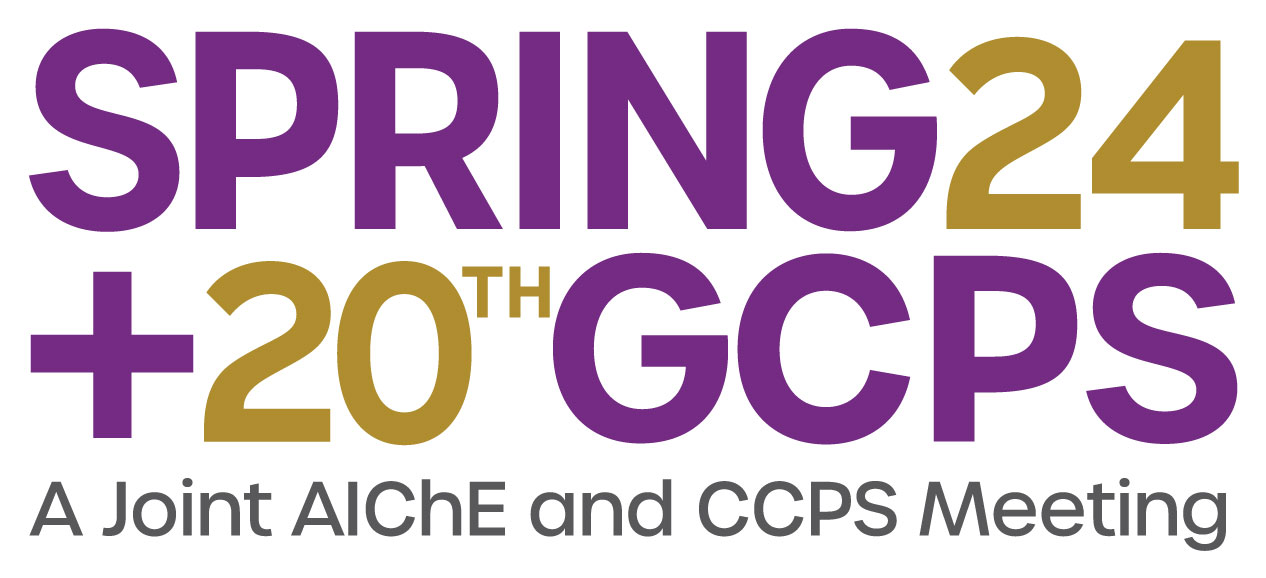
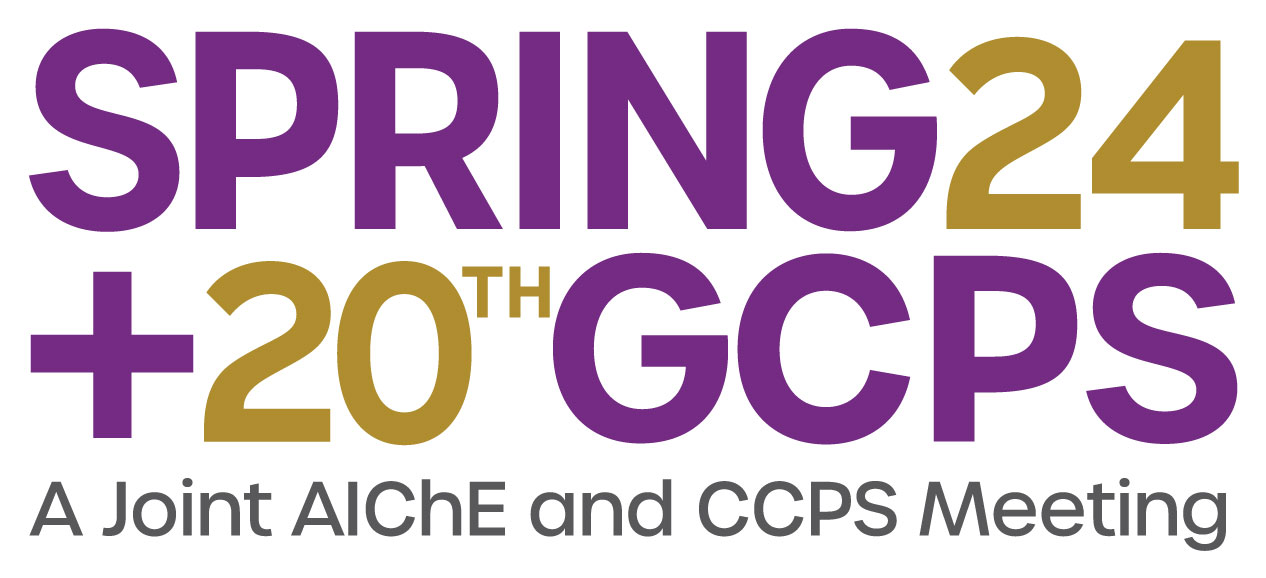
Coolbrook is a Finnish-Dutch-British technology and engineering company on a mission to de-carbonize major industrial sectors such as petrochemicals and chemicals, iron and steel and cement. Coolbrook's proprietary, revolutionary RotoDynamic Technology generates process heating for high temperature processes with CO2-free electricity and replaces burning of fossil fuels in multiple hard-to-abate industrial processes.
Coolbrookâs RotoDynamic ReactorTM (RDRTM) can reach 100% CO2 free olefin production. It is an electrically driven turbomachine where one or a cascade of stator-rotor-diffuser sequences heat gaseous steam-hydrocarbon mixture efficiently and with extremely low residence time into reaction temperature. The heat increase occurs intrinsically in the heated gas and results from conversion of rotor blade -induced kinetic energy of the gas into thermal energy by rapidly slowing the velocity of the gas. As the velocity of the gas slows down from supersonic to subsonic, a shockwave occurs that enhances the conversion of kinetic energy into heat. Using RDR with renewable electric power makes it one of the most promising technologies capable of cutting 100% of process emissions (CO2, NOx and particulate emissions).
Linde Engineering is a leading technology partner for plant engineering and construction worldwide. Linde Engineering has supplied its Ethylene Technology for eighty years with proven success and a well-known reputation. Linde can offer all kinds of supplies from feasibility studies, Pre-FEED/FEED packages up to the complete scope of work for an ethylene complex including procurement, construction, and commissioning/start-up services. Linde has a tremendous knowledge not only on how to design ethylene plants but more importantly on how to build a reliable ethylene plant.
Coolbrook and Linde Engineering are in a strategic partnership to collaborate on the development and deployment of Coolbrookâs RotoDynamic Reactor technology to replace burning fossil fuels with clean electricity in ethylene plants world-wide. Coolbrook and Linde Engineering are jointly developing an offering for petrochemical companies to be able to achieve a significant reduction in emissions and to boost profitability through increased olefin yields and improved uptime through reduced coking.
RDR can be implemented step by step also at existing cracker sites into the existing infrastructure. In this way both the environmental and commercial viability are maximized. Coolbrook/Linde integration concepts are flexible towards the available and required utilities of the existing plant set-up and allow steam crackers to minimize the integration efforts in transition towards electrified steam cracking.
Conceptual integrating of electric cracking technologies into existing steam crackers
Powering steam cracking with electricity avoids the inefficiencies of combustion-based process heating. During past decades, a significant effort has been put into improving the thermal efficiency of conventional cracking furnaces and this has led to efficient capturing of the furnace flue gas energy in feedstock pre-heat and superheated high-pressure steam generation. The integration between furnaces and downstream energy consumers, such as compressors and distillation units, has produced a complex system where changes in one energy source or sink will affect the others and potentially move the system away from energetic optimum.
Transition towards low-carbon industry requires step-wise adoption of new technologies, and the inertia caused by existing plant integration set-ups can lead to sub-optimal choices for emission reduction technology, such as hydrogen firing or carbon capture, to maintain the current optimum set by conventional furnace-based systems. Breaking the convention requires new thinking and investigating the plants at system level to find a new optimum for the integration that allows selection of most efficient and cost-effective reactor technology.
Coolbrook RotoDynamic Reactor offers flexible selection of feed pre-heat system, quench energy valorization and is flexible towards feed temperature as long as the feedstock is vaporized and superheated to avoid condensation. Linde Engineering has a vast experience and toolbox to design efficient plant-wide integration concepts. Coolbrook and Linde Engineering will present joint conceptual integration concepts that allow the customer to choose the best available low-carbon cracking technology while maintaining or improving the overall profitability of the assets
Exemplary integration scenarios
The conference contribution will demonstrate different options for integrating Coolbrook RDR into existing steam crackers, ranging from concepts with steam generation as required for existing plant conditions to solutions with minimized specific electricity consumption per ton feedstock.
These concepts will serve as a basis for tailored process integration offerings that will be provided by Linde Engineering and Coolbrook. Specific requirements of each customerâs plant-wide utility system will be taken into consideration when optimizing the final integration concept for minimized CAPEX and OPEX and maximized profitability.
The installation of a RDR is simple due to its modular structure and small size compared to conventional crackers. In RDR concept, preheating is significantly less complex and more flexible than conventional convection sections. Downstream recovery processes, equipment and utilities can also be simplified due to the more favorable composition of the olefins produced in the RDR.
RDR Pilot Plant
Coolbrookâs RDR Pilot plant in Brightlands Campus in Geleen, Netherlands was built to test and develop RDR Technology for electrified steam cracking of hydrocarbon feedstock.
The test program consists of a variety of test runs divided over several basic raw materials. Duration of test runs vary between a few hours needed for yield testing and a few weeks needed for testing coking tendency and reliability. The pilot will function as a step towards commercial demonstration of RDR technology. The project will deliver design tools and proof-of-concept for commercial implementation, which will have industrially relevant size and will be connected to an existing and operating ethylene cracker. The capabilities of the pilot plant and a summary of available results will be presented.
Presenter(s)
Language
Pricing
Individuals
AIChE Member Credits | 0.5 |
AIChE Pro Members | $19.00 |
Fuels and Petrochemicals Division Members | Free |
AIChE Graduate Student Members | Free |
AIChE Undergraduate Student Members | Free |
AIChE Explorer Members | $29.00 |
Non-Members | $29.00 |