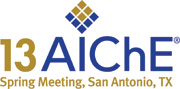
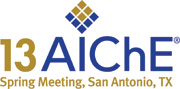
For several years organisations involved in high hazards operations have reported their process safety performance in terms of lagging indicators or “after the fact” measures such as loss of containment. These measures are naturally important to the company, the industry and the wider public. Nevertheless major hazards businesses are increasingly dissatisfied with basing their future strategy entirely on lagging indicators. This has been likened to driving a car using the rear view mirror and can result in equally disastrous consequences. From a control perspective, feed forward as well as feedback control is desirable. What are needed are indicators that drive improvement. Leading indicators for process safety offer a way of examining the contributing factors to accidents and putting in place a system for monitoring these factors in a tangible process. In this manner early warning signals can be acted upon and the progress towards zero accidents can be assured in a meaningful way.
In 2012 the European Process Safety Centre(EPSC) published a document on the selection, development and implementation on leading indicators for process safety which shared details on the type and spread of indicators which members have established within their own companies. In addition EPSC provided several practical tips for the do’s and don’ts of successful implementation including presentation of data and engagement of staff. This talk is to develop these aspects further whilst exploring the relationship between leading indicators on a plant, business unit and corporate level. Additionally the interaction between leading and lagging indicators is to be highlighted alongside the management space which process safety indicators now inhabit with respect to monitoring and audit/review activities.