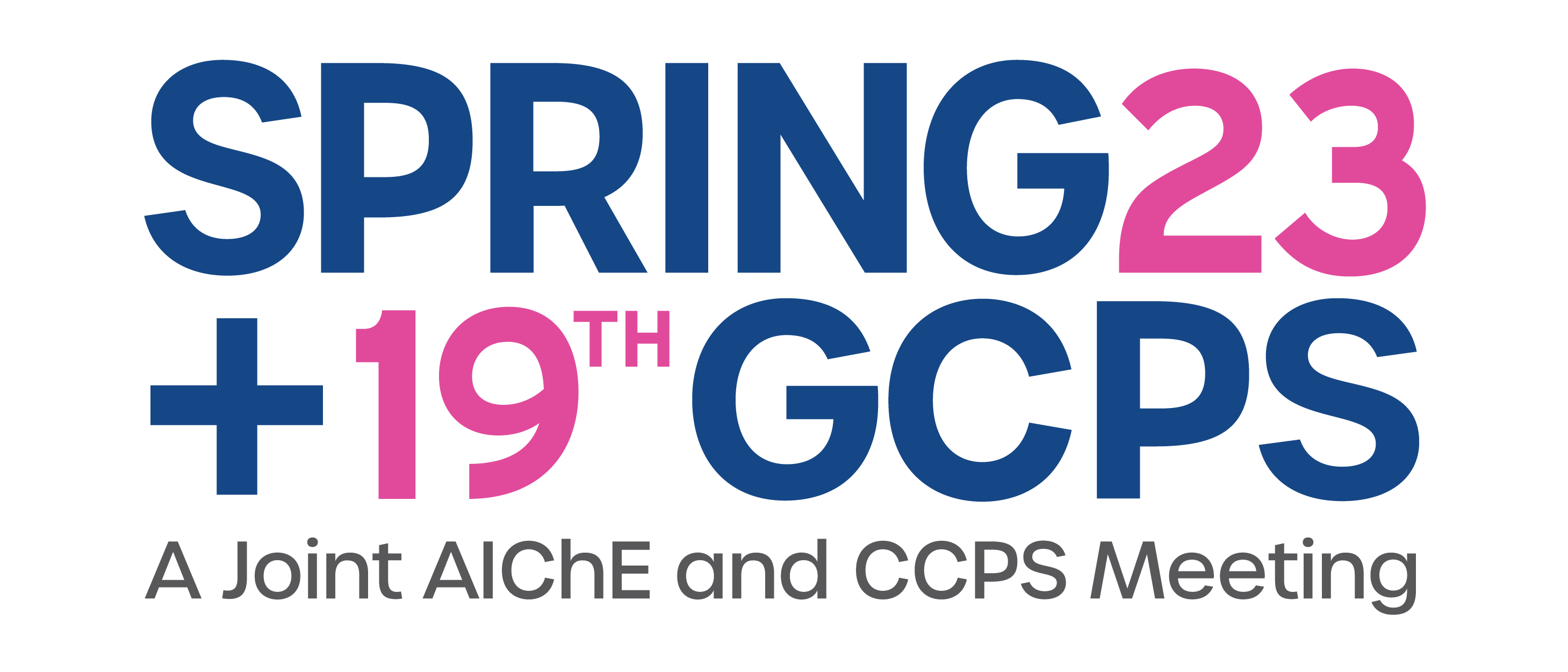
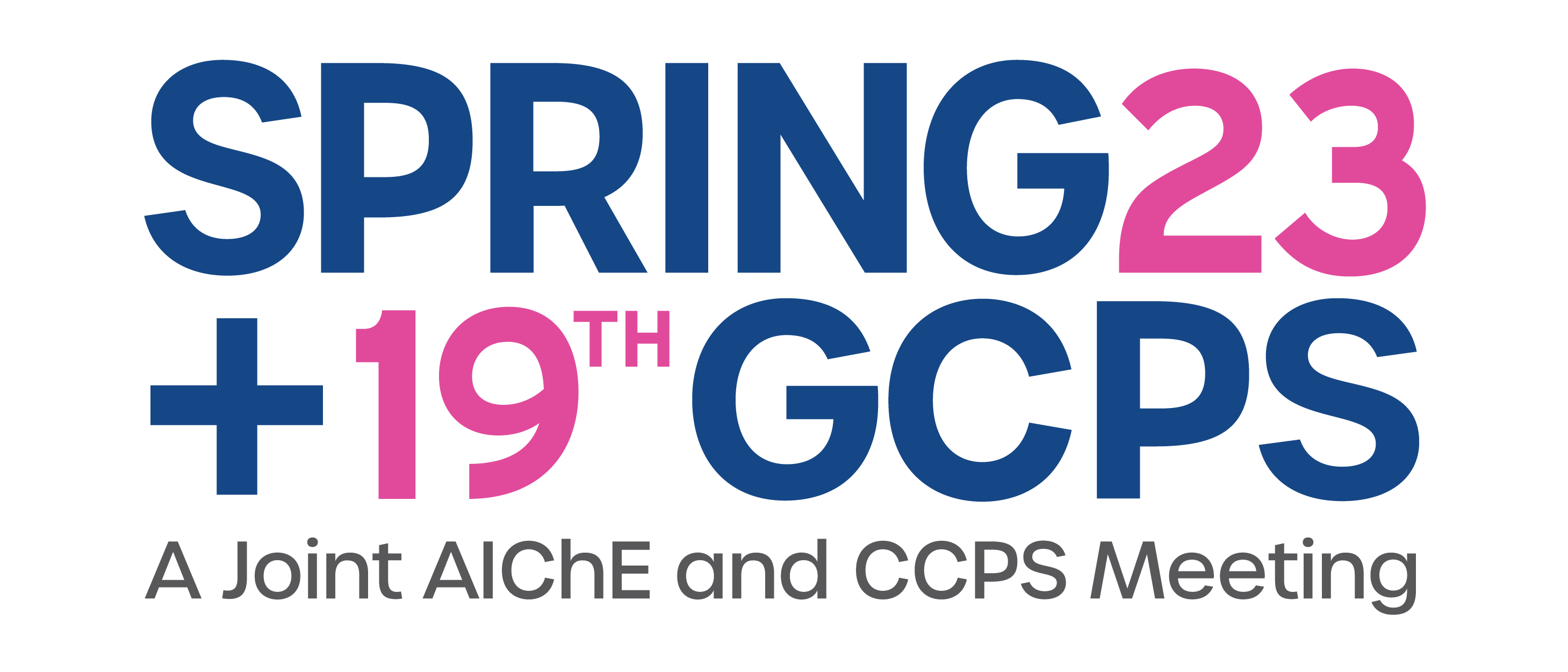
Radiant coils are operated under severe conditions at temperatures even beyond 1100 °C and alternating reducing and oxidizing conditions that represent an enormous challenge for the materials â especially related to their corrosion resistance and mechanical properties.
An oxide barrier layer, generated during furnace start-up on the inner surface of high-alloyed radiant coils, initially protects the material against hazardous atmospheric conditions. With progressive ageing of components, corrosive attack can strongly influence the mechanical properties of the bulk material by reducing e.g. the aged material ductility, but attack of the internal surfaces may also negatively affect the steam cracking process itself due to strong coke deposition. During the aging of materials installed in these very harsh conditions, the originally formed oxide layer is degraded and catalytically active elements like nickel and iron get access to the surface leading to catalytic reactions with the process gas (coking).
Coke deposition on the inner surface of components is a limiting factor when it comes to furnace run lengths, thus affecting e.g. the furnace availability and the maintenance costs, but the need to increase firing rates due to coking also affects the efficiency of the furnace as well as the CO2 footprint.
Normally, small amounts of sulfur-containing components are added to the feedstock to âpoisonâ catalytically active sites present on the inner surface of components in order to reduce the CO formation in the cracked gas. When such concentration limits are exceeded, e.g. by accident, reactions taking place on the inner surface may lead to extensive and irreversible damage to the coil material.
This paper will reflect the strong corrosive attack of centrifugally cast tubes in a several years old radiant tube section resulting from an unintentional, excessive sulfur dosage occurred during preâsulfidation.
Results of metallurgical investigations will be presented, these are focused on the degradation mechanisms leading to the service life reduction of the entire radiant section assembly.
The study of process parameters will also be addressed, as the coking rates suddenly increased after the event, leading to strongly reduced run-lengths.
In this special case study, coke formation was so strong and furnace efficiency so severely decreased, that the operation of the radiant coils was no longer economically justifiable.
Presenter(s)
Language
Pricing
Individuals
AIChE Member Credits | 0.5 |
AIChE Pro Members | $19.00 |
Fuels and Petrochemicals Division Members | Free |
AIChE Graduate Student Members | Free |
AIChE Undergraduate Student Members | Free |
AIChE Explorer Members | $29.00 |
Non-Members | $29.00 |