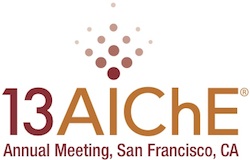
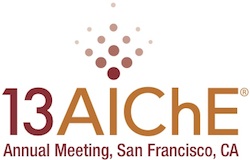
Introduction
Capsule filling using nozzle dosators (ND) has been widely investigated (Jones, 2001; Newton, 2012) and it is one of the main technologies used by pharmaceutical industry today. Nozzles come in sizes that match the diameter of capsules (from 00 to 5), and deliver a specific volume of powder into capsules. However, the amount of powder that the smallest nozzle (size 5) can handle is in the range of 40 mg-80 mg (depending on the density of the powder formulation).
Some new and prospective pharmaceutical products require the handling of even smaller powder quantities: 5mg-20 mg. A straightforward solution is to extend the use of nozzle dosators (by reducing the diameter of nozzles) and take advantage of the features already available for this technology: large output, highly automated, check weight for quality control of every single capsule. However, this requires understanding the design space for nozzles of smaller diameter and to revisit the effects of process parameters and powder properties on capsule quality. It is expected that miniaturizing the nozzles will affect the process performance and capsule quality.
In the current research, Design of Experiments (DOE) as part Quality by Design approach is used to study the effects of process parameters and material properties for three small nozzles on fill weight and weight variability. A capsule filling machine (Labby, MG2) with a single ND is used.
Materials and Methods
The DOE (D-Optimal with Design statistics G-Efficiency) includes four process parameters of the capsule filling machine (Labby, MG2): 1- Diameter of the nozzle (3 different nozzles), 2- Size of dosing chamber (three sizes), 3- Depth of powder bed in the bowl (3 values), and 4- Speed of capsule filling (3 values). The DOE also considers two interactions between process parameters: 1- Size of dosing chamber and powder layer depth; and 2- Diameter of the nozzle and size of dosing chamber. The DOE has two constraints for the ratio between size of dosing chamber and layer (interaction 1): never smaller than 1:2 and never larger than 1:5 (which are typical values found in capsule filling machine set-up).
The materials are four different grades of lactose: Respitose ML001, ML006, SV010, and SV003 (DFE). The following material attributes are characterized (in triplicates): particle size and shape; bulk and tapped density; compressibility; 3 flow indexes (Carr index, Basic flowability energy (measured with FT4), and ffc (measured with FT4)); cohesion (measured with FT4), wall friction, and air permeability (measured with FT4).
In order to precisely assess capsule fill weight, and hence guarantee the validity of the conclusions of the current study, we follow the following procedure:
- Weighing of empty capsules: The powder is filled into size 3 gelatin capsules, which are approximately 48 mg ± 3 mg. The empty body of capsules is much heavier than the powder fill itself. The variability in the weight of the empty capsules (± 3 mg) is almost as large as the low-dose content (5 mg). Therefore, the weight of the empty body must be known before filling capsules. Empty capsules are weighed and numbered for identification before filling.
- Use a high precision scale in our experiments: DENVER SI-234A (Readability: 0.0001 g; Reproducibility: 0.1 mg).
For each run in the DOE, capsule filling is performed with MG2 equipment (Labby) and the method is as follows:
- Fix the size of the dosing chamber with the aid of adjustment gauges (2.5mm, 3.75mm, and 5mm).
- Fill capsules for 5 minutes to reach steady state of the operation.
- Collection and weighing of the first group of 20 numbered capsules.
- Continuously run the machine for 5 minutes.
- Collection and weighing of the second group of 20 numbered capsules.
- Compare the net weight of the two groups of capsules.
- If the fill weight of the two groups of capsule does not differ by more than 10%, then the data is combined in a single group (a batch of 40 capsules).
Results
First, the effects of four process parameters and two of their interactions on fill weight and weight variability for four powders is discussed. The lines in Table 1 corresponds to each run in the DOE and show the values for each of the four process parameters, and the fill weight and weight variability for each of the four powders tested. At the bottom of the columns named weight and weight variability for each powder, we indicate the parameters that significantly correlate with each of these two capsule attributes. For instance, fill weight always correlate with the diameter (dia) of the nozzle and the size of the dosing chamber (cha). Hence, filling is performed on volumetric basis.
At the bottom of the columns for weight variability, the parameters that affect fill weight variability are indicated. These parameters depend on the type of lactose tested and nozzle diameter (dia) is always one of them. The interactions between process parameters do not significantly affect either fill weight or weight variability.
Table 1: Effect of process parameters on fill weight and weight variability for four different grades of lactose (Respitose ML001, ML006, SV010, and SV003).
Then, the effects of material attributes (for the group of four powders) on fill weight and weight variability is discussed. Figures 1 and 2 show the material attributes that have a statistically significant correlation with fill weight and weight variability respectively. Bulk and tapped density have the largest correlation with fill weight. Many material attributes affect weight variability, however their effect is rather small (see small coefficients on y axis of Figure 2). Particle size shows the largest correlation with weight variability.
Figure 1: Material attributes that affect fill weight. Bulk and tapped density show the strongest correlation with fill weight.
Figure 2: Material attributes that affect fill weight variability. Many parameters have a small effect but still statistically significant. Particle size has the largest effect on weight variability.
Conclusions
The current study uses QbD principles to understand the effect of process parameters of a nozzle dosator capsule filling machine and material attributes on fill weight and weight variability of capsules with low fill content. This study is focused on low fill weight (5mg-45mg). In order to fill these amounts of powder, nozzles with smaller diameters than the traditional nozzles (sizes 0 to 5) are required.
For the powders tested, fill weight is affected by the diameter of the nozzle and the size of the dosing chamber. Diameter and size of the chamber are the two parameters that define the volume of the dosing chamber (the R2 of models is at least 90%). Hence, filling is performed on volumetric basis.
The material attributes that have the largest effect on fill weight are bulk and tapped density. Many material attributes affect weight variability, even though their effect is rather small.
Acknowledgments
To MG2 and GSK for their financial and scientific support
References
Jones, B.E. (2001). The filling of powders into two-piece hard capsules. International Journal of Pharmaceutics 227, 5-26.
Newton, J.M. (2012). Filling hard gelatin capsules by the dosator nozzle system - Is it possible to predict where the powder goes?. International Journal of Pharmaceutics 425, 73-74.