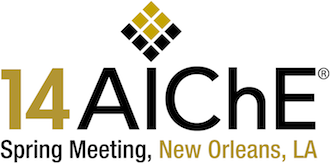
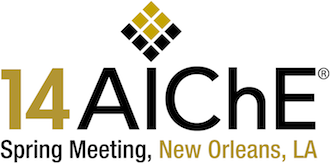
For as long ethylene has been produced via the steam cracking method, producers have searched for various ways of extending the time of operation between furnace de-cokes. Operators have optimized startup procedures, operational guidelines, fired burner patterns, tube sizes, designs, coatings, and have tried a variety chemical additives all with one aim in mind: Extend furnace run-lengths.
The benefits of longer runs are obvious: More time producing ethylene equates to more revenue. But there are many intangible benefits as well, including: Less risk of process upsets, longer tube metal lifetimes, reduced risk of environmental impact, and others. To help maximize all of these benefits, producers have accepted the hazards of dealing with less desirable chemicals like DMDS, or DSO to assist in delaying furnace coking.
Most all of these products are somewhat effective in delaying coking as they provide a source of sulfur (as H2S) to passivize tube metal nickel alloys that are known to catalyze the thermal breakdown of hydrocarbons to coke. However, these products all have limitations due to their inability to effectively generate H2S over a broad range of temperature, which is necessary for optimal tube passivation. Dorf Ketal’s new product is a polymeric sulphur compound that generates an even distribution of H2S beginning at much lower temperatures and continuing through high temperature ranges. The result is a more thorough passivation that reduces coking hot spots and extends furnace run lengths.
This paper will discuss the mechanisms of furnace coke formation and demonstrate the benefits achieved with a novel chemistry developed by Dork Ketal. This innovative new product is much safer to handle, is not regulated for transportation, has no objectionable odor, and most importantly, repeatedly yields significantly longer run times between de-cokes because of its superior sulfur releasing characteristics. This paper will present actual data from multiple installations around the world, from plants using a variety of feed stocks. A special focus will be given on applications in plants designed for liquids that are now attempting to crack lighter feedstocks.