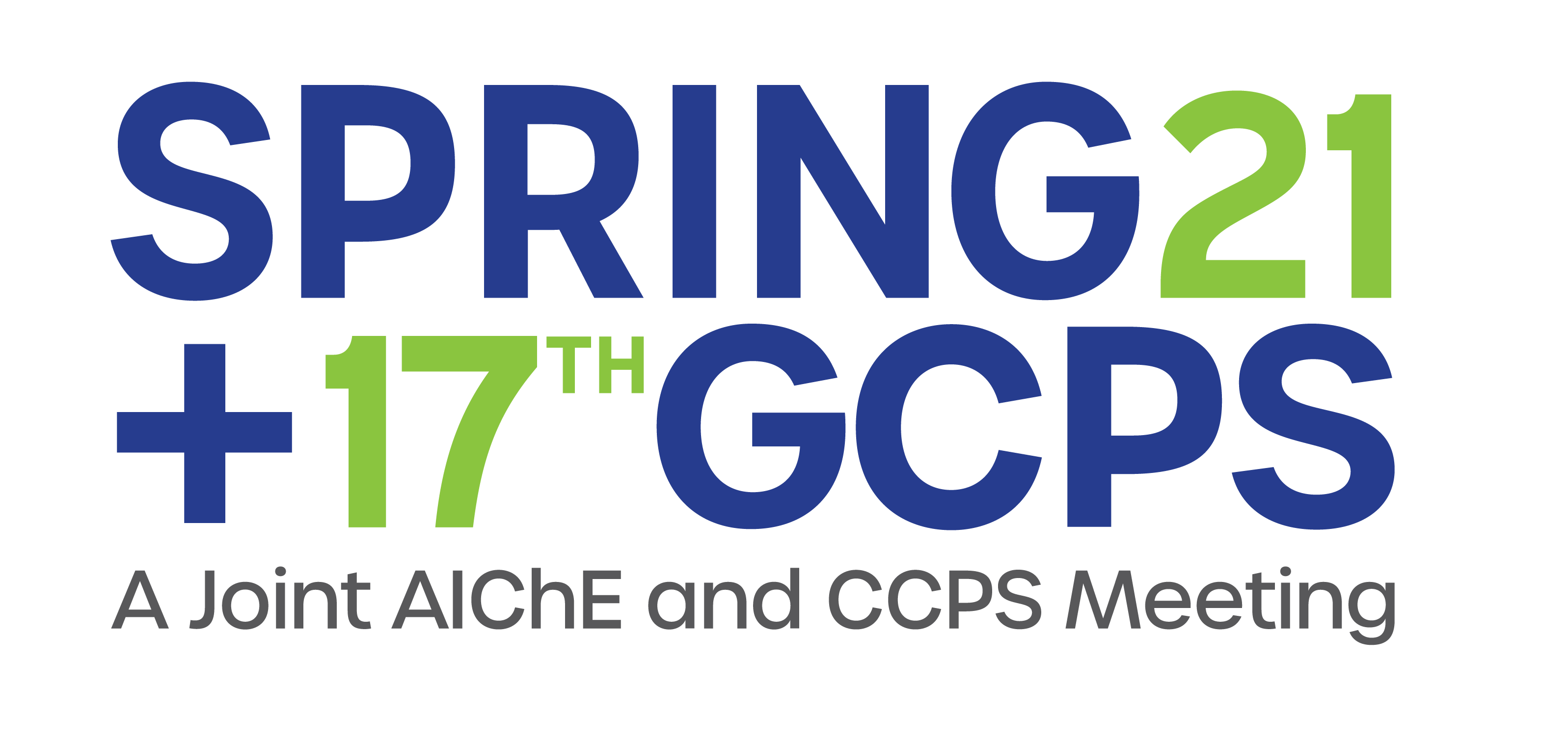
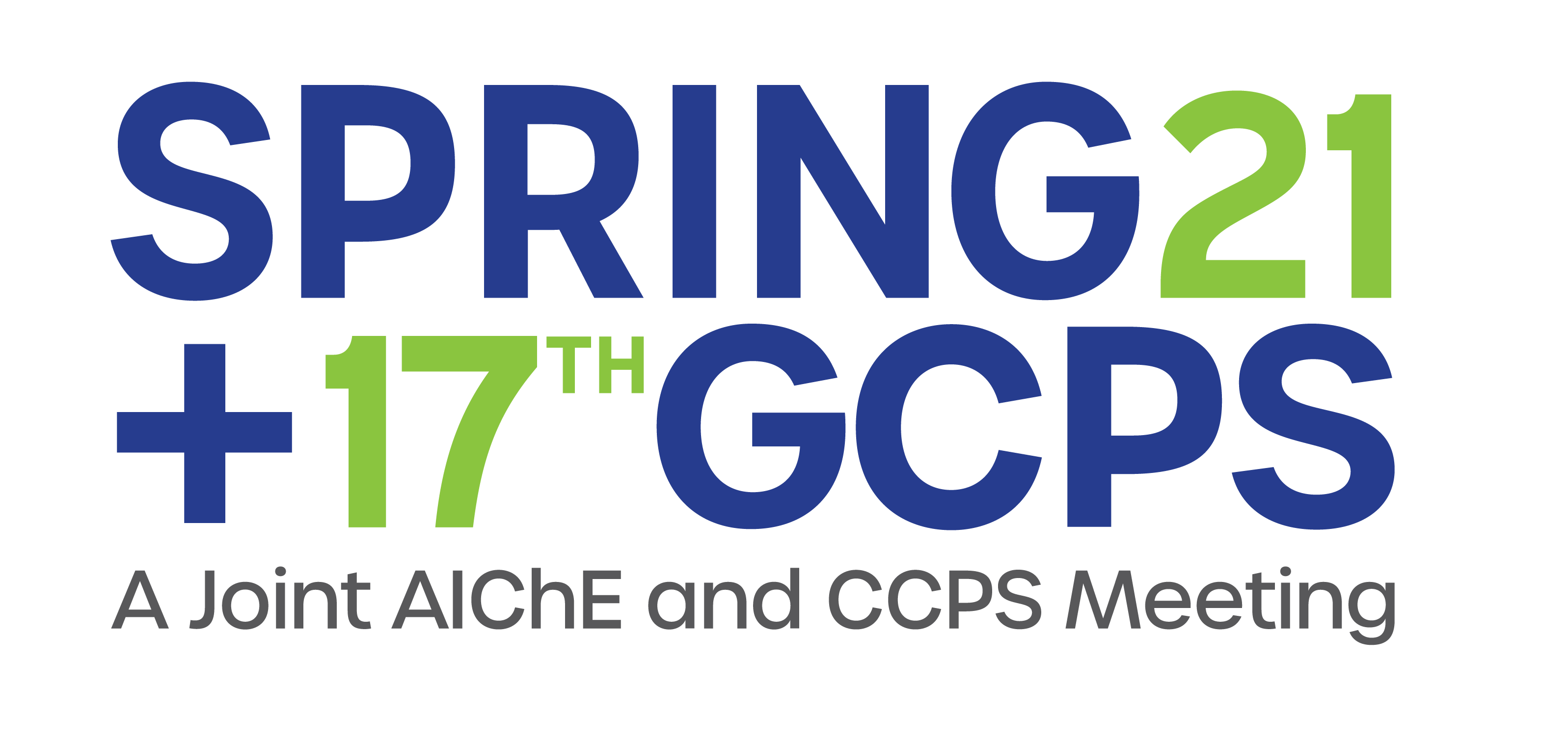
A specialty chemicals facility was exploring how to minimize product yield losses while maintaining quality in several of its existing distillation trains. The original instrumentation & control schemes had become less reliable and generated unsatisfactory results as the units were pushed for greater production and recovery, requiring manual intervention & control by the Operators. A process control consultant was asked to assess the existing controls structures & instrumentation and recommend revisions that would achieve the desired objectives without requiring operator-intervention. The Consultantâs activities centered around answering the following questions:
- What is the appropriate measurement that best infers the quality objective(s)?
- Are there any instrumentation or equipment deficiencies that must be resolved?
- How should the controls be structured to reliably achieve the plantâs objectives in real time?
This paper describes the analysis procedures and methodologies that were used to generate the recommended instrumentation & control modifications, as well as some of the surprising (and not so surprising) discoveries that were made during the assessments. The preliminary results of the recommended control modifications will also be presented.