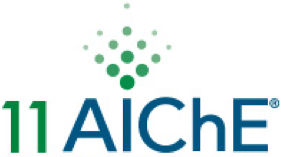
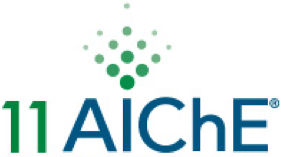
The production of stable biomass pyrolysis depends strongly on both reactor design and the effective design of a condensation train to collect the pyrolysis products. There are several challenges in the design of the pyrolysis system including solids feeding, char separation from the pyrolysis vapors, condensation of the pyrolysis vapors and compression of the non-condensible gases. In the feeding of solid biomass into the reactor, the feedstock properties such is softening point are critical in the feeding. Bridging properties are also very important and that is dictated by the method of biomass preparation, either knife milling or hammer milling. Hammer milled and disc-milled feedstocks tend to bridge easily whereas knife milled material bridges less. The reactor operating temperature is strongly influenced by the composition of the feedstocks. Biomass feedstocks such as poultry litter which are high in ash tend to form clinker in the reactor and therefore reactor temperature control is very critical for successful operation. The condensation train; especially with recycling of the gases tend to create major problems especially if an electrostatic precipitator is used to condense the aerosols. For systems employing electrostatic precipitator, the cooling temperature in the condensers must be very low because any water vapor escaping the condensers tend to cause electrical short-circuiting in the unit and reduces efficiency of the aerosol capture. Catalytic pyrolysis tends to produce more water and therefore the cooling system must be very efficient. The compressor for the non-condensible gases must be able to handle dirty gases (large clearances) otherwise it is easily clogged with the pyrolysis oils that tend to degrade the performance of the compressor and requires frequent replacements.
Presenter(s)
Once the content has been viewed and you have attested to it, you will be able to download and print a certificate for PDH credits.
If you have already viewed this content,
please click here
to login.