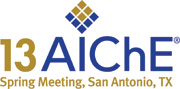
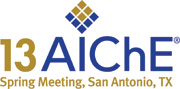
As in other industries, we in the explosives manufacturing industry have got safety policies and procedures, we do regular safety audits and we try and usually do comply with any available safety standard. However, despite all this paperwork, time and attention our industry continues to carry a fair number of safety incidents, the vast majority of which could have been anticipated. Conclusively, it can be said that for a whole variety of reasons there is in most cases a lack of attention to basic explosive safety, or so called BOS (Basis of Safety) in the explosives industry. in simple words, BOS is a set of simple established principles to do just two things: 1) prevent unintentional explosions (by preventing ignition) and 2) manage the consequences of a potential explosion.
The consequent application of BOS principles ensures that all (process) controls are appropriate and in place.
BOS is based on the principles of using lines of defences to block hazards from turning into incidents. These lines could be:
- Inherent Design (e.g. remote operation, process equipment), plant layout (e.g. inventory, separation of processes, safety barriers), Hazard Studies
- Learning from the past
- Individual operator controls
- Workplace controls
- Organizational controls
BOS principles are intended to assist all personnel involved in designing explosives manufacturing operations, working in these and handling explosives and sensitive (raw) materials to understand:
- The hazards associated with those materials
- How hazardous conditions can arise under normal and abnormal situations/process conditions
- How to avoid those hazardous conditions arising (prevention of ignition sources)
- How to minimize the consequences in the event of an incident
Application of BOS principles is not a separate exercise, but does complement existing safety management and QC systems.
To characterize and be able to control ignition sources and with this an explosion hazard, we need to understand what is happening. These are the conditions for an ignition or the sequence of events.
Firstly, in the sequence, if there is no explosive material present then there won't be an explosion. So, if these materials can be prevented at early stages in a production process or be kept to a minimum, this should be done. From a plant design perspective, this could be a change from a batch to a continuous process.
Secondly, in the sequence adding any energy to explosive materials can potentially trigger an initiation leading to ignition. Preventing of ignition is the best place to intervene to stop the chain of events leading to an explosion. Ignition sources in the explosives industry can be summarized as FISH which are Friction (between surfaces), Impact (between impacting or colliding surfaces, increase of pressure and temperature), Static (electrostatic discharge) and Heat (fire, decomposition, adiabatic compression, radiant heat, prolonged friction). Most explosive substances are well characterized regarding their sensitivity towards ignition sources. However, they can behave differently under slightly changing process or operating conditions and may become unpredictable. Therefore, the process design has to take a very conservative approach.
Examples will be given who these principles are applied in designing processes, Hazard Studies and R&D.