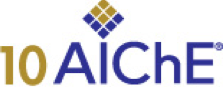
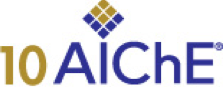
Ethylene producers have faced the challenge of feedstock contaminants for decades. However, with current industry transitions and surplus capacity, the low cost producer will have a real advantage in terms of survivability. The ability to leverage opportunities to improve the cost position on feedstocks as well as the ability to process flexible feeds, including mercury contaminated distressed feeds, will enhance the competitive position of ethylene producers. Although the level, as well as type of mercury present, varies substantially in different hydrocarbon fractions, mercury is a known contaminant present in ethylene plant feeds.
Mercury removal in ethylene plant feeds is desirable for both safety and operational reasons. Accumulation of elemental mercury in the cold sections of the ethylene plants is a safety concern due to potential exposure of employees to mercury during plant turnaround and maintenance activities. Mercury may cause corrosion of aluminium plate-fin heat exchangers typically used in the cryogenic sections of ethylene plants. In addition, poisoning of the hydrogenation catalysts in the acetylene and MAPD converters is another motive for mercury removal.
Although adsorbent based solutions are a cost effective option for mercury mitigation, it is critical to understand the complex issues of mercury species that can be removed by various products, and the options regarding treating the feed to the cracker versus treating the cracked products from the furnace. Selection criteria for matching adsorbent products with specific streams, as well as economic considerations of various options for total mercury containment in ethylene plants will be discussed.