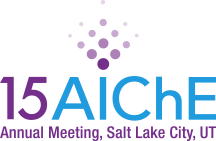
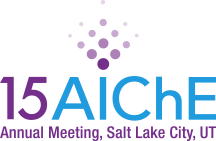
Regulatory Process Control of an Advanced Post-Combustion Amine Scrubbing System
Matthew S. Walters, Thomas F. Edgar, Gary T. Rochelle
McKetta Department of Chemical Engineering, The University of Texas at Austin, 200 E. Dean Keeton St. Stop C0400, Austin, TX 78705
Keywords: amine scrubbing, dynamic modeling, pilot plant validation, process control
Amine scrubbing is a leading technology for capturing CO2 from fossil fuel power plant emissions. The in-and-out intercooled absorber1 and advanced flash stripper2 process configuration (Figure 1) using concentrated piperazine solvent has been proposed to reduce the capital and operating costs associated with separating CO2 from flue gas and compressing it for geological sequestration. A low-fidelity dynamic model of this advanced process has been developed and implemented in MATLAB® for the purpose of screening regulatory process control strategies. The low-fidelity model has been validated with both a high-fidelity model and pilot plant data, and it is valid for simulating the system near the design conditions.
The primary process control objective of an amine scrubbing plant will likely depend on environmental regulations, electricity markets, and enhanced oil recovery (EOR) economics. Two possible objectives are proposed here: delivering a constant rate of CO2 to an EOR facility and maintaining a 90% removal rate in the absorber. We consider a capture unit integrated with a base-loaded coal-fired power plant that experiences disturbances in boiler load of ≤ 5%. Steam is extracted from the power plant turbine intermediate pressure/low pressure (IP/LP) crossover. The steam extraction valve is assumed to be 100% open at design conditions, which limits steam availability during a disturbance. The off-design turbine operation is predicted using Stodola's Ellipse Law.
In the constant CO2 delivery case, the compressor is flow controlled to meet the specified CO2 rate and the CO2 inventory in the solvent is allowed to vary. In the case where removal rate from the flue gas is controlled, two choices for manipulated variables are examined: the solvent circulation rate (set by the lean solvent pump) and the CO2 delivery flowrate (set by the compressor speed). After assigning manipulated variables for level and water balance control, the remaining variables are paired with self-optimizing process variables.
With constant CO2 delivery, the removal rate in the absorber floats for a period of several hours when a disturbance is introduced. Because the process variables spend long periods away from steady state, the steam extraction rate is also floating. The process is not optimal when it is away from steady state, and there is an energy penalty associated with the transient period. There is also a clear tradeoff between electricity produced and the amount of CO2 available for EOR. This scenario may require an oversized compressor to avoid reaching the capacity limit as the pressure of the stripper drops. In the event of a sustained disturbance, the CO2 inventory may become depleted and cause the solvent to approach the solid solubility limit. No oscillations in process variables were observed in this scenario.
As a result of the heavy material and energy recycle in the process, maintaining a constant removal rate in the absorber is challenging with only feedback control3. Manipulating solvent rate to control removal with a small process inventory leads to significant oscillations in process variables. The oscillations could possibly be reduced by less aggressive tuning or a larger lean storage tank; however this will make the response much slower and a large inventory is likely not acceptable. These observations are consistent with previous work that investigated using solvent rate to control removal on a simple absorber and reboiled stripper with monoethanolamine4,5. Without any knowledge of the absorber, a feedback controller that manipulates compressor speed must be tuned non-aggressively to assure stability and is subject to slow oscillations as the system comes to steady state. A model-based supervisory controller is proposed to improve upon this strategy by making control moves that take into account the heavy material recycle.
Figure 1. In-and-out intercooled absorber with advanced flash stripper configuration.
References
[1] Sachde D, Rochelle GT. Absorber Intercooling Configurations using Aqueous Piperazine from Sources with 4 to 27% CO2. Energy Procedia 2014;63:1637-56.
[2] Lin Y-J, Madan T, Rochelle GT. Regeneration with Rich Bypass of Aqueous Piperazine and Monoethanolamine for CO2 Capture. Ind Eng Chem Res 2014;53:4067-74.
[3] Walters MS, Edgar TF, Rochelle GT. Dynamic Modeling, Validation, and Time Scale Decomposition of an Advanced Post-Combustion Amine Scrubbing Process. Energy Procedia 2014;63:1296-1307.
[4] Ziaii SF. Dynamic Modeling, Optimization, and Control of Monoethanolamine Scrubbing for CO2 Capture. The University of Texas at Austin. Ph.D. Dissertation. 2012.
[5] Ceccarelli N, van Leeuwen M, Wolf T, van Leeuwen P, van der Vaart R, Maas W, Ramos A. Flexibility of Low-CO2 Gas Power Plants: Integration of CO2 Capture Unit with CCGT Operation. Energy Procedia 2014;63:1703-1726.