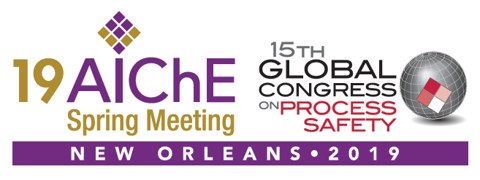
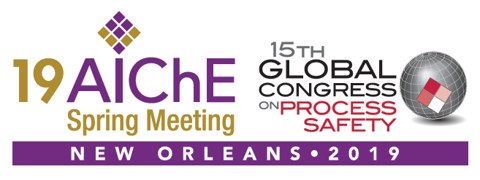
We examined the effects high emissivity coating systems (HECS) have when applied as coating systems to Process Tubes for ethylene steam cracking furnaces. Utilizing tests including carburization, thermal conductivity, and total hemispherical emissivity, HECS were analyzed as a potential method for reducing coking and increasing the heat flux across process tubes. Application of HECS on the external surface of the radiant process tubes could improve the energy consumption1 in the radiant fire box.Incomplete use of all radiant heat in the fire box along with the reoccurring decoking process represent high costs to the industry every year. One of the most important ways to reduce the energy input in steam cracking furnaces per ton ethylene produced is to increase the absorption of radiant heat by the process tube and to uniformly distribute that heat across the tube with no âhot spotsâ thus reducing coke formation inside the process tubes2. Steam cracking is one of the most energy-consuming processes in the petrochemical industry and globally uses approximately 8% of the sectorâs total primary energy3. Improving the energy efficiency and reduced coking of process tubes has an immediate payback that cannot be overlooked in typical ethane or naphtha-based olefin plants4.
A key component to the steam cracking processâ efficiency and throughput is uniform and efficient heat transfer onto and through the process tubes. One technology that has been shown to enhance heat transfer in high temperature process furnaces is HECS5.
The HECS performance on process tubes must be viewed as making each tube a new composite process tube structure with improved thermal performance. The thermal performance enhancements can be defined by improvements in 1. Uniform heating of the tube surface thus reducing hot spots that may attribute to increased coking, 2. Increased heat absorption by the process tube with more heat going to product conversion. Through all this the metallurgy of the process tube is not impacted. A new composite process tube concept is created.
To prove or disprove the above HECS concepts studies and research was undertaken on Duraloy process tube MO-RE 10 with the test procedures detailed below.
Results:
- Carburization Testing:
The impact on carburization on uncoated and HECS coated process tubes was assessed utilizing the NACE International TM0498 test protocol. Control process tubes consisted of thermally aged uncoated tubes being compared with HECS tubes for the rate and degree on carburization. Results of these tests indicate and impact on carburization can be affected by HECS on process tube coking performance. Data will be presented on the HECS effects. Field studies will be underway shortly to verify the laboratory results.
- Thermal Conductivity Testing:
Thermal conductivity is the ability of a material to conduct heat usually measured in watts per meter-kelvin (W/(mâ K). ASTM E1530 was chosen as the test procedure to compare control process tubes with HECS process tubes. Thermal conductivity and heat flux are directly related. Thermal conductivity is the ability of a material to conduct heat, heat flux is defined as âa flow of energy per unit of area per unit of time,â or a rating of quantity of heat that is conducted across the process tube thickness expressed as (Wâ mâ2). How do HECS impact the thermal conductivity must be answered because improved reaction rates in process tubes has been reported from field data where HECS have been utilized on process tubes. So, as thermal conductivity increases, heat flux, or the amount of heat conducted through the tube also increases. Data to identify whether thin filmed HECS lead to increased heat flux will be presented. Laboratory testing will be verified with field heat flux and reaction rate data and compared.
- Total Hemispherical Emissivity Testing:
Total Hemispherical Emissivity (THE) testing via ASTM C 835-06 has been accomplished. THE testing results indicate that an increase of 0.4 - 0.6 in THE can be seen when HECSâs are applied to process tubes. THE increases on the surface of the process tube increases the amount of energy absorbed and distributed across the tube uniformly. Data will be presented on these results and the impact of HECS increase in process tube THE thus leading to positive impacts on the reaction rates and reduced coking.
Conclusion
Can existing process tube performance be improved by making them into composite tubes with HECS on the exterior surface? This study will show what the improvements can be for existing process tube reaction rates and reduced coking. Have we now entered the era of composite process tubes with HECS enhancement?
References
- Georgios D. Stefanidis, Kevin M. Van Geem, Geraldine J. Heynderickx and Guy B. Marin (2008), âEvaluation of high-emissivity coatings in steam cracking furnaces using a nongrey gas radiation model,â Chemical Engineering Journal, pp. 411-421.
- Andres E. Munoz G., Kevin M. Van Geem, Marie-Francoise Reyniers and Guy B. Marin (2014), âCoking Resistance of Specialized Coil Materials during Steam Cracking of SulfurFree Naphtha,â Industrial & Engineering Chemistry Research, pp. 13644-13655.
- Tao Ren, Martin K. Patel and Kornelius Blok (2008), âSteam cracking and methane to olefins: Energy use, CO2 emissions and production costs,â Energy, May, pp. 817-833.
- Tao Ren, Martin K. Patel and Kornelius Blok (2006), âOlefins from conventional and heavy feedstocks: Energy use in steam cracking and alternative processes,â Energy, June, pp. 425-451.
- Kongkaew, Nithitorn & Juyploy, Pachara & Uengbowontrakoon, Poramate & Sri-U-Thai, Pankam & Srimitrungroj, Theerasak. (2016). CFD simulations of high-emissivity coatings on reactor tubes and furnace walls in steam cracking furnace.
Presenter(s)
Language
Pricing
Individuals
AIChE Member Credits | 0.5 |
AIChE Pro Members | $19.00 |
Employees of CCPS Member Companies | Free |
AIChE Graduate Student Members | Free |
AIChE Undergraduate Student Members | Free |
AIChE Explorer Members | $29.00 |
Non-Members | $29.00 |