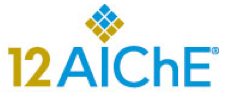
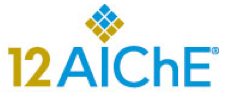
Corrosion under insulation (CUI) of carbon and low alloy steels is one of many failure mechanisms that decrease reliability and equipment life while increasing the cost of ownership. Carbon and low alloy steels are most susceptible to CUI when operated in or cycled through temperatures ranging from 10°F (–12°C) to 350°F (175°C). Because CUI is “hidden”, the inspection costs to locate this failure mechanism are high when compared to external corrosion of non-insulated piping and equipment. The key to managing CUI is to break the CUI cycle by applying surface coatings that protect the substrate from water and oxygen, the catalyst of corrosion.
Traditional surface coatings such as epoxies and acrylics have a service life of 5-8 yrs before the bond begins to breakdown and corrosion begins. Surface imperfections during the initial application of traditional coatings and/or damage of the coating during installation of the insulation result in an immediate location for CUI to begin. Reduction of CUI requires a surface coating that has a service life of > 20 years and is tolerant to surface imperfections.
This paper will focus on Thermal Spray Aluminum (TSA). TSA is a surface coating that has been proven to have a long service life and is tolerant to surface imperfections due to its anodic properties.
Presenter(s)
Once the content has been viewed and you have attested to it, you will be able to download and print a certificate for PDH credits.
If you have already viewed this content,
please click here
to login.