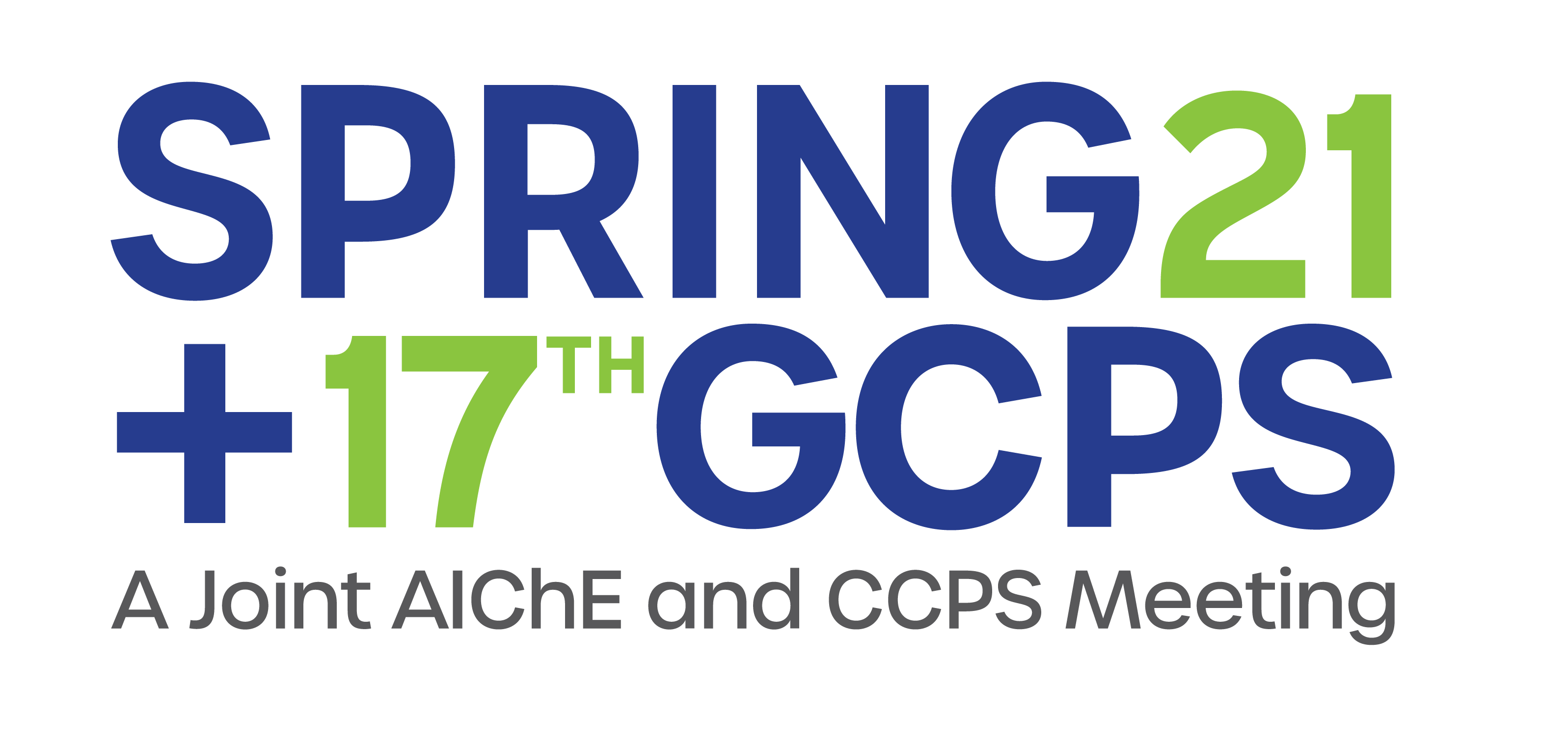
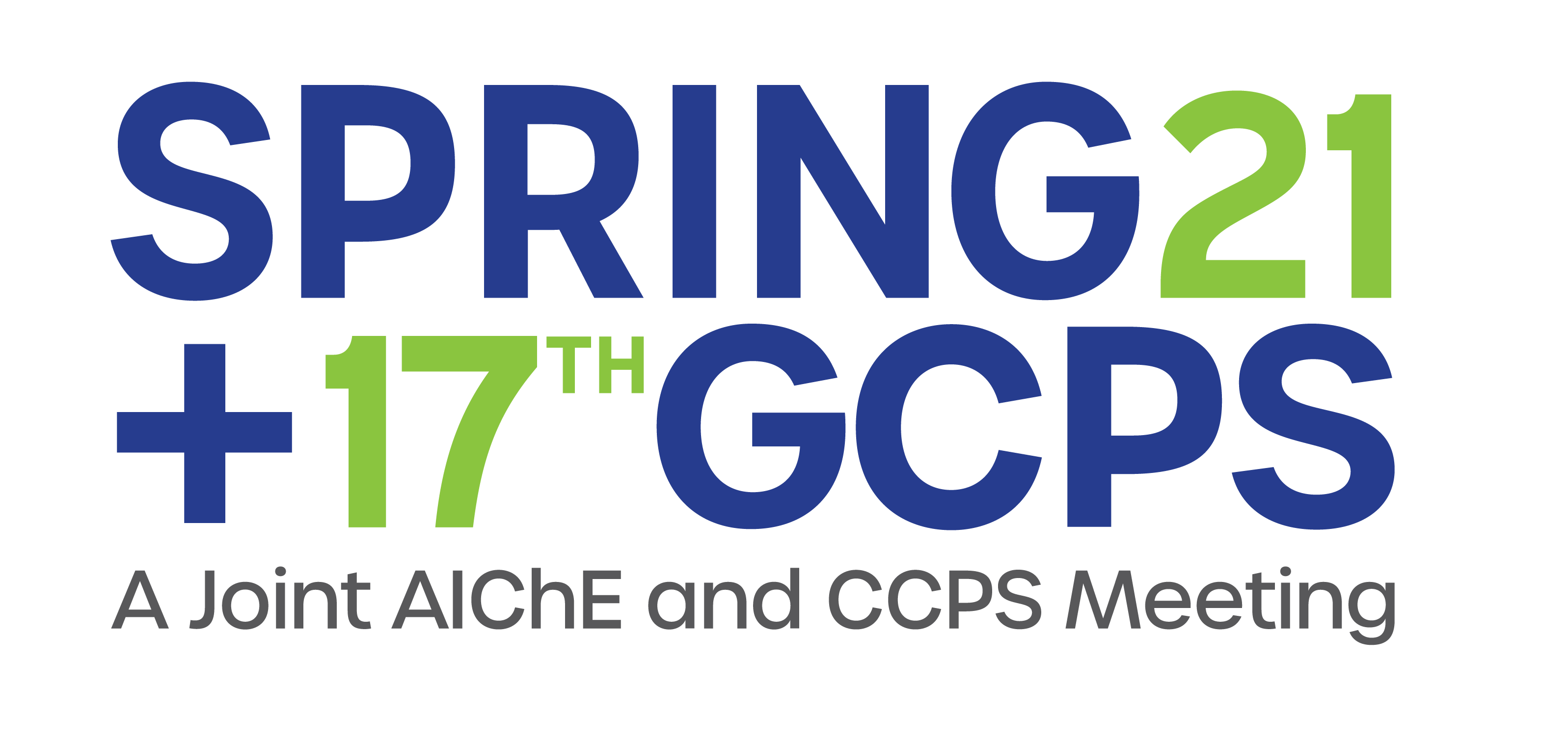
In industrial Methanol distillation, a stream consisting of a multi-component mixture of Methanol, Water and a number of trace components must be refined into AA grade Methanol, containing less than 10 wt-ppm of the middle-boiling Ethanol. Current Methanol production economic objectives also dictate that close to 100% of Methanol entering the column is recovered as product, while ensuring all hydrocarbons (primarily consisting of Methanol not being recovered as product) is recycled back to the reforming process to make syngas. In the recent past these requirements have
prompted some engineers to question the âstatus quoâ design of using a distillation column with a side draw to achieve these operational objectives, particularly with regards to energy efficiency.
The objective of this paper is to study the energy efficiency benefits that could be realized by different column configurations. To this end five practical column configurations that include a divided wall column, a recovery column arrangement, a side draw column, a cut divided wall column as well as a direct synthesis configuration were analyzed with the aid of an industrial process simulator. All configurations investigated were able to match the strict industrial product specifications and operational objectives. The energy usage of the column configurations were improved through a systematic analysis and the results revealed that all intensified columns have a superior energy usage compared to the direct synthesis configuration as expected, but with the gains limited to only 3%. An unbiased consideration of the energy efficiency results, together with other external factors including cost of capital and operability, shows that the recovery column configuration would be the most practical choice despite the presence of the divided wall column configuration which represents a greater level of intensification and integration.
prompted some engineers to question the âstatus quoâ design of using a distillation column with a side draw to achieve these operational objectives, particularly with regards to energy efficiency.
The objective of this paper is to study the energy efficiency benefits that could be realized by different column configurations. To this end five practical column configurations that include a divided wall column, a recovery column arrangement, a side draw column, a cut divided wall column as well as a direct synthesis configuration were analyzed with the aid of an industrial process simulator. All configurations investigated were able to match the strict industrial product specifications and operational objectives. The energy usage of the column configurations were improved through a systematic analysis and the results revealed that all intensified columns have a superior energy usage compared to the direct synthesis configuration as expected, but with the gains limited to only 3%. An unbiased consideration of the energy efficiency results, together with other external factors including cost of capital and operability, shows that the recovery column configuration would be the most practical choice despite the presence of the divided wall column configuration which represents a greater level of intensification and integration.
Presenter(s)
Once the content has been viewed and you have attested to it, you will be able to download and print a certificate for PDH credits.
If you have already viewed this content,
please click here
to login.