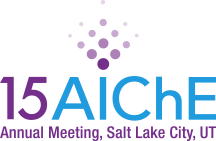
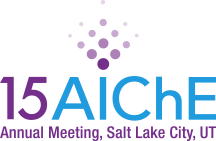
The continuous direct compression manufacturing process consists of several loss-in-weight (LIW) feeders, a horizontal mixer, a surge hopper, and tablet press equipped with a near infrared (NIR) probe at the die-filling station of the tablet feed frame. A system-wide deterministic dynamic model was used to fit dispersion coefficients within the various elements for a given formulation/throughput using the feed frame NIR to measure the system response. This partial differential non-linear algebraic system model consisting of ~8,000 equations is sufficiently complex that it cannot be solved real-time with the current technology. This necessitates a second, reduced system model based upon the original deterministic model and uses thousands of digital experiments to create a set of response surfaces. The result is a data-driven version of the model that can be executed real-time using a PAT controller (e.g. SynTQ) to assess the impact of feeder variability on the final product within the distributed control system (e.g. DeltaV). The real-time reduced system model provides prediction of the feed frame concentration, the time when a disturbance will reach the die-filling station, and the time when the disturbance will clear the system.