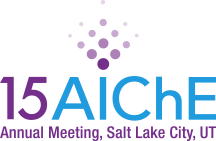
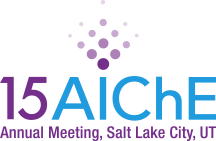
Evaluation of Static or Dynamic Curing Process for Improved Controlled Release, Dry Powder Coatings of Ethylcellulose using a Rotor Coater
Shawn Engels?, Cody Schoener ?, Uma Shrestha ?, Kody Bellach?, and Brian Jensen?
?Freund-Vector Corporation, Marion, IA 52302, USA
?The Dow Chemical Company, Midland, MI 48674 USA
Purpose: To assess how different curing conditions influence controlled drug release from ethylcellulose, high productivity coatings using a rotor process technology. The rotor process technology enables the user to achieve high levels of weight gain in a short period of time while still demonstrating sustained drug release with micronized ethylcellulose. For this work, static and dynamic curing was assessed at different temperatures and lengths of time to improve film coalescence to provide more stable dosage forms. Static curing was completed in an oven while dynamic curing was completed in the rotor coater. Optimized curing conditions and times will enable formulators to achieve the most robust product.
Methods: Acetominophen (APAP) was dry powder coated onto sugar spheres (#20 ? 25; Colorcon Inc., USA) using polyvinyl pyrrolidone (K2932, ISP Inc., USA) as binder on a Granurex GXR-35 rotor process (Freund-Vector Corp., USA). A drug to binder ratio of 97:3 w/w was maintained. Experimental ethylcellulose samples (The Dow Chemical Company, USA) were dry powder coated onto the APAP beads with triethyl citrate (TEC) as a plasticizer using the same rotor process as above. An ethylcellulose to TEC ratio of 3:1 w/w was maintained throughout the coating. Once the APAP sugar spheres were coated to 20% weight gain of ethylcellulose, samples were either removed and static cured or kept in the rotor coater and cured. For static curing, samples were placed on trays and placed inside an oven for 2 hours at 60ºC. For dynamic curing, samples continued to rotate at 250 rpm while forced, hot air was applied from above at 40 or 60ºC between 15 and 60 minutes. Dissolution and SEM were evaluated for curing influence on drug release. USP Apparatus I (baskets) was utilized for in-vitro dissolution studies and drug release data was compared using similarity factor ( analysis.
Results: Initial experiments demonstrate that dynamic curing provided more controlled drug release compared to static curing (Figure 1A). Dynamic curing for at 40ºC for 15 minutes was significantly slower (by analysis) in drug release compared to static curing at 60ºC for 2 hours. This indicated the combination of the force hot air plus the frictional movement caused by the rotor bed movement enables improved film coalescence versus a static tray of sample placed in the oven. Dynamic curing at 40ºC for 15 minutes versus dynamic curing at 60ºC for 60 minutes was similar based on
analysis indicating a short cure time of at least 15 minutes might provide full film coalescence and a stable coating. Further curing assessment on drug release will be presented on samples which were placed on stability for 1, 3, and 6 months in storage conditions of either 30ºC and 65% relative humidity or 40ºC and 75% relative humidity.
Figure 1. (A) Influence of static vs dynamic curing on APAP drug release and (B) cross-sectional view of rotor coater. Hot air is forced upon the product bed from above (large arrow at top).
Conclusion: Using the rotor process and force hot air, formulators can achieve sustained release and fully coalesced films by dynamically curing. Dynamic curing as short as 15 minutes at 40ºC can significantly reduce curing times compared to static curing. The combination of dynamic curing and dry powder coating using the rotor process and micronized ethylcellulose also provides high productivity opportunities for pharmaceutical companies when compared to traditional organic or aqueous based ethylcellulose wurster spray coatings.