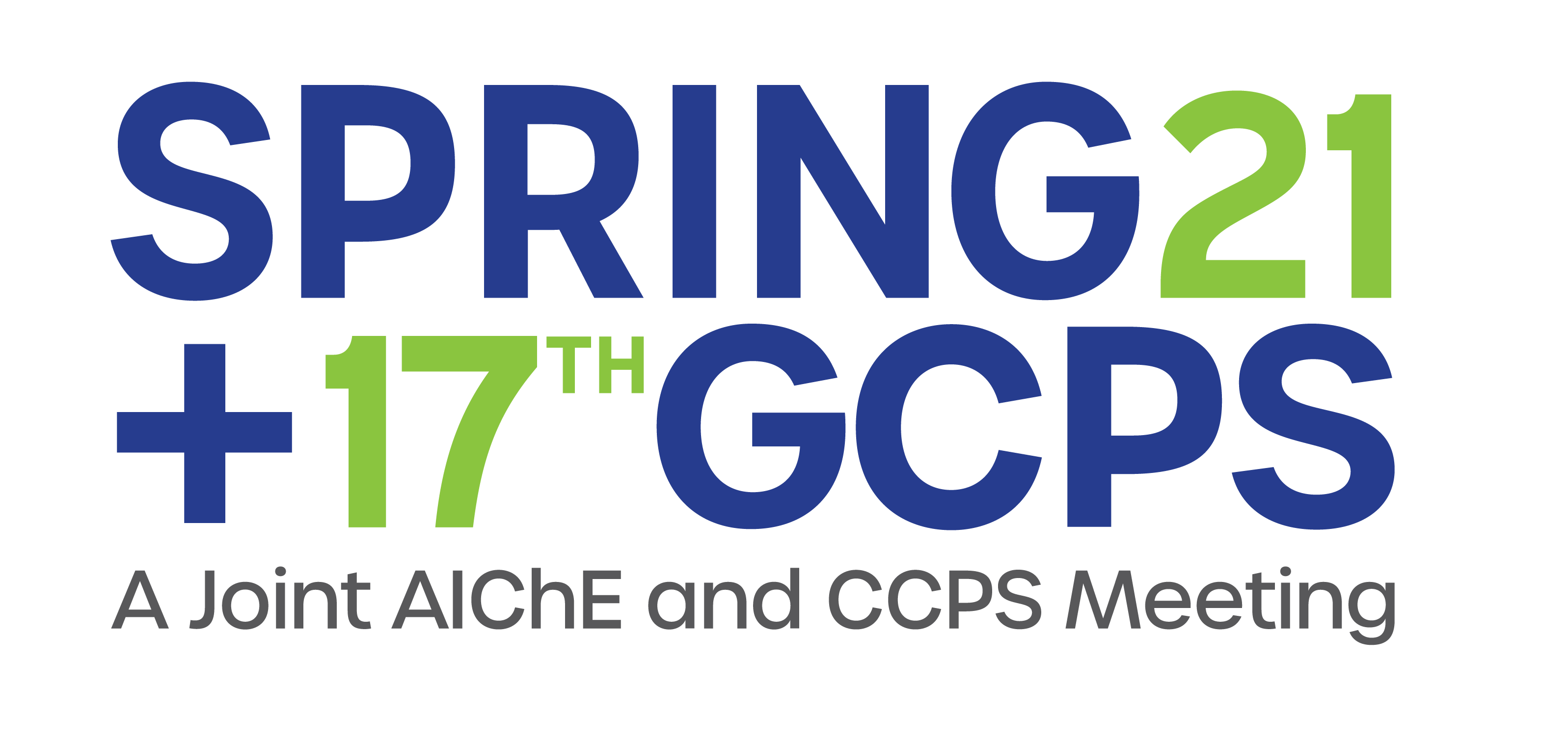
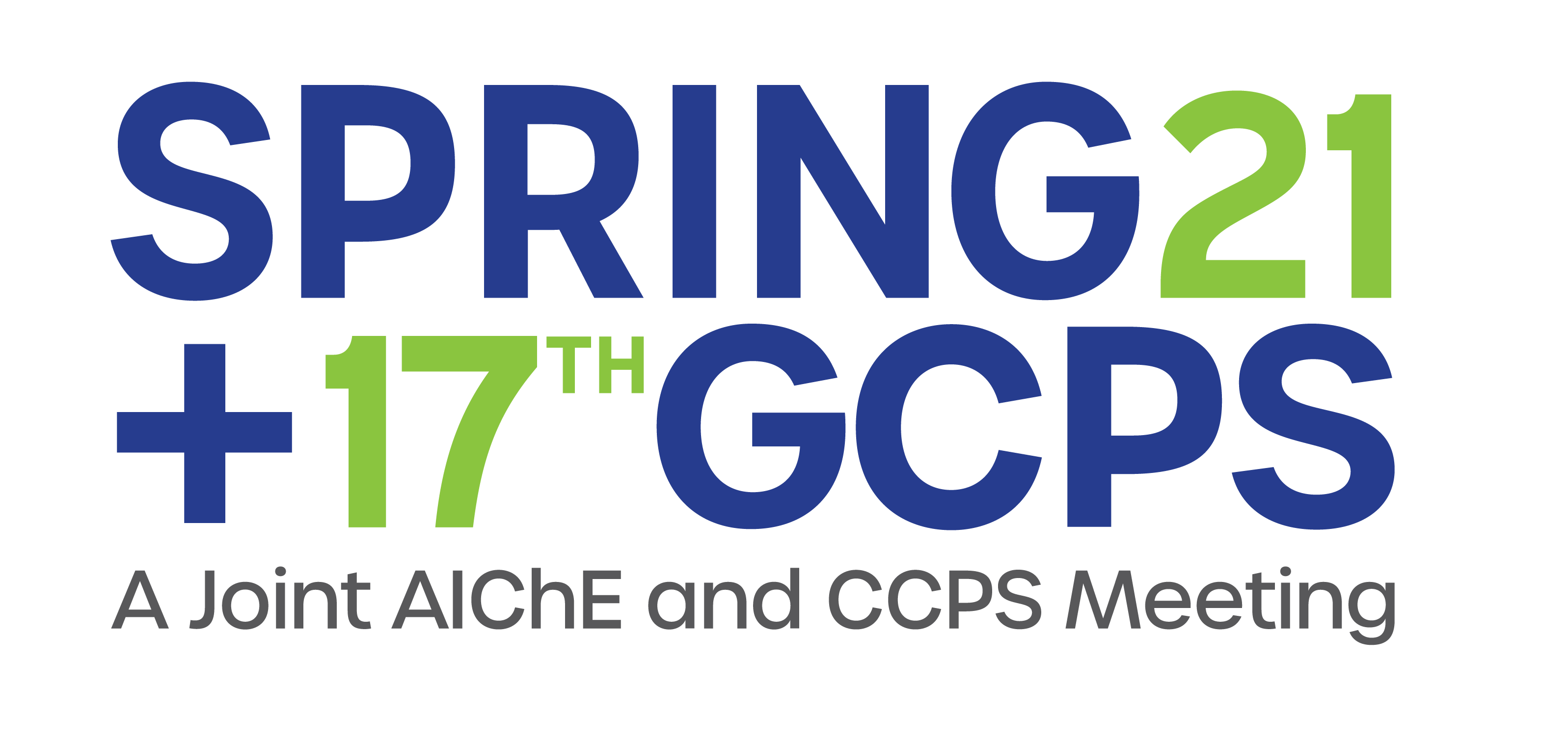
The charge gas compression energy consumption varies typically from 7 to 10% of the total Olefins plant energy requirement. Therefore, in order to improve the plant competitiveness, the energy optimization of this area of the plant is a key issue, once this industry is intensive in energy consumption. Additionally, many crackers aim minimize the environment impact of the operation, in consonance with this thought, Braskem intend achieve zero carbon operation until 2050.
The first step to optimization is to know deeply the system. However, the charge gas compression efficiency determination is not a trivial task. Many factors affect the charge gas compression efficiency, as follow:
- Charge Gas Compressor (CGC) design. Differentes machines require diffentes reciruclation to prevent the surge. The type of the labyrinths could affect the energy consumption as well the design of the intercoolers, pipelines and nock out drums;
- Operation conditions. Usually, low plant feed rates results in necessity of CGC recirculation increasing in order to prevent the surge. High cold area backpressure affects the CGC efforts, resulting in energy consumption increasing, in a same way, the CGC suction pressure, typically determined by the pyrolysis furnaces requirement, impacts in the CGC energy consumption;
- Polythropic efficiency. Oligomers deposits, internal recirculation through the labyrinths and charge gas composition affect the thermodynamic efficiency;
- Lack of focus on recirculation optimization. This part of the gap of energy efficiency is related to the operational actions in the day-by-day, particularly with the using of the existing facilities to control the recirculation in a minimum value to guarantee a proper distance of operation point from surge line
From the operational team point of view, these are uncompressible factors, except the last one (focus on recirculation control). In fact, the operational team has not action on the machine design neither operational condition (plant feed rate, CGC backpressure etc) and has limited action on the machine polythropic efficiency evolution along the campaign.
A KPI frequently used to monitor the overall compression system efficiency is the specific energy consumption (SEC), defined as the total energy consumed by the turbine driver divided by the flow rate of a stream representative of the plant capacity usage, for instance, the charge gas flow rate to cold area. The advantage of this approach is the facility of calculation; it could be easily automatized in the DCS. In other hand, once the general KPI cover all the factors cited above, it can not indicate where the energy has been drained.
Other limitation of this approach KPI is its restrict using to analyze the evolution of a certain compression system, this way it is not possible to use it to compare different machines. In fact, it makes no sense to compare the specific energy consumptions of different charge gas compressors because (i) different CGC designs will require different recirculation flow rate for the same percentage of capacity usage; (ii) eventually, different machines may be being compared at different percentage of capacity usage; (iii) due to the restrictions in other parts of the plant, machines from different units may be operating under different operating conditions (for instance, suction pressure, backpressure from the cold area or overhead temperature of the quench water tower ) and, finally, (iv) CGCs may be being compared at different times in their campaigns, so that the drop in polytrophic efficiency throughout the campaign may compromise the representativeness of the comparison. This way, it is possible imagine that a certain machine with SEC 0.90 GJ/t would be being operated in a more optimized way compared another machine with SEC 0.75 GJ/t.
Many times, it is not easy to monitor the polythropic efficiency. An usual error is to use the design composition of the charge gas. A changing of the value of the polythropic coefficient (Cp/Cv, dependent of the gas composition) from 1.20 to 1.22 results in a increasing of polythropic efficiency calculated by 6 percentage points. Therefore is highly recommended collect and analyze chromatographically the gas composition every time the polythropic efficiency is be monitored. Additionally, this calculation requires expunging the effect of water eventually injected in some charge gas compressors to reduce the discharge temperature, it could be performed by a thermodynamic simulation; usually, this water injection reduces the discharge temperature around 10°C. Additionally, many plants has not facilities to get these samples neither proper instruments to carry out these calculations.
Therefore, the SEC increasing could be due the operational condition changing (for instance, a period of low market demand for monomers or modification of CGC suction pressure for any reason), or unnecessary recirculation. In these cases, the SEC evolution does not mean, in fact, a changing of the intrinsic energy efficiency of the system. In order to overcome these difficulties, these article propose a methodology to monitor the compression system energy efficiency evolution.
This way, a non-phenomenological model for SEC prediction was developed based on the compressor process variables. This model was trained in a period when the compressor was known to be clean. This SEC prediction, based on the compressor data, differs from the methodology to calculate this parameter showed previously (phenomenological approach, based on energy consumption by the turbine driver and charge gas to the cold area), once it does not use any information related to the turbine steam consumption or steam conditions. In other words, this modeling allows the SEC prediction based on the compressor data, implicitly assuming the actual polytrophic and isentropic efficiency data of the period in which the model has been trained. The application of this methodology in a Braskem cracker resulted in a SEC mean absolute error prediction close to 0.46%.
After the training phase, the predicted value of SEC (SECpred) should be very close to the measured value of this KPI based on the turbine driver data. However, over time, it is expected that the measured value (SECactual) will tend to be higher than the value predicted by the non-phenomenological model of prediction based on the compressor data (SECpred), this occurs because the values of actual polytrophic efficiencies should be lower than those that are implicitly incorporated into the trained model while the machine was clean.
Based on that, it was defined the virtual variable PEEM (Polythropic Efficiency Evolution Monitoring) as the difference between the SECactual and SECpred. In the beginning of the campaign, just after the model training, it is expected a PEEM value nearby zero. Along the campaign, the PEEM value will increase.
Thus, this approach allows monitoring the evolution of the CGC polythropic efficiency and verifying its trend over time with a relatively low error, in a practical way, regardless the operational conditions. Case it has been observed a trend of significant reduction in polythropic efficiency, a more detailed analysis should be done and eventual actions to prevent the further loss of efficiency should be considered (for instance, chemicals injections to solubilize the olygomers inside the compressor and prevent its formation, a proper wash oil injection, adjustment in the water injection to cooling down the discharge temperature etc). This initiative is particularly useful in this moment, when many crackers are considering the challenge of extending their campaign length to 8 or 9 years. Finally, this methodology, in theory, could be adopted for any other CGC with minor adaptations, as function of the available instrumentation.
Bibliography:
- Snider, S., Ethylene Plant Cracker Gas Compressor Fouling, AIChE Spring Meeting, Houston, TX EUA, 2006.
- Shaojun, L., Prediction of Cracking Gas Compressor Performance and its Application in Process Optimization. Chinese Journal oh Chemical Engineering.20 (6), 2012.
- ASME Standart, Multistage Centrifugal Compressor Fouling Evaluation at High Power Setings. International Gas Turbine & Aeroengine Congress & Exhibition, Stockhlom, Sweden, 1998
- De Haan, S., The Impact of Fouling and Corrosion in Ethylene Plant Efficiency. AIChE Spring Meeting, San Antonio, TX EUA, 2010.
Presenter(s)
Language
Pricing
Individuals
AIChE Member Credits | 0.5 |
AIChE Pro Members | $19.00 |
Fuels and Petrochemicals Division Members | Free |
AIChE Graduate Student Members | Free |
AIChE Undergraduate Student Members | Free |
AIChE Explorer Members | $29.00 |
Non-Members | $29.00 |