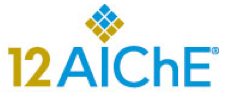
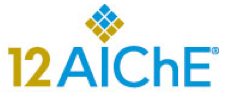
Abstract For 8th Global Congress on Process Safety
(Process Plant Safety Symposium)
April 2012
One Company's Near Miss Program - Successes, Learning, and Improvements
Shakeel H. Kadri
Glen A. Peters
James VanOmmeren
Air Products & Chemicals Inc.
7201 Hamilton Blvd.
Allentown, PA 18195 USA
Process safety near misses and incidents are a key indicator of a company's process safety performance. The goal in reporting and evaluating near misses is to improve Operators' hazards awareness by recognizing unsafe conditions and acting on less severe near miss events before they escalate into more severe Tier 1 and Tier 2 type process safety incidents. Near miss analysis can also be used to identify themes and trends that a company should focus on to improve process safety risk management at their facilities.
Air Products and Chemicals, Inc. has been reviewing process safety near miss events for many decades but has developed and fine-tuned a detailed and systematic Near Miss Program within the last five years. The current program is modeled after CCPS guidelines with specific provisions for unique hazardous materials that Air Products handles. This presentation will describe the global management program, which must deal with the challenges of approximately 1,500 plus process safety near miss entries per year; worldwide operations in over 40 countries; many different business units; and very diverse hazardous materials, systems, and services provided globally. The breadth of the Near Miss Program, from technician to executive, and the depth of the program, from initial design to plant decommissioning, will be presented. Near Miss Program learning and improvements will be described that have enabled Air Products to efficiently analyze near misses, identify improvements in our process safety management program, as well as functional work processes, and effectively communicate global leadership improvement messages addressing near miss themes and trends to help support our Process Safety performance continuous improvement goals.