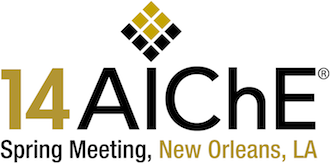
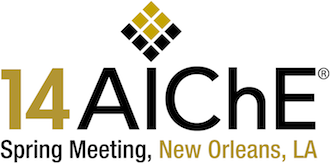
FM Technologies, Inc. (FMT) has developed new methods for joining SiC-to-SiC and SiC-to-metal for use in ethylene production. Global production of ethylene from olefin plants reached over 150 million metric-tons in 2012 according to GPCA, making ethylene one of the largest, by volume, chemical commodities in existence today. The United States is one the largest producers, with Petral Consulting estimating US ethylene production at more than 25 million metric-tons, about 1/6th of global production, in 2012. EIA’s latest annual energy outlook lists proposed additions to US ethylene production capacity of more than 10 million metric-tons from 2013 through 2020. Ethylene production involves the cracking of liquid or gaseous hydrocarbon feedstock in the presence of steam at low pressures and elevated temperatures inside pipe coils within a pyrolysis furnace. These coils are subjected to some of the most severe operating conditions in the petrochemical industry, experiencing extreme thermal cycling, coking, carburization, oxidation and creep during service, often resulting in reduced service life and premature pipe failures. Presently, most coils are made from a family of modified HP Ni-Cr alloys combined with small amounts of either Mn, Al, Ta, Ti, Si, Nb, W or Mo to enhance carburization and creep resistance and minimize coking. This family of HP alloys seems to have reached their useful operating limits as the past few decades have seen a trend of increasing furnace temperature in efforts to increase yield and efficiency from the endothermic cracking process. Conventional metal coils in general have always been hindered by temperature limitations and the frequent maintenance required for coke removal. Silicon-carbide (SiC) ceramic tube, on the contrary, has nearly double the service temperature of the metals currently used in today’s ethylene furnaces and is inherently resistant to carburization and coking. The use of SiC tube in the firebox of the furnace in place of the usual metal coil would allow processing at significantly higher temperatures, greatly improving the energy efficiency and yield of the ethylene cracking process. However, producing SiC tubes long enough for practical use has proven challenging. The novel high-temperature joining methods developed at FMT circumvent this issue by allowing easily manufactured 15-20ft SiC tubes to be joined end to end to form a complete furnace coil, and then allows for the ceramic coil to be joined to standard metal tubing at the ends of the firebox. The joining is accomplished by various methods through the use of a proprietary mix of joining materials. Sample joints and their performance results will be presented. Demand for improved coil technology is high, with annual tube consumption by ethylene producers exceeding $600Million, and the joined SiC tubing presents a significant jump in performance over what is currently in use today. This is especially important for the current boom in US ethylene production, as new plants will certainly be implementing this sort of game changing technology to ensure the most return on the $1-$4Billion investment required to build them.