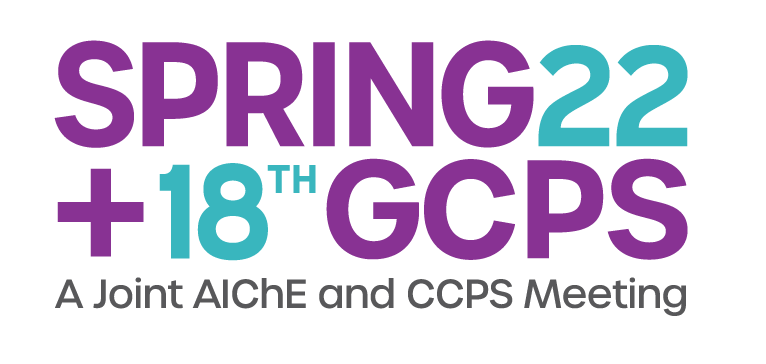
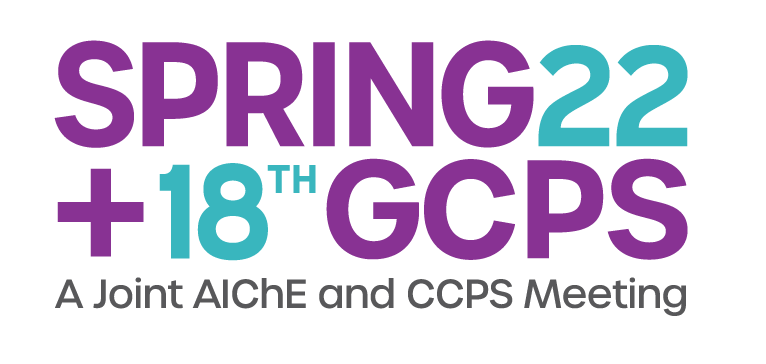
In the search for a solution to this problem Clark Solutions first came with a design using an intermediate inert fluid contained in a circuit of heat exchangers to avoid direct contact between these process fluids in the event of a leak for any reason. Acid cools the inert fluid in a exchanger, the inert fluid heats water in another exchanger in a continuous system. This approach was succesfull with a first industrial operation working for 2 years without experiencing a leak but, once the leak happened (due to a fabrication problem), this dis not led the plant to shut down or to any other major issue. In plant was kept running for the next 60 or more days, untill a planed stop for maintenance was arranjed and took place.
While the approach works fine, it is expensive: two heat exchangers, piping, pump, intermediate expansion vessel, instruments and inert fluid for filling the circuit.
The next step was developing a heat exchanger that could do everything above in a single piece of equipment. Safehx is what we denominate a buffered heat exchanger. It is actually a new class of heat exchanger where hot, cold and inert fluids are contained within a single vessel and where a leak of of of the process fluids avoid its contact with the other and vice versa.
Basically the process fluids are transported through two or more tube bundles in the upper and lower part of the shell and the inert fluid fills part of the shell volume. As the hot fluid flows it transfers heat to the buffer fluid which in turn boils and eveporates. The ascending vapors reach the upper cold fluid transporting bundle and cools down condensing the fluid vapors that precipitate back into the pool, in a continuous process.
In the research of this product we have found that it also can be used in those systems where a precise control of the tubewall temperatures are required such as in amine heating systems. Since the inert fluid vapors temperature are set by the fluid properties, eventough transferring a high heat flux, this is accomplished without letting the tubewall temperatures exceed the phase change temperature induced limit.
The concept also gives some extra degrees of freedom when building the equipment; since both fluids are transported inside tube bundles, these can be made in specific materials and the shell in another material, usually much less expensive, as the inert fluid is in contact with thes section of the vessel.
While the equipment was designed to cool sufuric acid avoinding the risk of failure due to a leak, the approach can be used in other service where the mixture of the hot and cold fluids are not desirable, even in the event of a failure, as well as, in sensitive materials.
Measured heat transfer coefficients are very near of those achieved in shell and tube heat exchangers.
We believe that the bufferred heat exchanger is a new class of heat exchanger that will find a niche position in some specific applications, such as the one described above.