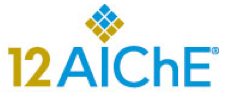
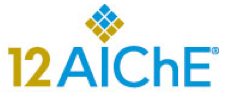
Evaluation of Management of Safety Barries for Major Hazard Accidents
The last accidents in the process industries have demonstrated and intensified the importance of the safety barriers to prevent the occurrence of accidents.
The safety barriers, that are called preventive, if the barrier could avoid the occurrence of accidents, or mitigating, if that minimizes the consequences, can be identified by Preliminary Hazard Analysis, HAZOP or LOPA studies, but no formal methodology is well established to evaluate the integrity of this barriers. Normally, they are taken for granted and considered to be operating well, based on information from
The purpose of this methodology is to evaluate the safety barriers management, with focus on major accidents, in other to monitor the barriers integrity. In order to evaluate this, an audit methodology has been developed to identify possible gaps on the management of the safety barriers. This process analyses the main barriers and safeguards used in the process industries risk analysis and it is usually conducted by the plant safety process team with the support of the other areas: inspection, maintenance, instrumentation, engineering, safety and environment.
Best engineering and process safety management best practices have been used to define the requirements that a barrier should follow to guarantee its well established management. For each type of barriers there are questions related of the barriers management.
A protocol, specific for each scenario identified on the risk assessment studies, is used, as illustrated in Figure 1.
For Inspection and Maintenance Program, as an example of preventive barriers, some questions are key for the management of this: existence of inspection plan; documentation of the plan; inspections performed according; and management of recommendations from inspections; revision and update of the plan. All these question shall be answered considering the specific conditions of the system, equipement or instruments involved on the scenario.An example is indicated in Figure 2 bellow.
These questions must be answered with YES or NO and at least one NO answer is indicates that the barrier is potentially compromised. In other words, if one step of the management cycle is not being performed, this can lead to a potentially comprimised barrier that can lead to an accident, considering the Swiss Cheese Accident Model from James Reason.
The results of the barriers audit indicates that the potentially compromised barriers what will generate an action plan for barriers integrity management. Both specific and systemic actions are identified and shall be implemented in order to guarantee the better management of the safety barriers.
Main differentiator of this methodology and sistemic approachs for Process Safety Management System evalution is the focus on the barriers and requirements for its management.
Additionally several indicators and statistics can be generated over the process of auditing, evaluating areas that requires greater investiments (as safety, maintenance, inspection, instrumentation), best practices can be shared among different sites of same company and an overview for communication with leadership can be developed, bringing a new view of the process safety management system.