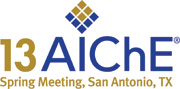
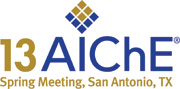
Introduction
The use of electric and electronic equipment has been more frequently propagated in the facilities of industries, pilot-plants and laboratories. This equipment is a source of ignition for inflammable clouds, thus elevating the risk of fires and explosions. The “area classification” methodology tries to avoid these scenarios. Although traditionally used in the industry, the area classification is very seldom employed in the academic environment (like pilot-plants and laboratories). Even employing equipment of smaller dimensions, the laboratories and pilot-plants are not environments free of risks (CSB, 2010).
This study presents, as its main objective, an evaluation of the need to apply a classification of the area for distillation pilot-plants. The adopted methodology is based on the NFPA 497 rule.
Pilot-Plant
The distillation unit studied herein was projected for “fuse oil” processing. The term “fuse oil” originated in Germany, and is employed to describe alcohol mixtures obtained during purification phases. In Brazil, the fuse oil (“óleo fúsel”) is known as the heavy fraction of a distillation process of the alcohol fuel. The separation of its components, especially the ethanol, is obtained through the distillation column.
The methodology proposed by NFPA 497, is based on the operational conditions. Temperature, pressure, flow on pilot-plant were described. The evaluated unit presents a volume smaller than 19m³, a leak smaller than 23m³/h and a pressure lower than 7kgf/cm². Therefore, these parameters were classified as being “smalls” or “lows” (NFPA 497). From this information on, as well as from the layout of the plant, it is possible to define the “reference figure”. In the studied case, the rule indicates the figure “5.10.1” (NFPA 497). With the test pilot-plant’s project and the “reference figure”, one may define the surrounding area of the equipment.
Classification of the Area
The employment of the “reference figure” at the pilot-plant results in a classified area of 1.52m of ray around the distillation column (NFPA 497). The column is 1m high from the ground. For elevated equipment, the rule recommends to adopt, as a complementary way, a protection ray of 7.62m at ground level (NFPA 497). A similar classification methodology was adopted for the feeding and product vases, condensers, etc. As a final product of an individual classification of the equipment, one may obtain the general trace/mark. This result is obtained with the fusion of the classified area of all equipment, separately.
The importance of the area classification
From this analysis it is possible to define that the classified area surrounding the equipment presents significant dimensions. Such area embraces not only the electric equipment employed in the operation of the test pilot-plant, but also other plants installed in the proximities. The presence of inadequate equipment or electric installations in this area elevates the risk of fires and explosions.
From the studies developed, it is possible to conclude that the adoption of classified areas seems to be relevant in order to improve the process safety, even in the academic environment. Although the operational conditions are lighter than the ones observed in the industry, and the dimensions of the equipment are smaller as well, the formation of inflammable clouds of significant sizes appears to be possible. The leaking of inflammable material together with the presence of inadequate electric equipment − regardless whether in academic or industrial environment − may result in scenarios of elevated risks.
CSB (2010): “CSB Release Investigation into 2010 Texas Tech Laboratory Accident”