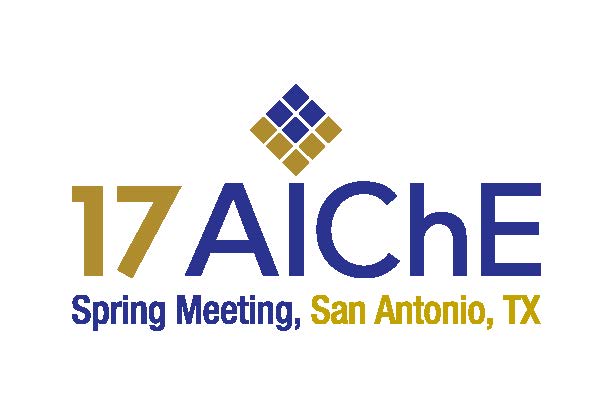
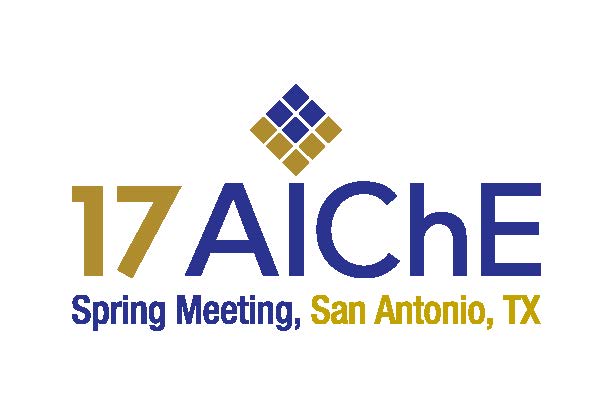
Authors: Van Geem Kevin M.1,*, Battin-Leclerc F.2, Bellos G.3, Heynderickx G.1, Buysschaert W.4, Cuenot B.5, Djokic M.R.1, Faravelli T.6, Theis G.7, Jakobi D.8, Lenain P.9, Munoz A.E.G.10, Olver J.11, Dedeyne J.N.1, Vangaever S.1, Honnerová P.12, Veselý Z.12
1 Laboratory for Chemical Technology, Ghent University, Ghent, Belgium; 2 Centre National de la Recherche Scientifique, Nancy, France; 3 DOW Benelux B.V., Terneuzen, The Netherlands; 4 CRESS B.V., Breskens, The Netherlands; 5 European Centre for Research and Advanced Training in Scientific Computation, Toulouse, France; 6 Politecnico di Milano, Milan, Italy; 7 John Zink International Luxembourg SARL, Luxembourg; 8 Schmidt + Clemens GmbH +CO. KG, Lindlar, Germany; 9 Ayming France, Lyon, France; 10 AVGI, Ghent, Belgium; 11 Emisshield Inc., Blacksburg, Virginia, USA; 12 New Technologies Research Centre, University of West Bohemia, Plzen, Czech Republic
The goal of this work is to develop and demonstrate the steam cracking furnace of the 21st century by drastically improving the energy efficiency of the current state-of-the-art, in a cost effective way, while simultaneously reducing emissions of greenhouse gases and NOX per ton of ethylene produced by at least 25%. This project aims to implement and combine several of the latest technological innovations in the field of energy efficiency and fouling minimization by proving that these technologies work properly under industrial circumstances, supported by industrial partners, knowledge institutions and research and technological organizations. The ultimate objective is to deploy the furnace at the demonstrator at commercial scale with the most effective technologies improving efficiency of ethylene furnaces evaluated on pilot scale.
Ethylene is a basic building block of the chemical industry, and is the link between chemical companies and petroleum refiners. Steam cracking is the most energy-consuming process in the chemical industry and globally uses approximately 8% of the sectorâs total primary energy. Improving the energy efficiency has an immediate pay-out because energy cost counts for a substantial part of the production costs in typical ethane or naphtha based olefin plants. One way to reduce the energy input in steam cracking furnaces per ton of ethylene produced is to reduce coke formation on the reactor wall. During the course of a run, deposited coke can reduce the heat-transfer efficiency of the firebox by 1-2%, resulting in a 5% increase in fuel consumption. To bring the energy consumption of the whole furnace down, the project will use the following levers: the use of renewable fuels and oxy-fuel combustion, high emissivity coatings emitting in the non-absorbent flue gas spectrum, novel radiant coil alumina forming alloy tubes that lower the coking rate leading to a lower outside tube temperature, and enhanced heat transfer between flue gas and the process by 3D reactor technology.
An important challenge for the petrochemical industry is the upcoming stronger environmental regulations, in particular related to NOX and CO2. To reduce NOX emissions the use of advanced oxy-fuel combustion will be demonstrated. The advantage is clear; because no nitrogen is added (apart from leakages), almost no NOX is produced. An additional advantage is that the produced flue gas is a concentrated CO2 stream, that can be more easily captured, stored or used for other applications (Carbon Capture and Storage), for example in chemical looping. Novel experimental data combined with life cycle analysis will be used to assess if the use of bio-gas and bio-oil is truly more sustainable or is just practically infeasible. These bio-fuels will be considered in the project as they can be considered renewable, and hence, decrease net CO2 production. A logical concern for bio-oil is the possible presence of fuel-bound nitrogen. Detailed reaction mechanisms describing the formation of NOx from bio-gas and bio-oil combustion will be developed and validated, also under oxy-fuel combustion conditions. Computational Fluid Dynamics (CFD) will be adopted to scale-up these novel technologies.
One of the most expensive parts of any cracking furnace (â 1/3 of the furnace cost) are the reactors, the so-called coils. Recent innovations in the development of new coil materials, especially 45Ni35Cr steels, or materials with an increased content of aluminum (â6%) that can be operated up to 1200°C will be considered. The project will provide data that show if there is a benefit or not of using these more advanced but more costly materials. Moreover, the best material will be combined with another recent innovation, the 3D Swirl flow reactor design or the SCOPE technology. The use of advanced coil materials, combined with 3D reactor designs, improved process control, and more uniform heat transfer could increase run lengths, reducing simultaneously CO2 emissions and the lifetime of the furnaces. It is believed that the current design of these 3D reactors is far from optimal, and that CFD can lead to the design of radiant coils with even better performance.
One of the main objectives of this project is to increase the energy efficiency of the radiation section of a steam cracking furnace, minimizing exergy losses. Not only will the radiation section be studied, but the furnace as a whole. A key element to realize this is the use of high emissivity coatings manufactured and studied under real furnace conditions in the project. Coating different sections of the furnace will be considered, such as radiant walls/floor of furnace, radiant roof panels, burners & burner blocks, process coils/tubes, as well as convective section tubes and walls. In addition to higher heat absorption, coating the external surface of radiant coils can improve the surface homogeneity and eliminate hot spots on the tube walls. An additional benefit will be extended run lengths resulting in less energy spent annually for decoking the radiant coils.
IMPROOF will demonstrate the advantage of combining all these technological innovations, with an anticipated reduction of emissions, and increase of the time on stream and thermal efficiency.