fuel gas handling system, and LNG fuel is delivered to the engine and boiler system for propulsion and power generation of vessels.
This paper shows application of dynamic simulation to analyze and predict the LNG tank process behaviors (pressure, temperature and LNG aging) for LNG fueled ship, using a digital twin (CHEMCAD simulator) with cloud hosting, and verifying the behavior of controllability of fuel gas supply pressure from FGSS to engine system, and the interactions of BOG compressor control and LNG pump control etc. The dynamic simulation is executed in real time, and the results of calculation are transferred to LNG fueled ship through Sea-Navi® system.
- Overview of LNG fuel gas system for LNG fueled ship
LNG is the cleanest fossil fuel currently on the market. Vessels with a FGSS meet international measures and regulations to reduce emissions and contribute to a cleaner environment for future generations.
The main components of the FGSS are as follows:
- LNG bunker skid
- Cryogenic type C tank
- LNG pump (LNGP)
- BOG compressor (BOGC)
- LNG vaporizer & LNG gas heater for LNGP line
- Pre-heater & After-cooler for BOGC line
- Buffer tanks
- Process control system
The simplified process flow diagram for FGSS is shown in Fig.2.1.
|
As shown in Fig.2.1, the fuel gas flow rate to the main engine is based on BOGC pressure control and LNGP pressure control.
Herein, we focus on the dynamic process study for LNG fuel tank behavior according to fuel gas flow and pressure to fuel gas consumers supplied by BOGC and LNGP.
The controllability of LNG fuel tank pressure is studied, based on the points of view of the operating period of both controls, the change of operating points. Then, the related optimum control parameters are calculated through the dynamic simulations at the same time.
|
Fig.2.2 shows the system architecture of the data communication between LNG fueled ship and AWS. The system conducts the online dynamic simulation using digital twin in AWS cloud system.
Presenter(s)
Language
Pricing
Individuals
AIChE Member Credits | 0.5 |
AIChE Pro Members | $19.00 |
Fuels and Petrochemicals Division Members | Free |
AIChE Graduate Student Members | Free |
AIChE Undergraduate Student Members | Free |
AIChE Explorer Members | $29.00 |
Non-Members | $29.00 |