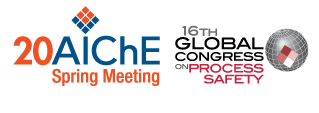
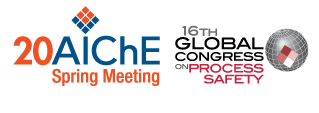
Names and affiliations: M. Kusenberg1, N. Mys2, K. Ragaert2, A. Zayoud1, M.R. Djokic1, S. De Meester2, U. Kresovic3, N. Alderweireldt3, K.M. Van Geem1
1 Laboratory for Chemical Technology, Ghent University, Ghent, Belgium; 2 Department of Green Chemistry and Technology, Ghent University, Ghent, Belgium; 3 Indaver N.V. Belgium, Mechelen, Belgium
Abstract
During recent years, energy and carbon efficiency became increasingly important in the transition from a linear to a circular economy. In this scenario, recycling of plastics plays a key role due to their energy and material intensive production, their abundant use and their long lifetime as a pollutant.
Post-consumer plastic waste is a mixture of several different polymers such as polyethylene (PE), polypropylene (PP), polystyrene (PS), polyvinylchloride (PVC) and polyethylene terephthalate (PET), which further contain a number of additives and auxiliary materials such as stabilizers, flame retardants, plasticizers and colorants. The high complexity makes mechanical recycling challenging due to certain limitations regarding waste separation and re-use of materials (i.e. food-contact applications, value-added materials). Therefore, thermochemical decomposition into base chemicals represents a promising technology towards circular economy.
In this work, several different plastic waste streams have been pyrolyzed in a continuous pilot setup consisting of a single-screw extruder connected to a heated 5 L stirred-tank reactor vessel and a system of condensers downstream of the reactor. The heated single-screw extruder is used to melt the plastic and convey it to the reactor. Products leave the reactor in a gas state and are condensed in the downstream section of the pilot setup. Reaction conditions range from 400 to 450 °C, 0.1 to 5 bar(a) and feeding rates from 1 to 3 kg/h. Plastic feedstock is either pure virgin material (PE, PP, PS), virgin blends that resemble real waste composition or real post-consumer waste (PE/PP-foils, mixed polyolefins (MPO)). This way, influence of the feedstock composition as well as real-waste contaminants such as dirt, missorted polymers such as PET or PVC or additives can be investigated.
Pyrolysis products of PS have a rather simple composition with the major constituent being styrene monomer. Pyrolysis of MPO or PE-foils however, yields a complex spectrum with a wide carbon range (up to C50) and a wide distribution of compound families (n/iso-paraffins, olefins, monoaromatics, mononaphthenes), which strongly depends on the plastic feed composition and the pyrolysis conditions (temperature and pressure). Furthermore, pyrolyzates can contain heteroatoms such as sulphur, oxygen, nitrogen, halogens and metals which on the one hand diminish the quality of the pyrolyzates as well as the steam cracking products and on the other hand harm process equipment such as pumps, flow controllers and metal surfaces. Contaminants are and will be the determining factor to decide if chemical recycling via a combination of thermochemical conversion of post-consumer plastic waste and steam cracking is feasible
To assess this, bench scale steam cracking experiments of untreated pyrolyzates from real post-consumer MPO and mixed foils have been performed at coil outlet temperatures from 820 °C to 880 °C, coil outlet pressure of 1.7 bar(a) and steam dilution of 0.5. Results show that light olefin yields are in range with those of fossil naphtha cracking. However, the coking tendency of these pure, untreated feedstocks is twice as high compared to a reference naphtha cracking. Different blends of these plastic waste oils with naphtha have also been studied and show great potential, as it is unlikely that a full steam cracking plant will be running on chemically recycled oils due to different economy of scales.
Our research clearly shows that cracking of post-consumer plastic waste is feasible with reasonable product yields and coking tendencies. The products show great potential for further direct utilization (i.e. styrene) or as steam cracking feedstock after treatment. Moreover, pre-treatment of the waste could diminish drawbacks such as blockages or low quality pyrolyzates. Future work aims to combine the feeding of the plastic waste to the reactor with a thermal pre-treatment within the extruder by variation of temperature, application of vacuum and screw speed. This way, volatile organic compounds, halogenic contaminants and a range of added compounds can be removed from the plastic melt prior to pyrolysis.
Presenter(s)
Language
Pricing
Individuals
AIChE Member Credits | 0.5 |
AIChE Pro Members | $19.00 |
Fuels and Petrochemicals Division Members | Free |
AIChE Graduate Student Members | Free |
AIChE Undergraduate Student Members | Free |
AIChE Explorer Members | $29.00 |
Non-Members | $29.00 |