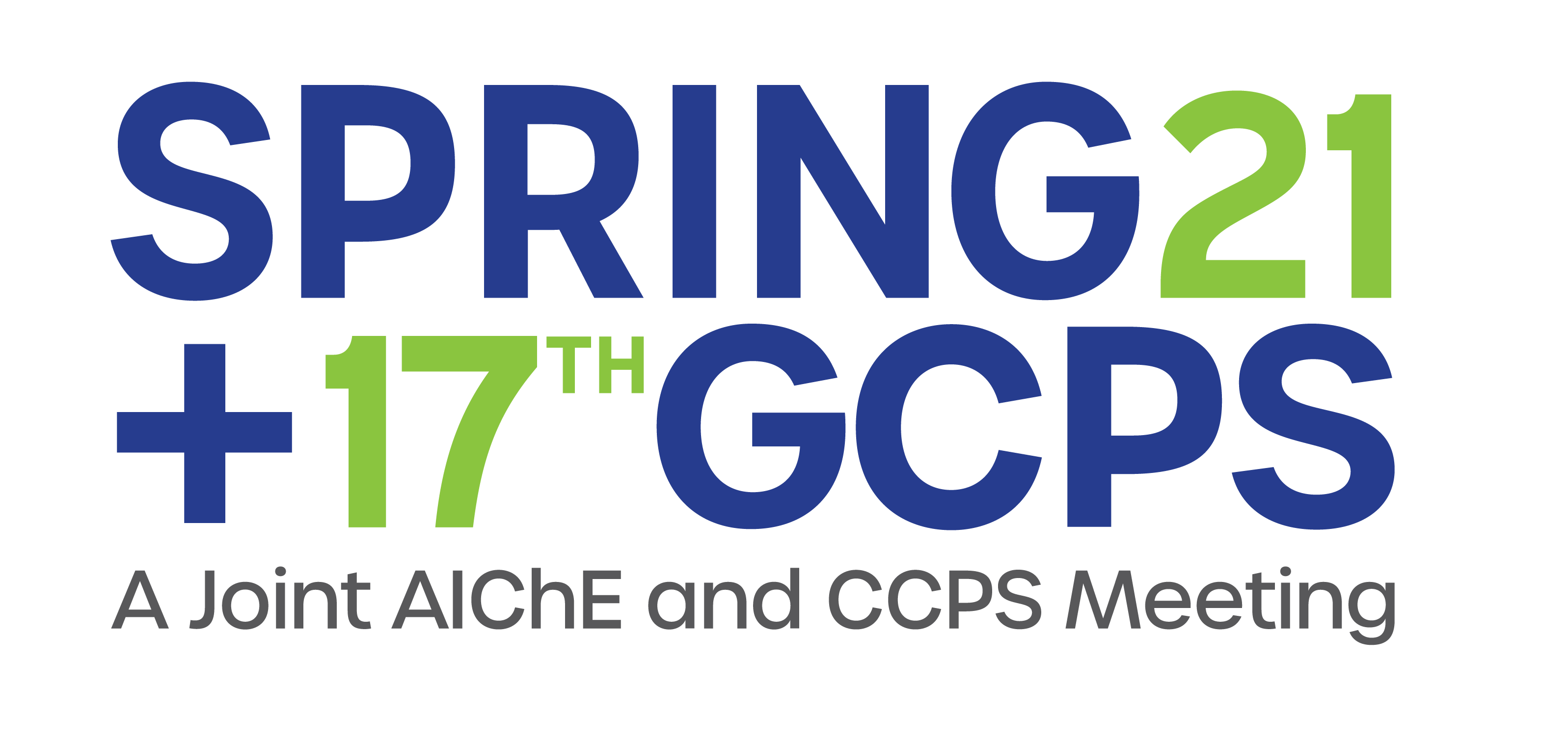
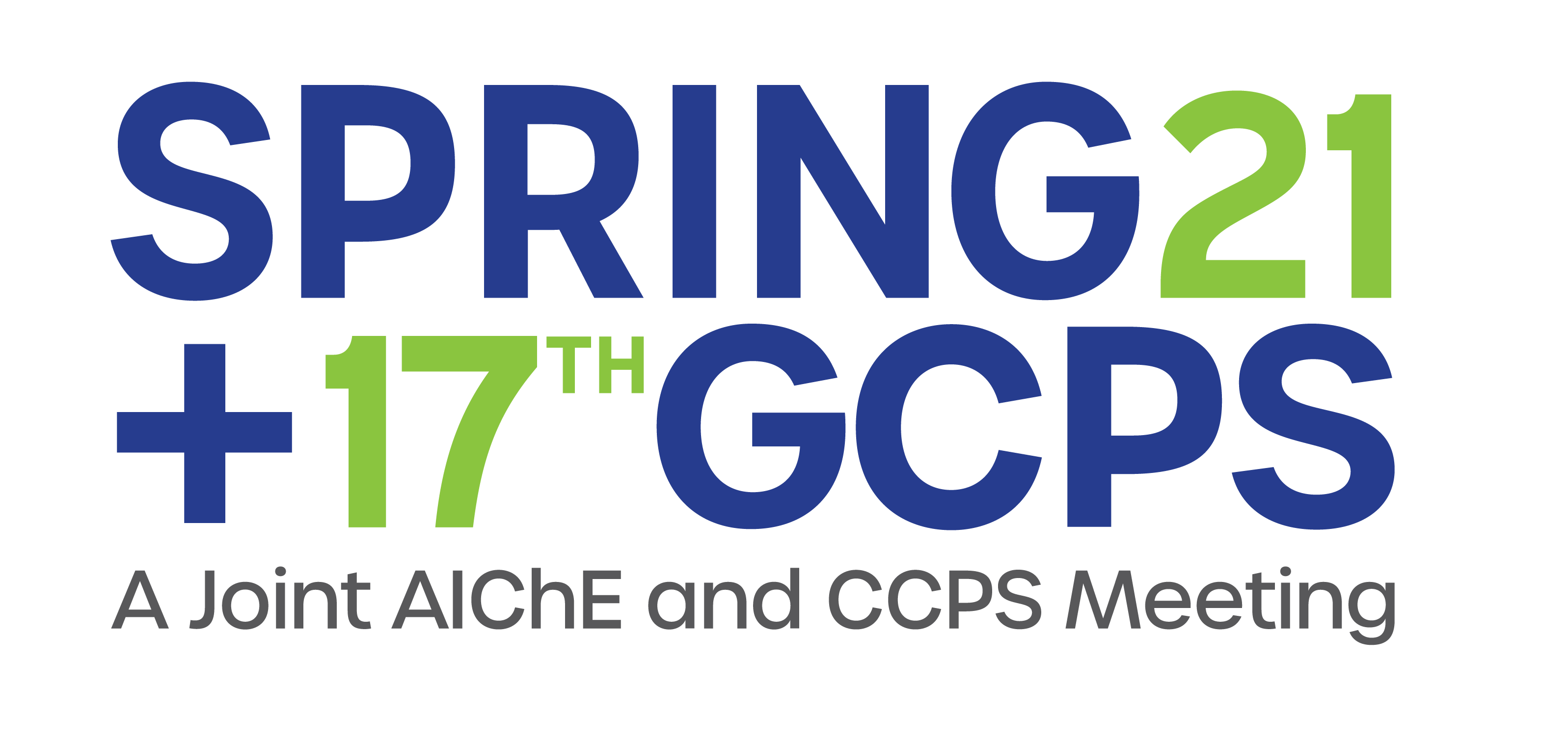
Asset and process safety information is the foundation of key safety, operations, engineering, and financial decisions we make every day. When that information is incomplete, inaccurate, inconsistent, or out of date, we pay for it in terms of higher operational and process risk, higher costs, inefficiencies, and reduced regulatory compliance.
Given the above premise, you would expect the majority of owner operators to formally measure and track the quality of their asset and process safety information and objectively know the true state of their information. After all, as Lord Kelvin said: "if you donât measure it, you cannot manage it." Unfortunately, that is not the case. Our research shows that Over 70% of plants have between 33% to 50%+ of their asset and process safety information missing, incomplete, inconsistent, or out of date with no formal quality management programs.
In this presentation, we will discuss:
- The need for formal quality management processes to frequently measure and report the true quality of their asset and process safety information.
- Underlying cultural, systems-related, and skills-related issues preventing companies from measuring and reporting quality metrics.
- Examples of what to measure and how to communicate it to stakeholders to drive positive change.
- The business benefits for companies that get to do it well.
Presenter(s)
Once the content has been viewed and you have attested to it, you will be able to download and print a certificate for PDH credits.
If you have already viewed this content,
please click here
to login.