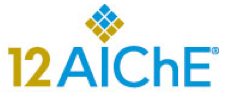
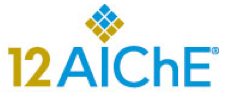
With the increase in requirements for monitoring and improving process safety indicators on a thermoelectric unit linked to a Braskem Basic Petrochemical Site in Brazil, a large range of knowledge among engineers and operators were found.
The theme Process Safety was commonly confused with operational continuity by the operators. Teams that interact daily with the plant could mistenkenly consider a jump protection as a pocess safety action, because it could prevent an unexpected trip in a given situation, interrupting production.
The creation of a team, with participants from all shifts could develop a culture of process safety at the operational level, involving them in the following actions:
1) Monthly monitoring of indicators requested by the leadership (process safety index), an operator of each group is responsible for reporting monthly an indicator element.
2) Presentations done by the plant engineer exposing on procedure of risk analysis, the dissemination of the risk matrix of the unit and the discussion of the worst scenarios.
3) Workshop of Discussion of critical procedures. Each year a critical operating procedure is chosen for discussion with operators and engineers with the purpose of review and equalize practices applied by day-by-day team.
4) Creation of Cine Process Safety. Monthly a movie explaining a big process safety accident is shown in the control center for discussion of lessons learned between the groups.
The results obtained by the group are intangible, but the understanding of process safety risks is essential for operational discipline, accuracy in permission to work and compliance with procedures and routines.