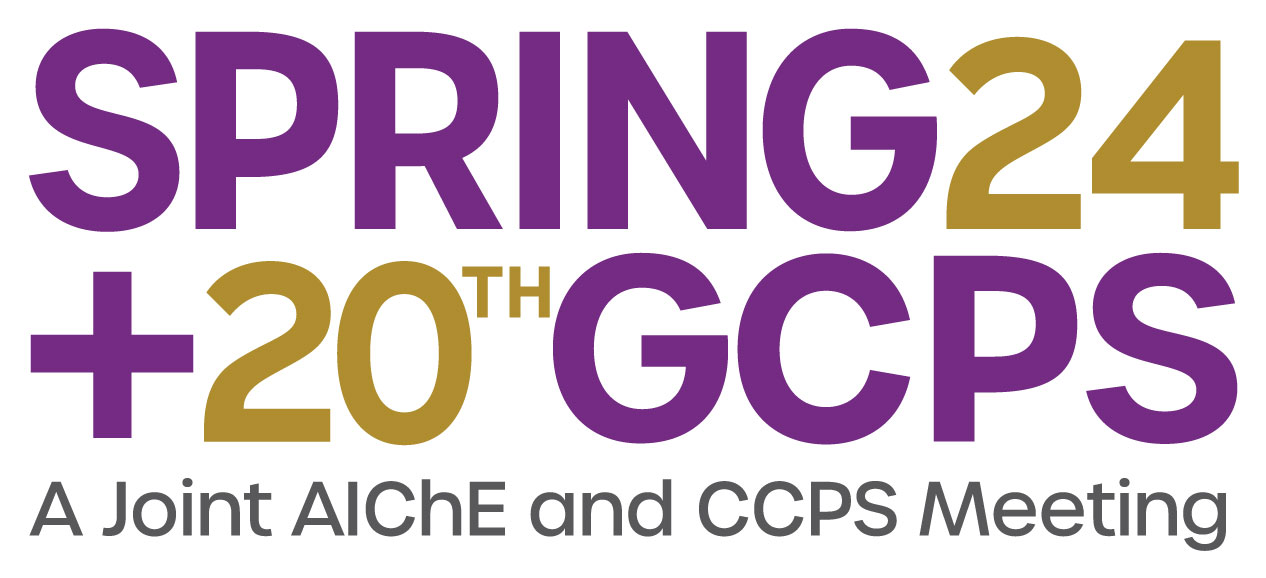
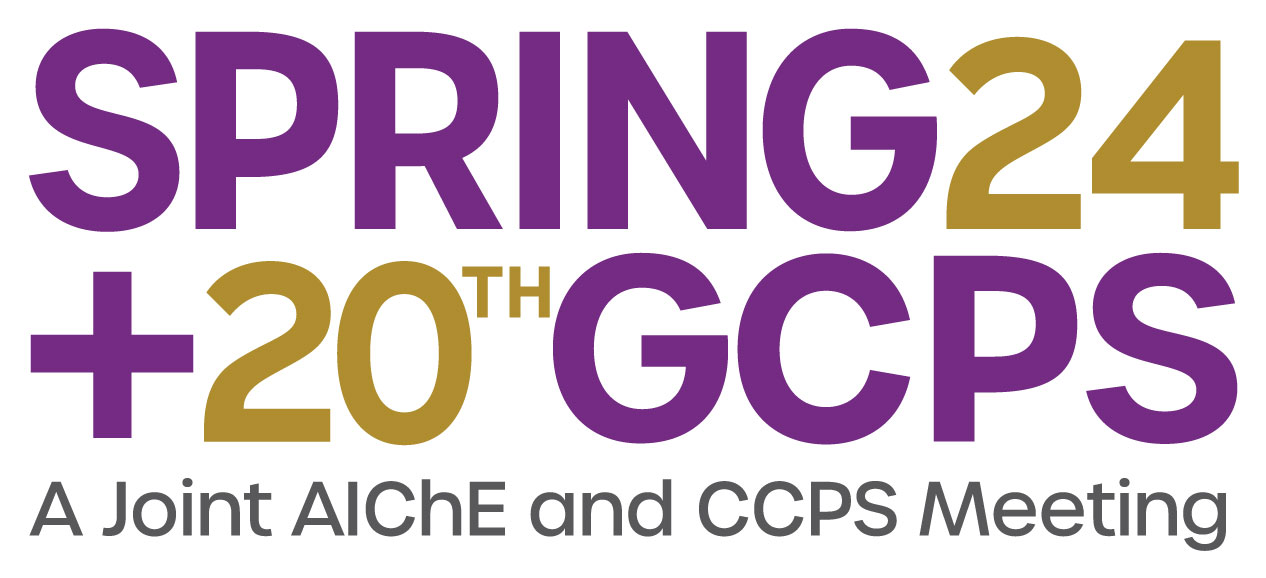
ABSTRACT
The employment of chemical recycling for polyolefin waste management, a promising eco-friendly approach, has gained substantial attention across scientific and industrial sectors. The plastic pyrolysis oil can be blended with naphtha and other hydrocarbon feeds in steam cracking units to yield light olefins or undergo catalytic upgrading and cracking processes. Research has shown that pyrolysis oil derived from polyolefins typically consists of approximately 50-60% mono and diolefins, with cyclic hydrocarbons (naphthenes and aromatics) comprising around 10-15% and the remaining fraction mainly consists of paraffins [1-3]. The presence of paraffins does not pose significant challenges in the production of light olefins from pyrolysis oil. The primary hurdles for steam cracking units arise from the olefins and diolefins. Studies on these units have revealed that when the feed contains more than 2% olefins, secondary reactions intensify [4]. It is important to note that pyrolysis oils contain various olefins, classifiable into α-olefins and iso-olefins. Based on earlier research [3,5], pyrolysis oil from polypropylene, containing iso-olefins as byproducts, presents fewer challenges in the production of light olefins due to steric hindrance from methyl groups. The main challenges are associated with linear α-olefins and diolefins, the primary components in the thermal pyrolysis of polyethylene waste [6], which are why 1-decene (α-olefin) and 1,9-decadiene (diolefin) were selected as model compounds for plastic pyrolysis oil in this research. Using the steam-treated (at 800 °C for 4h) ZSM-5 catalyst (sample: CBV 5524G, SiO2/Al2O3= 50), cracking of olefins and diolefins displayed distinct product distributions through separate reaction pathways (Figure 1).
During the catalytic pyrolysis of 1-decene (α-olefin), which occurred within the temperature range of 250 °C to 450 °C at varying contact times, the conversion process included isomerization followed by chain scission. This led to the production of lighter olefins. The dominant reaction pathway was skeletal isomerization, generating branched C10 isomers (nonene with a methyl group), which was notably more prevalent than double bond rearrangement, particularly at higher conversion levels. As conversion increased, chain scission of 1-decene isomers intensified, resulting in the production of lighter olefins such as butene and propylene. Consequently, in the case of 1-decene catalytic pyrolysis, the initial reactions involved isomerization, followed by chain scission, ultimately leading to the production of light olefins. Later in the process, cyclization of olefins occurred (Figure 2-left).
In contrast, during the catalytic pyrolysis of 1,9-decadiene (diolefin), the major products were cyclic compounds, particularly cyclohexenes with an alkyl group, and light olefins. Elevating the reaction conditions, such as increasing temperature and contact time, resulted in greater conversion of 1,9-decadiene into cyclic compounds and chain scission into lighter diene compounds. Notably, the presence of lighter conjugated diolefins generated through chain scission of 1,9-decadiene, facilitated the Diels-Alder reaction, promoting cyclization, aromatic production, and, consequently, coke formation. This phenomenon was less prevalent during the cracking of 1-decene, as it did not produce conjugated diene compounds, thus limiting the cyclization process. Hence, the reaction pathways of 1,9-decadiene catalytic pyrolysis, as
illustrated in Figure 2 (right), included chain scission, cyclization, ring expansion, and the formation of cyclohexene rings, which subsequently converted to aromatic compounds [7].
In conclusion, the analysis of structural characteristics of these olefins and diolefins indicates a significantly higher likelihood of forming butadiene derivatives within the diolefins category compared to α-olefins. Consequently, diolefins exhibit enhanced susceptibility to Diels-Alder reactions, leading to the eventual creation of diverse cyclic compounds, culminating in aromatics and polyaromatics. In light of these considerations, a comprehensive assessment, encompassing the proportion of polypropylene in the pyrolysis feedstock, alongside the quantification of linear diolefins and α-olefins, offers precise insight into the operational dynamics of the ensuing light olefin production unit.
1. Belbessai S, Azara A, Abatzoglou N: Recent Advances in the Decontamination and Upgrading of Waste Plastic Pyrolysis Products: An Overview. Processes 2022, 10:733 https://doi.org/https://doi.org/10.3390/pr10040733.
2. Soják L, Kubinec R, Jurdáková H, Hájeková E, Bajus M: High resolution gas chromatographicâmass spectrometric analysis of polyethylene and polypropylene
thermal cracking products. Journal of Analytical and Applied Pyrolysis 2007, 78:387-399 https://doi.org/https://doi.org/10.1016/j.jaap.2006.09.012.
3. Kusenberg M, Zayoud A, Roosen M, Thi HD, Abbas-Abadi MS, Eschenbacher A, Kresovic U, De Meester S, Van Geem KM: A comprehensive experimental investigation of plastic waste pyrolysis oil quality and its dependence on the plastic waste composition. Fuel Processing Technology 2022, 227:107090 https://doi.org/https://doi.org/10.1016/j.fuproc.2021.107090.
4. Baumgartner AJ, Engineers AIoC: Feedstock Contaminants in Ethylene Plants--an Update: American Institute of Chemical Engineers; 2004.
5. Abbas-Abadi MS, Kusenberg M, Zayoud A, Roosen M, Vermeire F, Madanikashani S, KuzmanoviÄ M, Parvizi B, Kresovic U, De Meester S, et al.: Thermal pyrolysis of waste versus virgin polyolefin feedstocks: The role of pressure, temperature and waste composition. Waste Management 2023, 165:108-118 https://doi.org/https://doi.org/10.1016/j.wasman.2023.04.029.
6. Abbas-Abadi MS, Zayoud A, Kusenberg M, Roosen M, Vermeire F, Yazdani P, Van Waeyenberg J, Eschenbacher A, Hernandez FJA, KuzmanoviÄ M, et al.: Thermochemical recycling of end-of-life and virgin HDPE: A pilot-scale study. Journal of Analytical and Applied Pyrolysis 2022, 166:105614 https://doi.org/10.1016/j.jaap.2022.105614.
7. Joshi YV, Bhan A, Thomson KT: DFT-Based Reaction Pathway Analysis of Hexadiene Cyclization via Carbenium Ion Intermediates: Mechanistic Study of Light Alkane Aromatization Catalysis. The Journal of Physical Chemistry B 2004, 108:971-980 https://doi.org/10.1021/jp036205m.
Presenter(s)
Language
Pricing
Individuals
AIChE Member Credits | 0.5 |
AIChE Pro Members | $19.00 |
Fuels and Petrochemicals Division Members | Free |
AIChE Graduate Student Members | Free |
AIChE Undergraduate Student Members | Free |
AIChE Explorer Members | $29.00 |
Non-Members | $29.00 |