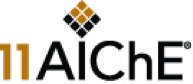
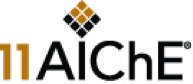
The production of fine chemicals and pharmaceuticals has been traditionally achieved via batch processes. More recently, there has been interest in using multiscale (meso- and micro-) reactors for the production of these fine chemicals and pharmaceuticals. These efforts in process intensification via meso- and micro-scale equipment are generally thought to have positive impacts in terms of smaller equipment footprint, significantly reduced in-process inventory, improved mixing control, excellent heat transfer and expanded operating conditions (higher temperature and pressure ranges).
However, the safety improvements accrued from this approach are usually case specific with trade-offs between the various factors. The potential for inherent safety of such an approach is enhanced by the reduced in-process inventory. Meanwhile, the opportunity to increase reaction rates (especially for micro-scale reactors) usually means running reactions faster, hotter and/or at higher pressures. Furthermore, the possibility for higher levels of process control could add another layer of complexity.
Cases of Reformatsky Reaction in literature have been known to be done batch-wise due to the unpredictability of zinc activation and exothermicity of the reaction stages. It is further complicated by the sensitivity of the Reformatsky reagent (zinc) to air and water. The INCOME (INtegrated COntinous Multipurpose Engineering) project in ICES aims to provide a platform to study various aspects of ?batch-to-continuous? processes. This gives us an opportunity to undertake the process development of a continuous Reformatsky chemistry and investigate its safety case.
As part of the process development effort, a full-suit of safety data was collected. This includes process calorimetry data, kinetics, vent sizing and physical/chemical properties of intermediates and products. This in turn was fed into safety assessments in the form of a Chemical Hazard Characterisation, Process Risk Assessment (PRA) and HAZOP. In these assessments, we have considered thermo-chemistry, control instrumentation, equipment coupling (downstream effects of deviations/perturbations) equipment integrity and fouling. Arising from these assessments, this paper will highlight and draw comparisons between the safety cases of batch and continuous Reformatsky processes.
Please note that due to the visual quality of this paper, there is no charge for it. The information is still valuable hence we are posting it here.